射出成形の基礎からコスト・納期対策への専門知識まで 射出成形をトータルに学ぶ
射出成形
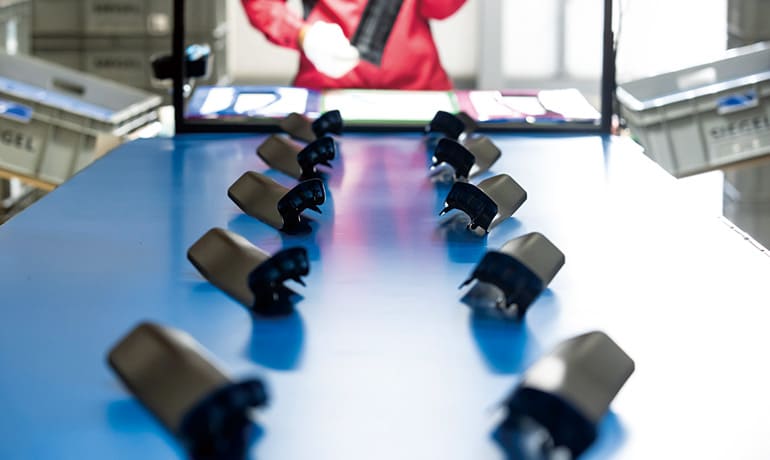
私たちの身の回りにあるプラスチック製品の数々。知っていましたか?私たちの身の回りにあるプラスチック製品のほとんどは、射出成形と言う工法で作られているのです。
この記事では、射出成形の基本的な知識から、メリットや注意点、さらには効率的に射出成形プロジェクトを進めるための専門情報まで幅広く紹介しています。特にプラスチック製品開発に携わる事業者様、設計者様にお役立ちいただけるようまとめております。
【射出成形ラボの簡易金型サービスはこちらより】
> 最短納期を2週間で!180ton射出成形機用の簡易金型を、60万からご提供いたします。
目次
射出成形とは?
プラスチックの成形方法は数多く存在しますが、特に金型を使用した大量生産工法としては「射出成形」「圧縮成形」「真空成形」「ブロー成形」などが挙げられます。その中でも代表的な成形方法が、今回ご紹介する「射出成形」です。
射出成形とは、射出成形機と呼ばれる機械を使用し、金型内に加熱溶融させたプラスチックを高圧で射出して成形する工法のことを言います。
複雑な形状・流麗な意匠面の再現性が高く、かつ大量生産を得意とする、最もメジャーなプラスチック成形工法です。
こちらの記事は動画でもご覧いただけます。
身の回りにある射出成形で作られた製品
前述したように、私たちの身の回りには射出成形で作られた製品がいっぱいです。まずはその中でも代表的な製品を3つほどご紹介します。
射出成形品 その① プラモデル
よくおもちゃ売り場にあるプラモデル製品。パーツがすべて繋がっており、それぞれニッパーで切って組み立てるプラスチック製の模型です。
実はこのプラモデル、射出成形機で成形された製品をそのまま袋に封入し、製品化されています。パーツがつながっている部分を『ランナー』、パーツ同士をくっつける穴を『ボス』、パーツの強度を保つための仕切りのようなものを『リブ』といい、こういった部分に射出成形で作られた製品らしさが特長として表れています。
射出成形品 その② 容器のふた
特に私たちの生活に欠かせない飲料水のペットボトル。このキャップ(蓋)も射出成形でできています。ロゴが印刷されていたり、触り心地が部分によって違ったり、内側はねじ構造であったりと非常に機能的で、射出成形の技術があの小さなキャップに詰まっています。
世界中で使用されているペットボトルのキャップ、射出成形の魅力の一つである大量生産で支えられています。
射出成形品 その③ 自動車を構成する部品
非常に大ロットかつ量産での射出成形といったら自動車部品が代表的でしょう。車の外観、内観ほとんどにプラスチック製の射出成形品が使われており、自動車一台を構成するのに射出成形品は無くてはならない存在です。
後ほど詳しくご紹介しますが、様々な種類の樹脂材に対応できる射出成形は、使用用途ごとに材質を変えることで、それぞれに適したプラスチック部品を作ることが可能です。
例えばドアそのものや取手部分、座席シート、内装の各パネル類、バンパー…etc。強度や触り心地、意匠面の美しさなど、各部品に要求される異なった機能を、材料を変えることで織り込ませられるのです。
射出成形の成形方法とは?
射出成形の工法はとてもシンプルで、加熱溶融させた樹脂材を高圧で金型内に射出して成形します。また、射出成形を行うには『射出成形機』という機械を使用します。
射出成形機を知ろう
射出成形機は射出(樹脂を発射する)装置と型締め(金型を締める)装置から構成されています。
なお射出成形においては、製品サイズや重量に合わせて適切な成形機サイズを選定する必要があります。成形メーカーごとに保有している成形機サイズが異なるため、ご検討中の製品サイズに適合する成形機を持っているかどうかは、成形メーカーを選定する上でとても重要なポイントです。
その点、弊社(株)関東製作所は、全国に180tonから1,800tonまでの幅広い成形機を完備していますので、サイズに関して不明点などある場合はぜひお声がけください。
[関連記事]
> 射出成形機を詳しく解説 成形の流れから構造、選定ポイントから射出成形品の製作事例まで紹介
「電動式」と「油圧式」射出成形機の違い
また成形機にもいくつか種類があり、性能や消費電力、メンテナンスのしやすさなどの点でメリット・デメリットがあります。特に代表的なのが「電動式」と「油圧式」と呼ばれる機種です。
電動式射出成形機
・消費電力エネルギーが油圧式成形機に比較して大幅に少ない
・低騒音で成形加工ができる
・成形工程を並列進行させることが可能なため、成形サイクルを短縮できる
・成形機の価格が油圧機と比較して割高
・サーボなので無理がきかない
・条件設定が難しい
油圧式射出成形機
・成形機の価格が電動機と比較して安い
・条件が出しやすい(幅が大きい)
・構造が単純なのでメンテナンスしやすい
・射出時間を非常に長く取る事が可能
・消費電力が大きい
・細かい制御が苦手
・作動油温度管理、品質管理が必要
射出成形機の「電動式」と「油圧式」それぞれのメリット・デメリットの詳細情報を、(株)関東製作所が運営する射出成形の専門サイト「射出成形ラボ」サイトにて掲載しています。
> 射出成形ラボサイトで「射出成形機の”電動式”と”油圧式”のメリット・デメリットを学ぶ - 成形機の性能は製品に大きく影響 -」の記事を読む
成形の流れを知ろう(動画で解説)
射出成形による製造工程は、成形機内部で、①樹脂を溶かし、②金型に流し込み、③高い圧力をかけて製品を作る。「溶かす」「充填する」「固める」の3工程が基本となっています。
プラスチックの成形原料の樹脂は「樹脂ペレット」と呼ばれ、射出装置内で溶けたペレットを注射器のように注入していきます。注入先には金型があり、流れこんだ樹脂ペレットが冷えて固まったのち、金型が開いて成形完了です。
また、下記動画は射出成形の工程を紹介した(株)関東製作所オリジナルの動画になります。プラスチックの原料を射出成形機に投入するところから、実際に成形品が出来上がるまでの詳細が分かります。
さらに射出成形ラボサイトにて、より詳しい射出成形の流れをイラストを用いながら説明しておりますので、そちらも併せてご確認下さい。
> 射出成形ラボサイトの「射出成形とは、複雑な形状・流麗な意匠面の再現性が高く、大量生産を得意とする、最もメジャーなプラスチック成形工法です。」の記事を読む
射出成形で使用する金型とは?
改めまして、プラスチックを決まった形にするための金属製の型を金型と言います。金型は、下図のように成形品の周りを囲んで凸部と凹部で作られています。
金型は、大きな鉄(アルミなどの場合もある)の塊を削り込むことで製品の形状を再現したり、成形機と連携させるために様々な機構を組み込んだり。そして何より、思い通りの製品を成形するため非常に高い加工・組付け精度が要求されます。
よって金型を作るにはそれなりの費用が掛かりますし、また量産金型なら完成させるまでに1カ月以上もの時間が掛かるため、それらを踏まえた予算・製造スケジュールを検討しておきましょう。
また機能面においても、金型を作る上での検討事項は非常に多岐にわたります。ここでは金型にとって特に代表的な要素「抜き勾配」と「アンダーカット」の2点をご紹介いたします。
金型の『抜き勾配』を知ろう
金型には『抜き勾配』という概念が必須です。読んで字のごとく『抜くための勾配』です。
抜き勾配が必要な理由は、射出成形後に成形機からスムーズに製品を離型させて、品質の良いきれいな製品を取り出したい為です。後ほど詳しくご紹介しますが、スムーズに離型出来ない(離型抵抗がある)と様々な『成形不良』に見舞われます。
例えば下図のように、成形品に勾配をつけずに作った場合、金型の固定側と成形品の間に抵抗が生まれ、製品を傷つけてしまう恐れがあります。
また、うまく固定側から抜けたとしても、図のように金型の可動側から成形品を取り出すとき、プラスチックの収縮の影響もあり、うまく成形品を取り出すことができません。そのため射出成形で製品を作る際には、せめて1~10°の抜き勾配をつける必要があるのです。
特に製品設計者の方は、製品デザインを金型に落とし込むことを想定し、前もって抜き勾配を織り込んだデザインを心掛けていただければと思います。
尚、抜き勾配についての詳しい解説は下記関連記事にてお読みいただけます。
[関連記事]
> 金型における『抜き勾配』を徹底解説! その重要性を学び、射出成形の不具合を回避!
金型においての『アンダーカット』とは?
アンダーカットとは、プラスチックの成形品を金型から取り出す際、金型の開閉方向には離型出来ない形状部分のことを言います。その形状部があるために、そのままでは成形品の取り出しが出来ないので、金型に改めて特殊な機構などを織り込む必要が出てきます。
アンダーカットを処理するには様々な方法が用いられますが、最も一般的な方法としては、金型にスライド機構を織り込むことでしょう。
金型に織り込まれるスライド
下図のように、アンダー形状部を金型分割し、金型の型開き方向ではアンダーとなってしまう形状部を、型抜き方向とは違う方向に摺動(スライド)させて、アンダーを解消させます。
分割する事により空間を作ることが出来、金型が抜けるためのスペースが生まれました。これでアンダーが解消されたことになります。
このようにアンダーカットを解消するために、一般的には金型内にスライド機構が採用されることが多いです。下記の関連記事では、アンダーカット処理のより詳しい手順と、スライドにもいくつか種類があり、それを紹介した記事もお読みいただけますので、併せてご確認いただければと思います。
【射出成形ラボの簡易金型サービスはこちらより】
> 最短納期を2週間で!180ton射出成形機用の簡易金型を、60万からご提供いたします。
[関連記事]
> 射出成形金型においての『アンダーカット』の基礎を学ぶ 金型から製品を離型する仕組みとは?
> スライドの種類、横スライド・傾斜スライドとは?金型のアンダーカットを解消する為の機構を学ぶ
またプラスチック金型全般の紹介記事もありますので、併せてご覧いただければ幸いです。
>プラスチック金型とは? メリット・デメリットや費用、ポイントなどを、製品開発支援企業が解説
射出成形の代表的なメリットとは?
ここでは改めて、射出成形を行うことで享受できる代表的なメリットをご紹介します。
メリット①:金型だからこそできる超大量生産!
金型はたった一つ作ってしまえば、そこから全く同じ外観・品質の製品を生産できます。ということは射出成形機を動かせば動かすほど、同じ製品を大量に生産できるのです。
基本的には一つの金型で、丁寧にメンテナンスを行いさえすれば、100万個以上ものプラスチック製品を成形する事が可能です。
メリット②:さまざまな樹脂材料に対応可能!
射出成形は溶けた樹脂を注射器のような細いノズルを通し、押し出して型へ流し込みます。よって溶かしてしまえば、ある程度の種類の樹脂なら概ね、同じ金型で対応できてしまうということです。一般的な樹脂であるPP(※)から、スーパーエンプラ(※)と呼ばれる超高性能プラスチックまで幅広く対応ができます。
また純粋な樹脂だけでなく、ガラス繊維や炭素繊維を配合して強度を高めた樹脂や、染料を加えて希望の色を着色した樹脂、絶縁性や対候性といった樹脂まで、用途に合わせた樹脂での成形が可能なのです。
- PP
- ポリプロピレンの略で、プラスチック素材の一つです。最も多く使用されているプラスチック素材の一つと言えます。
一般家庭で使用される身の回りのさまざまな製品に使用されており、家電製品や文房具、自動車用のパーツ、おもちゃやスポーツ用品など普段目にするものばかりで、その使用範囲は非常に幅広いです。
- スーパーエンプラ
- 金属に近い強度を持ち、金属の代替えとしても使われています。ロケットのパーツなどにも採用されているほどの優秀な素材です。
しかし高性能な分、素材費が高く、成形も特殊な設備が必要な場合もあるので、一般製品ではあまり使われていません。
メリット③:複雑な形状も再現でき、意匠面もとっても綺麗!
射出成形の最も特徴的なメリットは、意匠面の美しさを高めることであり、ギザギザした形状のデザイン、かわいい丸みを表現したデザイン、文字やロゴマークを入れるなど、細かく複雑な形状も再現できることでしょう。
成形機上で閉じられた金型の中に高圧力で溶けた樹脂を注入するので、金型の転写性が非常に高いのがそれを可能にする理由です。
また、カチッと嵌め込むスペースがあったり、穴が開いていたり、ヒンジがあってグネグネと曲げることができたり…。
そういった機能的な要素も後から加工を加える必要はなく、射出成形のワンショットで完成させることが出来るのです。前述したように金型の転写性が非常に高いので、製品設計時点で入念に機能性を詰め込み、型さえ作ってしまえば、その製品としての『機能』もそのまま再現しやすいのです。
製品によっては表面をメッキにしたり、質感をザラザラにしたりと、後から加工するケースもありますが、基本的にはワンショットの成形がそのまま製品となります。
この「後加工」という煩わしさが不要な点も、射出成形が量産に向いている要因と言えます。
射出成形で発生する代表的な「成形不良」
とてもメジャーで多くのメリットを有する射出成形ですが、反対にさまざまな『成形不良』が付いて回るのも事実です。つまり製品の外観上または性能の面からも、不良や不具合の発生が起きてしまうのです。
成形不良の発生は、成形品の廃棄はもちろん、再び良品を作るための材料・人員・時間といった多くの無駄にもつながるため、極力発生させない進め方をしなくてはいけません。
ここでは、射出成形で発生する代表的な成形不良の原因と対策をご紹介いたします。
成形不良①:バリ
射出成形における「バリ」とは、金型の合わせ面(PL)の隙間や突き出しピンなどの隙間から樹脂が溢れる現象です。簡単に言うと、正しい製品形状からプラスチックが無駄にはみ出した状態のことを言います。
製品の形状に意図しない突起が生じるため、特に外観製品においては品質を大きく損ねますので、しっかりと対策を講じましょう。
なお、バリに関しての発生原因やその対策方法は、下記リンク先ページにて事例と共に詳しく紹介しています。ぜひご覧ください。
> プラスチック成形品に発生した不具合『バリ』の対策方法【射出成形の不良対策事例 #2】
成形不良②:シルバーストリーク
シルバーストリーク(silver streak、銀条)とは、射出成形時、樹脂の中で発生したガス(空気)が金型内で引き伸ばされ、その筋状になった『流動痕』が樹脂の表面に銀色の筋となって現れてしまう現象を言います。成形品の表面に現れてしまうため外観不良となり、正しい対策が必要となります。
シルバーストリークに関しての発生原因やその対策方法は、下記リンク先ページにて事例と共に詳しく紹介しています。ぜひご覧ください。
> 射出成形における不具合『シルバーストリーク』の発生原因と対策方法【射出成形の不良対策事例 #3】
成形不良③:ウェルドライン
ウェルドラインとは、成形材料の樹脂が金型内を分岐したのち再び合流するとき、樹脂温度が低下して樹脂同士が完全に融合せず、融着不良となってしまう成形不良です。金型に接した樹脂は急速に冷却され固化するため、合流ポイントにてV字型の溝ができやすいのが特徴です。
成形不良④:ボイド
一般的にボイド(気泡)は成形品の内部に空気の泡が発生する現象です。レンズやプリズムのような透明な成形品では、外観不良や光学特性不良になってしまいます。
また機構部品・機能部品では、強度の低下や破壊の原因になったりします。
ボイドに関しての発生原因やその対策方法は、下記リンク先ページにて事例と共に詳しく紹介しています。ぜひご覧ください。
> 射出成形における不具合『ボイド』の発生原因と対策方法【射出成形の不良対策事例 #5】
成形不良⑤:反り
反りとは一般的に、冷却された樹脂製品が金型から取り出した直後に変形を起こしてしまう現象です。
この反りが発生するメカニズムには主に
1. 形状が原因となる『成形収縮』
2.成形条件の樹脂温度・金型温度・射出圧力などが原因となる『残留応力』
3.成形品離型時の突き出しピンの位置・本数・状態・タイミングなどが原因となる『外部応力』
などあります。
なお、反りに関しての発生原因やその対策方法は、下記リンク先ページにて事例と共に詳しく紹介しています。ぜひご覧ください。
> 射出成形における不具合『反り』の発生原因と対策方法【射出成形の不良対策事例 #6】
成形不良⑥:ヒケ
ヒケとは、成形品の表面が凹んでしまう現象です。
射出成形では、熱して溶かした樹脂を金型に射出し、型内で冷やし固めることで成形します。この際、熱で膨張した樹脂が冷えると型内で収縮しますが、厚みの異なる箇所では、収縮率の差が原因でヒケが発生します。
3種類のヒケ原因の検証方法
検証①:射出圧力や保圧を上げる
検証②:ゲート点数の変更
検証③:材料の変更
それ以外にもヒケはリブ付近で発生しやすく、主にリブ部分とその他の部分の板厚に差があり、その差がそのまま収縮率の差を生んでしまい、ヒケを発生させてしまいます。
ヒケに関してより詳しい情報は下記の関連記事に掲載していますので参考にしてください。
[関連記事]
> プラスチック成形品の意匠面に発生したヒケの対策方法【射出成形の不良対策事例 #1】
またヒケは、数ある成形不良の中でも特に発生事例が多いため、弊社(株)関東製作所もその経験から得た知見を、専用の資料にまとめたり動画で紹介などしております。
ご興味があれば、ぜひこちらの関連記事よりご覧ください。
> ヒケの発生する原因とその対策方法とは?プラスチックの成形不良を専門家が詳しく解説
成形不良⑦:キャビとられ
金型の動きとしては本来、成形品が金型のコア側に張り付いた状態でコアが稼働し開きます。その後、コア側のエジェクターピンが押し出されることで、成形品を取り出すことができます。
『キャビとられ』とはすなわち、ある原因で金型のキャビティ―側に成形品が固定されてしまい、成形品が取り出せない不具合のことを言います。
キャビとられは特に、前述でも触れた「抜き勾配」と密接に関係してきますので、製品設計や金型設計での対応が大きなポイントとなるでしょう。詳細はぜひ下記関連記事で、弊社の事例紹介と共にご覧いただければ幸いです。
> 射出成形における不具合『キャビとられ』の発生原因と対策方法【射出成形の不良対策事例 #7】
以上ご紹介した7つの成形不良以外にも、射出成形にはさまざまな『成形不良』が伴います。射出成形には高い品質を求められるが故に、些細な不良箇所も見過ごせません。
金型を製作し成形後に成形不良が生じると、金型の改修・設変が余儀なくされ、納期遅れ・コストの加算にも大きく影響します。極力成形不良をおさえ、高精度なプラスチック製品を作るためにも、発生原因とその対策を良く熟知した上で、プロジェクトを進めたいものです。
また、以下リンク先の『射出成形ラボ』サイトでは、射出成形において発生してしまう各成形不良の原因と対策を一覧でまとめております。ぜひそちらも併せてご覧いただければ幸いです。
> 『射出成形ラボ』サイトで、各成形不良の原因と対策の一覧を見る
成形不良を事前に回避!「流動解析」で樹脂の流れをシミュレーション
前項でもご説明した通り、射出成形には非常にやっかいな『成形不良』が付き物ではあります。しかし金型製作に入る前の段階で、成形不良などの不具合を予測できる方法があります。それが『流動解析』です。
流動解析とは?
流動解析とは、CAE解析(※)ソフトウェアのうちの一つとされており、このソフトを使えば、実際に樹脂を金型に流す前にPC上で金型内の樹脂の流れをシュミレーションすることができます。
- CAE解析
- 「Computer Aided Engineering」の略。設計におけるシミュレーション解析の総称を意味しています。細かく分類すると流体解析や熱解析、応力解析、構造解析などがあり、設計段階において目で見えない部分を解析する事で、知識や経験だけに頼らない設計を可能とします。
前項で紹介した成形不良の多くは、金型内での樹脂の流れを把握できていれば回避できるものも多くあるでしょう。
例えば金型内で、製品形状部の両端から流れ入ってきた樹脂同士がぶつかる境目の位置を、シミュレーションで把握できます。つまり、ウェルドラインの不良が起きやすい位置を特定できるわけです。
また樹脂は、金型内で発生したガスや元々あった空気を押し込みながら流れる為、末端まで樹脂が到達した際に金型外への逃げ場がないと、ガスパックやエアトラップと呼ばれる箇所が発生します。すなわち、流動解析を用いればそれらの位置を特定でき、ボイドやシルバーストリークなどの事前対策が可能になるのです。
流動解析を活用し金型改修を最小限に
流動解析を活用し、成形不良が発生しそうな位置を特定できるということは、前もって金型内に不具合を回避するための機構を組み込んでおくことが出来るということです。
不具合の原因になるガスを逃がすための『割りコマ』を配置することで、溜まったガスを抜くための隙間を最適な位置に設けたり、樹脂同士がぶつかる位置を調整するため、ゲートの位置を事前に検討出来たりします。
つまり流動解析でシミュレーションしたうえで金型設計することで、成形後の金型改修という無駄を極力減らすことに繋がります。結果、製品開発プロジェクト全体で、時間やコストの削減に大きく寄与できるでしょう。
[関連記事]
> CAE解析における流動解析とは?プラスチック製品開発現場での有用性を詳しく学ぶ
射出成形を行う上で最も効率の良い環境とは?
今までご説明してきたとおり、射出成形とは非常に量産性が高く、思い通りの形状を精度高く生み出せる、とてもメジャーな成形工法です。その分、プロジェクト全体を通して予算も高額になり、製品を流通させるまでには長い時間がかかるものです。
だからこそ、金型メーカー・成形メーカーを選定する前に、そのメーカーがいかに効率の良いプロジェクトを共に伴走してくれるかがとても重要でしょう。
ここでは、製品開発プロジェクトを進めるうえで特に着目したい『設備環境』についてご紹介します。
同じ工場に射出成形機と金型製造現場がある優位性
射出成形の量産において、金型メーカーと成形メーカーは別々で運用されている場合が多いのではないでしょうか。当然各々のメーカーにとっては責任区分が自社の専門範囲に限定されるので、メリットはあるでしょう。しかしクライアントである製品メーカー様側の立場ではどうでしょうか。
下図にあるように、プロジェクトがスタートして金型が製作された後や、成形途中で不具合が発生し金型を改修する場合などに、都度『金型を輸送する』という工程が生まれてしまいます。
一般的なトライの工程
金型メーカーと成形メーカーが別々の場合、金型輸送に伴う時間的ロスが発生してしまいます。
関東製作所でのトライの工程
では、もし成形現場と金型製造現場が同じ工場内にあったとしたらどうでしょうか。
当然、金型を作った後はすぐ隣に配備された成形機に乗せるだけですし、金型改修が発生しても成形機からその場で下ろし、横で直してまた載せる。そんなことが可能になります。
そう、同じ工場に射出成形機と金型製造現場があることで、大幅な納期短縮の可能性が生まれ、プロジェクトにとって大きなメリットになるでしょう。
【射出成形ラボの簡易金型サービスはこちらより】
> 最短納期を2週間で!180ton射出成形機用の簡易金型を、60万からご提供いたします。
弊社(株)関東製作所の東海地区と九州地区にある成形工場には、金型現場が併設されております。長年パートナーとして協業させて頂いてますキョーラク株式会社様との対談でも、その有効性を取り上げさせていただいています。
詳しくは下記リンクより、弊社コーポレートサイトの特集ページをご覧ください。
> (株)関東製作所公式サイトの「未来を臨むパートナーストーリー – 協業で築いた射出事業の生産力 -」ページはこちら
後加工や組付けを担う「自動機」を併せて考える
射出成形で作る製品の中でも、ワンショットで完成しないものもあります。例えば自動車のウォッシャータンクなどの中空部品は、表側と裏側の樹脂パーツを成形し、その後パーツ同士をくっつける『自動溶着機』のような機械が必要になります。
弊社(株)関東製作所には、プラスチック成形品の『後加工専用機』の製作部門があるため、そういった自動で稼働する溶着機も抱き合わせで製作が可能です。
[関連記事]
> プラスチックの接合方法『溶着』を学ぶ。自動化・省人化を見据えたそのメリットと種類とは?
金型から後加工用の自動機まで一社内で製作できるということは、量産工場においてライン単位での設計提案が可能となります。
工程①:弊社製作の『金型』で射出成形を行う
工程②:成形された製品を、弊社製作の『自動熱溶着機』にセットし溶着する
工程③:出来た製品を弊社製作の『自動検圧機』にセットし検査する
つまり、金型での成形品の生産から良品の保証まで一気通貫で完結。この一連の生産ラインを、弊社だけでプロデュースできるのです。
ライン単位で設計できるということは、
機能的な仕様① | 成形後、スムーズに溶着機にセットできるよう、成形品の取出しの向きを考慮して金型内での製品レイアウトを決められる |
---|---|
機能的な仕様② | 溶着機に製品を固定するため、金型内に固定用のリブを前もって設計しておける |
など、金型製作単体で進めた場合では決して気付かない『機能的な仕様』を金型に織り込むことが出来るのです。
このように、金型設計から成形、後加工、そして品質保証まで社内一貫で提供できることは、お客様にコスト面や納期スケジュールで大きく貢献できます。ぜひ、製造メーカーを選定する際の参考にしていただければと思います。
まとめ
超大量生産ができ、さまざまな樹脂に対応可能。そして複雑な形状も精度良く再現できてしまう大変優れた成形工法。
そんな魅力ばかりが際立つ射出成形ではありますが、その分、思い通りの製品を効率よく生み出すには、整った設備や経験から培った技術的な知見が伴ったうえで、初めて実現させることができるでしょう。
弊社(株)関東製作所は会社設立当初より、長い間プラスチック業界に従事して参りました。その歴史の中で、幅広い事業展開に挑戦し続け、今ではプラスチック製品開発における全ての工法に精通できております。
プラスチック製品はコスト面でも成形面でも自由度が高いからこそ、各種加工技術の知見やノウハウが製品の出来を左右します。
そのため失敗を回避するためにも、まずは高い知見や技術を有するメーカーに相談し、適切な方法でプラスチック製品を製造することが大切です。用途や形状、生産数、樹脂の種類などによって最適な製造方法が異なるため、分からないことやお困り事があれば、ぜひ弊社(株)関東製作所へご相談ください。
> 射出成形ラボサイトで射出成形を基礎からを学ぶ
射出成形とは、複雑な形状・流麗な意匠面の再現性が高く、大量生産を得意とする、最もメジャーなプラスチック成形工法です。