【ブロー成形から射出成形への工法転換】 キーポイントは初期段階の設計工程 -フロントローディング-
射出成形
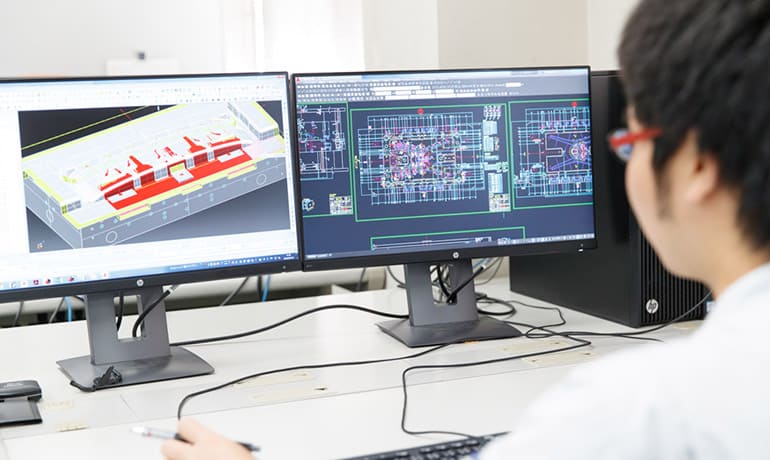
今回ご紹介するのは、ブロー成形から射出成形に工法転換するため、弊社が開発・設計をお手伝させて頂き、試作品~量産部品まで納入させて頂いた、「デフロスターノズル」という自動車部品の開発エピソードをご紹介いたします。
[射出成形ラボサイトでの事例紹介ページ]
> ブロー成形から射出成形に工法転換した製品事例
目次
「デフロスターノズル」ってどんな製品?
「デフロスターノズル」、または「ノズルデフロスター」と呼ばれるこの製品は、自動車のダッシュボード上でチラっと見える、フロントガラスの曇り止めのために設置されたエアコンの吹き出し口の部品です。
カーエアコンは運転席、助手席、後部座席はもちろんのこと、人気の1BOX車なら3rdシートまで吹き出し口が配置されています。これらは外から取り入れた空気を、カーエアコンユニットで加熱または冷却し、ダッシュボードや天井の中にかいくぐるように配置されたダクトを通して、温冷の風を吹き出し口まで運んでいます。
デフロスターノズルは、そのダクト部品の1種です。
乗車位置からは吹き出し口しか見えませんが、その下もカーブを描きながら製品が伸びており、カーエアコンユニットまでの空気の流路を形成しています。
自動車部品開発の順序とデフロスターノズルの特性
自動車は数多くの部品を使用しており、それら部品の開発は当然ながら順番や開発期間に差があります。
プラットフォームやエンジン、最近で言えばEVシステムや水素タンクなど、多車種に共通し、車の性能・安全を決するものは、数多くの実験を繰り返しながらじっくりと開発をしていきます。
その一方、車種ごとにデザインの異なるボディー、バンパー、インパネなどの部品は、短納期で開発されます。デザイントレンドは徐々に変わっていくものですから、即効性が求められるわけです。
そんな新車種ごとに開発されるデザイン部品群の中にも、製造工期を考慮して設計する順番が決まっています。一般的にはプレスボディー部品が先行し、次に内外装の樹脂部品を、大物からスタートして小物までといった形で進めていきます。
一般的に自動車の製造工期において、デフロスターノズル製造の順番は?
最後の最後です(笑)
ボディー形状、エアコンユニット位置が決まり、デザインされたインパネがフィットするよう設計され、それらの部品間の隙間をかいくぐって配置されるのが、ダクト類、デフロスターノズルだからです。
自動車部品に“主”と“従”があるとしたら、思いっきり“従”のグループですね。
ですので開発検討の際には、“主”部品達の変更で、おもいっきり形状が変更し、検討していた事項がすべて水の泡なんてものよくある事です。
そんなデフロスターノズルですから、この製品の金型製造と射出成形の特性を一言で表現するなら、
「金型の成立性や成形の困難性を全く考慮されずに設計が進む」
でしょう。
検討用データを頂くと、かなりの確率でパーティングラインが成立しておりません。また大型車では金型上の深さ方向が深く、型製作時には大型のマシニングが必要になります。
更に吹き出し口部は射出成形の最終充填部位となり、非常にガスを巻き込みやすく対策が必要です。製品の用途や可視範囲のわりに、設計段階が厄介で、手間がかかる部品なんです。
【射出成形ラボの簡易金型サービスはこちらより】
> 最短納期を2週間で!180ton射出成形機用の簡易金型を、60万からご提供いたします。
デフロスターノズルをブロー成形から射出成形へ
今回のお客様は、(日本を代表するカーメーカーでありながら)、デフロスターノズルはブロー成形でしか製造した実績がなく、次の車種では射出成形化したいというご要望でした。当時、他カーメーカーはほとんどが射出に切り替わっていましたので、そういう意味では後発組になります。
工法転換の背景
「曇り対策」は、安全性の面からも非常に重要ですが、消費者目線でも、エアコンをMAXに設定したのに、中々曇りが取れなかったり一部に曇りが残ったりすると、イライラしちゃいますよね?
CADの発達によって自動車のデザインが曲面化した結果、単純にフロントガラスに風を当てれば曇りが取れるわけではなくなりました。曇り対策のためには、ガラスの角度・幅などを考慮して、風の向き、広がり具合を調整する必要が出てきたわけです。
デフロスターノズルには、風向リブという風向きを調整する“壁”が流路に設けれらており、その壁が調整の役割を果たします。このリブに自由度を持たせ、「ちゃんと曇りが取れるフロントエアコン」を実現しようとすると、ブロー成形では“限界”があるのです。
少し難しい話になりますが、風向リブは吹き出し口の少し手前で設置が止まっています。このちょっと控えたリブ位置が、流体力学的に出口で風が上手に拡散する役割を果たし、ガラスの一部に曇りが残ったりすることを防ぎます。
ブロー成形でもリブは設置できますが、この「ちょっと控えた」がブローの金型構造的にできないんです。
射出成形も万能ではなくデメリットもあります。
ブロー成形では1部品で作成可能なものが、射出成形では2部品構成となります。よって成形品のアッセンブリーの工数が増えます。
また2部品構成となることで金型を2型製造するか、2部品セット取りの大型化する必要があります。すなわち型コストは必然と高くなります。
しかし、カーメーカーは最適な風向リブを設定するため、ブロー成形から射出成形への工法転換が必要だったわけです。現在ではお客様の満足度と安全性の面からデフロスターノズルは射出成形が一般的となっています。
プロジェクトの概要
全体のプロジェクトの概要と担当は次の通りです。
試作フェーズ
工程と内容 | 担当 |
---|---|
① ブロー成形でデフロスターノズルの製品設計をする | お客様 |
② その設計データを、射出成形へ再設計する | 当社 |
③ 試作金型の作成と射出成形品の納入 | 当社 |
④ 車両試作イベント | お客様 |
量産フェーズ
工程と内容 | 担当 |
---|---|
⑤ 試作イベントの結果を反映し、ブロー成形でデフロスターノズルの設計修正をする | お客様 |
⑥ その修正データを、射出成形へ再設計する | 当社 |
⑦ 量産金型の作成と射出成形品の納入 | 当社 |
見ていただくとわかりますが、お客様は従来通りの仕事をすれば、勝手に製品は射出成形に置き換わる。
当社の実績を信頼頂いた故ではありますが、すばらしいプロジェクト計画です。(笑)
工法転換プロジェクト最大のポイント -3種類の設計-
このプロジェクトの大きなポイントは「日程」でした。ブロー成形→射出成形という工法転換プロジェクトなのに、開発日程は従来のブロー製品製造を基準に設定されていました。
例えば試作品の場合、ブロー製品の設計完了から射出試作品納入まで3週間。前述の通り、デフロスターノズルは最後の最後に設計される部品ですから、この部品の遅れ=全体工程の遅れにつながり、後ろの余裕もありません。
② ⑥ の金型製造工程にも、最初に“金型の設計”があります。
ですので、このプロジェクトは金型を削りだす前に、3種類の設計があることになります。全ての設計工程が完了すれば、あとはいつも通りに型製造をするだけなので、「3種類の設計」が工法転換、日程遵守の重要工程となります。
ブロー成形を射出成形へ再設計 - 再設計ポイント4項目 –
ここでは実際にブロー成形を射出成形に再設計する際にどんなことをするか?
すなわち、ブロー成形品と射出成形品では、“風向リブ”以外にどんな違いがあるのか?という視点で説明していきます。
↑ブロー設計の状態
↑射出化設計の状態
まず、お客様が設計する際に“これだけは“とお願いしたのは製品の“厚み”です。
ブロー成形と射出成形では製品の板厚が異なります。一般的に射出成形の方が薄いです。射出化への再設計時に板厚から修正するととても大変ですので、ブロー成形での設計時に板厚だけは、射出の板厚で設計をしてもらいました。
それ以外の再設計は大きくわけて次の4項目になります。
- ブロー品では一体で設計されている部品を、FR・RRの2部品に分割する
- 分割した際に、射出金型のP.L.が成立するようにする
- アッシーのために片側に爪を、反対側に穴をバランスよく設ける
- また風が外周から漏れないようにフランジを設ける
ブロー成形のメリットは“袋”形状ですから、1部品構成で出来ます。しかし射出成形で空気が通る流路を作成するには2部品構成とし、アッセンブリーする必要があります。分割は、左右=ドライバー側・パッセンジャー側に分けるのではなく、車両の前後=FR・RRで分割します。
その最初のFR・RRの分割は、どこでもいいから分割するのではなく、P.L.を考慮しながら分割していきます。それも前述のようにデフロスターノズルは他の“主”部品の間をかいくぐって設定されていますから、分割ラインもS字カーブのようにウネウネします。
次にFR・RRの組付け性が良いように、また外れないようにバランスよく爪を設定し、外周をキープしながらフランジを設けていきます。
3種類の設計を同時進行 - コンカレントエンジニアリング的思考 –
では重要工程である『ブロー製品設計』、『射出製品設計』、『金型設計』の3種類の設計をどのように動かしたのか?
実際の工程を試作フェーズ、量産フェーズに分けて見てみましょう。
試作フェーズ:ブロー製品設計完了後、3週間で試作品納入
量産フェーズ:ブロー製品設計完了後、10週間でファーストトライ品納入
見て頂くとわかりますが、私達は3種類の設計をパラレルで動かしました。コンカレントエンジニアリングに近い形ですね。
設計工程は単純にCADを使って絵を描いたら終わりではありません。
『ブロー側』は車両設計の立場で、逆の『射出/金型側』は金型と成形品の成立のために、形状変更修正を設計が進むにつれ幾度とします。その際に前後の設計工程と形状変更依頼のやりとりを幾度となく実施します。
「インパネとデフロスターの隙間が0.5㎜しかないから位置を変更したい」とか、「金型のPLが成立しないからここのR形状を大きくしたい」などといった感じです。
これらのやりとりを、各工程が完了してから次工程が動きだしたのでは、そもそも日程が間に合いませんし、前工程でのやり直しロスが発生いたします。ですので、日程短縮のためにパラレルで動しつつ、特に今回のプロジェクトでは、お客様が射出成形に詳しくないため、いつも以上に綿密に連絡を取り合いました。
問題なく納品へ! ポイントはフロントローディング
作るもの=3Dデータさえできてしまえば、あとはいつもの型作りですから、最初に設計工程を重要工程と位置づけし、お客様と綿密なやりとりを実施することで、私達は試作、量産の両フェーズとも問題なくスムーズに射出成形品の納入まで実施いたしました。
また試作、量産の両フェーズを請け負っていることをメリットに、試作型での作成時の改善事項や、VE提案を量産フェーズへと反映しました。
単なる工程の前倒しではなく、モノづくりプロセスの上流プロセス部分=設計に、実施すべきことを埋め込んで全体最適を目指す。いわゆる“フロントローディング”です。
【射出成形ラボの簡易金型サービスはこちらより】
> 最短納期を2週間で!180ton射出成形機用の簡易金型を、60万からご提供いたします。
『新たなモノづくり』で一番重要なのは設計
新しいモノづくりにチャレンジする場合、製品設計者は製品性能の検証を確実にし、使用する現場の意見など取り入れ、従来よりも高性能/高品質/安価などのテーマに沿った設計をするでしょう。
しかしながら、その設計工程で「金型のこと」「成形のこと」はあまり考慮されず進むことが多々あります。それどころか、近年3Dプリンターが安価になり普及した影響で、そういった事例は増える傾向です。
樹脂製品を簡単に作ることができる3Dプリンターは、「金型」「成形」を無視した状態でもモノが出来てしまいます。
3Dプリンターで幾度も試験をこなした後に、「企画数量が多いので、こんな製品を射出成形で作りたいんですけど」とご相談を頂いても、射出成形で実装するには、製品形状に対しかなりの修正が必要で、実施した試験も1からやり直ししなければいけないケースもあります。
お客様の立場から言えば、「3Dデータを元に相見積を実施し、最安値のメーカーに金型と製品を発注する」と言うのが、通常のルーティーンでしょう。
ですが、工法転換へのチャレンジする場合や、そもそも射出成形の知見が乏しい場合は、早めに総合的に支援をしてくれるメーカーとタッグを組むべきです。結果その方が全体の日程、コストを抑えることが来ます。
そしてそのキーポイントは、今回の事例でご紹介したように初期段階の設計工程です。そう、フロントローディングなのです。
関東グループでは、長年のモノづくり経験に加えてCAE解析への対応や、3Dプリンターを使った相互での形状確認、試作及び量産共対応など、幅広い分野をサポートし、プラスチック製品開発のベストパートナーを目指しております。
ぜひ、開発当初からデザインーインすることで、お客様が作りたい、欲しい製品開発をお手伝いさせてください。
射出成形ソリューションサイト
> 小ロット・試作金型製作・コストダウン提案の【射出成形ラボ】サイト