射出成形機を詳しく解説 成形の流れから構造、選定ポイントから射出成形品の製作事例まで紹介
射出成形
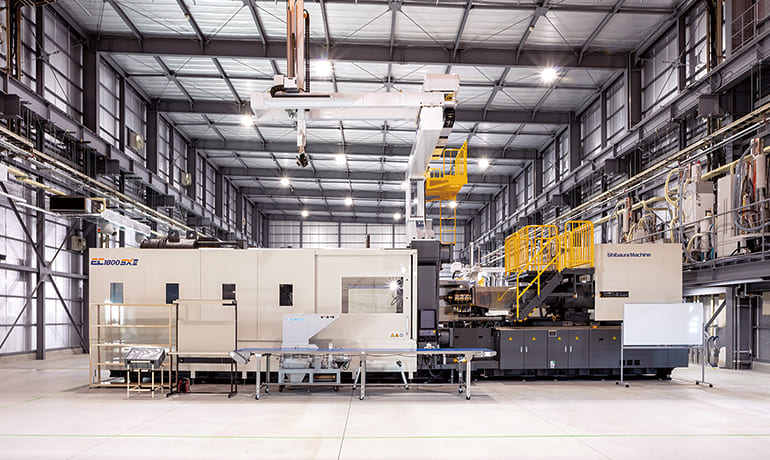
プラスチック製品を作るために欠かせない装置、それは射出成形機です。
射出成形機は様々なサイズ・重量のプラスチック製品を効率的に生産することが可能であり、現代のモノづくり業界において非常に重要な役割を果たしています。
今回は射出成形機の構造や種類、選定方法について解説します。また当社、関東製作所グループで保有している180t~1,800tクラスの成形機を例に、対応サイズ・重量を参考にご紹介します。
目次
射出成形機の基本を知る
そもそもプラスチック製品とは、素材となる「樹脂」、製品を形作る「金型」、そして素材から製品を成形して生み出す装置「成形機」の3つの要素によって作られています。
成形方法としてはブロー成形、真空成形など様々な工法があり、中でも代表的な成形方法が「射出成形」です。この工法により製品を作り出す装置が今回ご紹介する「射出成形機」なのです。
[関連記事]
> 射出成形の基礎、コストや納期対策への専門知識を学ぶ
- 射出成形とは
- 材料を加熱し溶融させた後、成形品の形状に射出する工法です。
射出成形は金型の転写性が非常に高いため、複雑な形状のプラスチック製品の製造に適しています。また1つの金型で100万個以上ものプラスチック製品が成形可能で、1サイクル40秒~50秒程度です。閉じた金型に液体樹脂を流し込むため無駄が少なく、後加工も不要です。
こちらの記事は動画でもご覧いただけます。
射出成形機は自動車部品や家電製品、医療機器など多くの製品の製造に使われており、様々な産業分野で広く利用されています。射出成形機は身近な物からあらゆる物までを作り出し世界中で活躍しています。
【射出成形ラボの簡易金型サービスはこちらより】
> 最短納期を2週間で!180ton射出成形機用の簡易金型を、60万からご提供いたします。
射出成形機での成形の流れを学ぶ
射出成形機によってどのようにプラスチック製品が作られるのでしょうか?
ここでは射出成形機の全体の流れを見ていきましょう。基本的には大きく分けて【溶融】【充填】【固化】という3つの工程があります。
溶融(ようゆう)
まずは材料の準備です。材料とはペレットと呼ばれる粒状の樹脂やマスターバッチと呼ばれる着色剤のことです。これらをホッパー部分に入れるとシリンダーに入ります。
次に材料はシリンダー内でヒーターによって加熱され溶融し、その後シリンダー先端に溜まります。この時、温度が低すぎると材料が十分に溶けず、温度が高すぎると材料が劣化する可能性があるため、適切な温度調節が要求されます。
充填(じゅうてん)
まず取り付けた金型を閉じ、締め付けます。樹脂を射出する際に高い圧力が金型にかかる為、金型が開かないよう強い締め付けが必要になります。
そしてシリンダーの先端のノズルを金型に押し付け、圧力をかけながら溶融した材料を金型内に射出します。
固化(こか)
金型を冷却することで成形品を冷やし固めます。成形品が固化したら金型を開き、成形品を取り出します。
このような流れでプラスチック製品は成形されます。
以下の動画では射出成形の流れをよりわかりやすく解説しておりますので是非ご覧ください。
射出成形機の構造を学ぶ
射出成形機は、大きく分けて射出ユニット、型締ユニット、コントローラーの3つから構成されています。以下ではそれぞれの役割や内部構成について解説します。
射出ユニット
射出ユニットは材料を溶かし、金型に高圧で流し込む役割を担っています。内部はホッパー、シリンダー、ノズルによって構成されています。ホッパーから入れられた材料はヒーターによって加熱されたシリンダーで溶け、ノズルから射出されます。
このような役割を担う射出ユニットには構造上、いくつかの種類が存在します。
プランジャー式
シリンダー内の材料をプランジャーで押し出すことで射出する方式です。(プランジャーとはピストン棒という意味で、前後に往復運動をする装置です。)
プランジャーが後退するとシリンダー内に材料が流れ込みます。プランジャーが前進しシリンダー内の材料を押し出します。すると圧力がかかり射出されるという構造です。
プリプラ式
材料を溶融するためのシリンダーと射出するためのシリンダーの2本を使用し射出する方式です。溶融用加熱シリンダーで材料を溶かし、射出用加熱シリンダーに送り込み、プランジャーで押し出すことにより射出されるという構造です。
スクリュー式
スクリューの回転によって射出する方式です。これは現代における最も代表的な構造です。
シリンダー内に材料が落ち、スクリューが回転することで先端に向かって材料が運ばれます。その過程でヒーターによって材料は溶け、シリンダーの先端に溜まります。スクリューを前方に押し込むことにより射出されるという構造です。
スクリュー式では1本のスクリューで溶融、混練、計量、射出の工程を完結することができます。また、スクリューによる回転や混練作用により材料が均一に溶けることで、製品の品質が確保できるというメリットがあります。
関東製作所では、この「スクリュー式」の射出成形機を多く保有しています。
また射出成形機によってはスクリューが耐摩耗仕様のものもあり、これによりガラス入りのエンプラなどの様々な材料に対応できます。
型締ユニット
型締ユニットは金型を取り付ける部分で、金型の締め付けや開閉する役割を担っています。また成形品の冷却も行います。
内部は型締シリンダー、固定側ダイプレートと可動側ダイプレートによって構成されています。固定側ダイプレートと可動側ダイプレートの間に金型を取り付け、開閉することで材料を充填したり、成形品を取り出したりします。
型締ユニットは射出の際に高い圧力がかかるため、金型が開かないように締め付けが必要になります。金型の締め付けが弱いと金型が開き、そこへ射出した樹脂が流れ出てしまいます。この際にできる不良を「バリ」といいます。関東製作所では、「バリ」の対策方法に関する記事も掲載しています。
[関連記事]
> プラスチック成形品に発生した不具合『バリ』の対策方法【射出成形の不良対策事例 #2】
このような不良を防ぐためにも強い締め付けが必要なのです。金型の締め方の動作方式としては、直圧式とトグル式の2つがあります。
直圧式
油圧シリンダーによって型締力を発生させるものです。油圧シリンダーの前進後退で金型の開閉動作を行います。
直圧式では高い圧力を直接受けるため大きな油圧力を必要とします。型締め位置の調整は油圧シリンダーを移動させることで比較的簡単にできるのがメリットです。
トグル式
トグルリンクと呼ばれるアームを使用して型締力を発生させるものです。型締力はサーボモーターで設定し生成するため、油圧を必要とせず強い型締力が出せます。
トグル式ではアーム機能により型開閉時の速度が速くなり、サイクルタイムが短縮できます。さらに型締時は高い圧力をかけることが可能になるなど、効率良く速度や圧力を変換できることがトグル式のメリットです。また型締めを行った際にロックがかかるため、型が開いてしまうこともありません。
コントローラー
コントローラーは射出成形機の制御部です。
射出の速度やシリンダー温度、圧力、金型の温度、樹脂の射出量などの、成形条件を制御するための装置になります。射出成形機に内蔵されているものもあれば、外付けのコントローラーもあります。
射出成形機の種類を知る
射出成形機の射出や型締に必要な動力源として代表的なものが電動式と油圧式の2つあります。以下では両者を比較し、それぞれのメリットとデメリットを解説します。
電動式射出成形機
電動式はサーボモーターを用いて、速度・圧力・位置などの動作をすべて制御する仕組みです。電動式ではトグル式と直圧式の型締めに対応していますが、ほとんどトグル式が採用されています。
電動式のメリット
電動式ではサーボモーターにより射出装置の制御が正確にできるため、成形品の寸法や形状を一定に保つことが可能になり、製品の成形精度が高くなります。これにより油圧式ではできなかった高い精度が必要な作業が可能になります。
必要な時に必要なだけモーターを駆動させるため、油圧式と比較して40%~50%省エネです。これにより電気使用料金が安くなる効果があります。そして油圧式と比較して低騒音です。
また4つ以上の独立したモーターにより成形工程を並列進行させることができるため、成形サイクルの短縮ができ、生産性が上がります。電動式では油不使用、冷却水を大幅に削減など、環境への影響が低減されます。また衛生面でクリーンなため食品容器や医療関係品に最適です。
電動式のデメリット
サーボは設定されたことに忠実かつ素早く応答する動きができる制御機構のため、無理がききません。また成形機の価格が油圧式と比較して高いです。さらには条件設定が難しいというデメリットもあります。
油圧式射出成形機
油圧式は油を閉じ込めて、その圧力を離れた場所に伝えることで大きな力を出す仕組みです。これには「パスカルの定理」が応用されており、古くから利用されている動力源です。油圧式では直圧式の型締めのみ対応しています。
油圧式のメリット
油圧式は油を使用しており、油は圧縮性が少ないという特性があるため高い圧力が生成可能です。
また電動式と比べて成形機の価格が安いです。油圧ならではの操作感覚があり微調整などが可能なため、電動式と比べて条件設定の幅が広いです。
油圧式のデメリット
電動式と比べて消費電力が大きく音も大きいため、特に夜間は騒音が気になってしまいます。また細かい制御が難しく、寸法が安定せずブレが生じるため再現性に乏しいです。
油は金属を脆くするため、作動油温度管理や品質管理が必要です。
また、油を使用するとオイル漏れのリスクもあり危険な面も考えられます。オイル漏れにより機械が止まり、生産性も下がるというリスクも大きなデメリットでしょう。
市場全体、また関東製作所でも『電動式』が主流?
現在の射出成形機は消費電力の削減や再現性が高いという面から、次第に油圧式から電動式へ移換しています。関東製作所で保有している射出成形機も電動式が多いです。
ですが油圧ならではの操作感覚が必要な場合もあり、油圧式での成形条件を電動式に移換することができない成形品もあります。そのため電動式と油圧式のどちらが適切な方式であるかは、射出成形の要件によって異なります。成形品の特性と照らし合わせて選択する必要があるでしょう。
射出成形機の選定方法(計算式あり)
射出成形機には様々な種類があるため、適切な射出成形機を選ぶ必要があります。
成形機サイズは製品のサイズ、射出容量、製品の深さによって決まります。まずは作りたい製品の形状、サイズ、材料、生産量などについて明確にしておきましょう。
射出成形機タイプの選択
上記で説明した通り、射出成形機にはそれぞれ構造に違いがあります。射出ユニットと型締ユニットで方式が異なりますし、動力源の違いもあります。それぞれの特徴を理解した上で射出成形機のタイプを選択しましょう。
必要型締力(ton数)の選択
また、製品サイズ・重量によっておおよその成形機サイズが分かります。成形機サイズはton数で表記されております。例えば「EC850SX-78A」という成形機は、850tまで対応が可能です。これは、成形メーカーの保有設備を見れば分かります。
このton数は何の力を表しているかというと、『金型を締める力』を表しています。
射出成形では材料を射出する際、金型に大きな圧力がかかります。一般的に指先ぐらいの面積に対して、乗用車1台分ぐらいの圧力がかかると言われております。この圧力によって金型が開かないよう、型を締め付けておく力のことを『必要型締力』といいます。
『必要型締力』が高いとガス逃げが悪くなり、低いとバリが発生します。そのため適切な型締力を算出する必要があります。
必要型締力の計算式
必要型締力は以下の計算式で求められます。
F=p×A/1000
F:必要型締力 / p:キャビティー内圧力 / A:投影面積の合計(㎠・平方センチメートル)
※pは樹脂材料によって変化します。
またそれ以外にも成形品の肉厚、キャビティーの表面温度、ランナーの取り方、成形条件などによって数値が変わるので注意が必要です。
例として『A4サイズのPPプラスチック製品を成形するのに必要な型締め力』を計算していきたいと思います。
p(キャビティ内圧)は素材によって変化するとありますが、PPの場合は300kgf/㎠になります。A4サイズの製品を作る場合、A(投影面積の合計)は、21×29.7cm=623㎠です。
これらを当てはめると
F=(300×623)/1000=186.9t となります。
成形条件合わせで余力を考慮すると、成形機サイズは200~220tを選択すればいいことが分かります。
このようにして、どのような射出成形機が必要なのかが決まります。
しかしこの辺の詳しい仕様に関しては、製品メーカー様だけでは判断できない領域かと思います。よく熟知した成形メーカーと密な打ち合わせが必要です。
関東製作所は「金型」と「成形」両方の事業を展開しているため、社内で一貫した対応が可能です。成形品の仕上がりをゴールとした金型提案もその場でできることが、弊社最大の強みです。
【射出成形ラボの簡易金型サービスはこちらより】
> 最短納期を2週間で!180ton射出成形機用の簡易金型を、60万からご提供いたします。
関東製作所保有の射出成形機と成形品の事例紹介
ここでは株式会社関東製作所が保有する射出成形機をトン数別に紹介します。また、各成形機の製品事例についても紹介します。
1,800tサイズの射出成形機
メーカー・機種名 | 芝浦機械/EC1800SXⅢ-155A |
---|---|
成形品サイズ | 720×720㎜、400×1,300㎜(PPコールドランナー) 850×850㎜、400×1,800㎜(PPホットランナー) |
製品重量 | ~4,650g(量産の場合)、~6,200g(トライアルの場合) |
材料 | 汎用PP・ABS・PC+ABS・PC、PA6+G30%など |
取出し機 | 3軸サーボ スクリュー耐摩耗仕様 |
保有工場 | 株式会社関東製作所 福岡工場 |
※トレーなどのプラスチック製品で例えると、A1サイズ程度まで対応可能です。但し、A1サイズ程のトレーを作る場合は、ホットランナー仕様となります。
- ホットランナー・コールドランナー
- そもそもランナーとは、1つの金型で製品を複数個取りする際に、全ての成形品に樹脂を流すための通路のことです。
- 通常、ランナー内の樹脂は金型と同時に冷やされ、成形品と一緒に取り出されます。このような仕組みのことをコールドランナーといいます。コールドランナーでは廃棄ランナーが出てしまいますが、ホットランナーとは違い金型に追加で設備を加える必要がないので、金型代は安価というメリットがあります。
- 対してホットランナーとはランナー内の樹脂を温め、冷やされ固化された成形品のみを取り出す仕組みです。廃棄ランナーが出ないというメリットがありますが、金型に特殊な設備を設けるため、金型代やメンテナンス費用が高くなります。ただ長期的に見れば無駄な樹脂を浪費しなくて済む点でコスト削減に繋げられるので、条件次第で適切なランナーのセレクトを心掛けましょう。
- 「成形品サイズ」の項目で、ホットランナーとコールドランナーで成形可能な製品サイズが異なっていたのはこの仕組みが要因です。ホットランナーを利用すると樹脂が固まるまでの時間が長くなります。つまり樹脂が流れる時間をコールドランナーと比べ長く稼げるので、その分大きな製品が作れるという原理です。
>射出成形ラボサイトで、関東製作所保有の1,800ton射出成形機の詳しい機能を知る。
デーライト延長200mm!特注の電動式1,800ton射出成形機で、深くて重い製品も成形可能!
1,300tサイズの射出成形機
メーカー・機種名 | 三菱重工業/1300mmⅢ |
---|---|
成形品サイズ | 620×620㎜・400×950㎜(PPコールドランナー) 720×720㎜・400×1,300㎜(PPホットランナー) |
製品重量 | ~2,700g(量産の場合)、~3,600g(トライアルの場合) |
材料 | 汎用PP、ABS、PC+ABS、PC(量産対応可能) |
取出し機 | なし |
保有工場 | 株式会社関東製作所 岐阜工場 |
※トレーなどのプラスチック製品で例えると、B2サイズ程度まで対応可能です。但し、B2サイズ程のトレーを作る場合は、ホットランナー仕様となります。
製品事例:自動車のグリルラジエーター
自動車のグリルラジエーターです。樹脂材質はABS。1mを超える大型製品であり、かつ意匠面に格子形状が敷きつめられたデザインのため、金型の切削加工に非常に時間を費やした事例です。
より詳しい製品事例の情報は、下記リンク先「射出成形ラボ」サイトにてご覧ください。
> 意匠面の加工精度を追求した大型製品 – 自動車用グリルラジエーター –
850tサイズの射出成形機
メーカー・機種名 | 芝浦機械/EC850SXⅢ-78A |
---|---|
成形品サイズ | 500×500㎜・300×800㎜(PPコールドランナー) 600×600㎜・300×1,150㎜(PPホットランナー) |
製品重量 | ~2,400g(量産の場合)、~3,100g(トライアルの場合) |
材料 | 汎用PP・ABS・PC+ABS・PC(量産対応可能) PA6+G30%(トライアル・小ロットは対応可能) |
取出し機 | 5軸サーボ対応 |
保有工場 | 株式会社関東製作所 浜松工場 |
メーカー・機種名 | 芝浦機械/EC850SXⅢ-78A |
---|---|
成形品サイズ | 500×500㎜・300×800㎜(PPコールドランナー) 600×600㎜・300×1,150㎜(PPホットランナー) |
製品重量 | ~2,400g(量産の場合)、~3,100g(トライアルの場合) |
材料 | 汎用PP・ABS・PC+ABS・PC、PA6+G30%など |
取出し機 | 3軸サーボ対応 スクリュー耐摩耗仕様 |
保有工場 | 株式会社関東製作所 福岡工場 |
※トレーなどのプラスチック製品で例えると、A2サイズ程度まで対応可能です。但し、A2サイズ程のトレーを作る場合は、ホットランナー仕様となります。
製品事例:自動車のサイドステップ
自動車のサイドステップです。樹脂材質はAES。長手方向に1,000mmあり、かつ樹脂厚が薄い製品ですが、多点ゲート・バブルゲートを採用することで反りを軽減できるように工夫をしています。
より詳しい製品事例の情報は、下記リンク先「射出成形ラボ」サイトにてご覧ください。
> 反り対策・成形機サイズダウン・日程短縮の提案 – 自動車用サイドステップ –
650tサイズの射出成形機
メーカー・機種名 | JSW日本製鋼所/J650EL3-3100H |
---|---|
成形品サイズ | 430×430㎜・300×620㎜(PPコールドランナー) 510×510㎜・300×820㎜(PPホットランナー) |
製品重量 | ~1,650g(量産の場合)、~2,200g(トライアルの場合) |
材料 | 汎用PP・ABS・PC+ABS・PC(量産対応可能) PA6+G30%(トライアル・小ロットは対応可能) |
取出し機 | なし |
保有工場 | 株式会社関東製作所 岐阜工場 |
※トレーなどのプラスチック製品で例えると、B3サイズ程度まで対応可能です。但し、B3サイズ程のトレーを作る場合は、ホットランナー仕様となります。
製品事例:自動車のガーニッシュ部品
自動車のガーニッシュ部品です。材質はAES。小ロット生産のため、広範囲のアンダーカットにスライドを使わず、フロート押出による手取りでの取出しを行った製品です。
より詳しい製品事例の情報は、下記リンク先「射出成形ラボ」サイトにてご覧ください。
> 金型のイニシャルコストを抑える小ロット対応 – 自動車用ガーニッシュ –
450tサイズの射出成形機
メーカー・機種名 | JSW日本製鋼所/J450ADS-1400H |
---|---|
成形品サイズ | 360×360㎜・200×650㎜(PPコールドランナー) 420×420㎜・200×950㎜(PPホットランナー) |
製品重量 | ~900g(量産の場合)、~1,200g(トライアルの場合) |
材料 | 汎用PP・ABS・PC+ABS・PC(量産対応可能) PA6+G30%(トライアル・小ロットは対応可能) |
取出し機 | 3軸サーボ対応 |
保有工場 | 株式会社関東製作所 浜松工場 |
メーカー・機種名 | 芝浦機械/EC450SXⅢ-36A |
---|---|
成形品サイズ | 500×500㎜・300×800㎜(PPコールドランナー) 600×600㎜・300×1,150㎜(PPホットランナー) |
製品重量 | ~1,000g(量産の場合)、~1,380g(トライアルの場合) |
材料 | 汎用PP・ABS・PC+ABS・PC、PA6+G30%など |
取出し機 | 5軸サーボ対応 スクリュー耐摩耗仕様 |
保有工場 | 株式会社関東製作所 福岡工場 |
※トレーなどのプラスチック製品で例えると、A4サイズ程度まで対応可能です。
製品事例:色差計の筐体部品
色差計の筐体部品です。樹脂材質はPP。7型で9部品を構成する仕様。各部品をアッセンブリしての製品のため、それぞれ非常に高いレベルの精度が要求された事例です。
より詳しい製品事例の情報は、下記リンク先「射出成形ラボ」サイトにてご覧ください。
> 成形品の仕上がりをゴールとした金型の仕様提案 – 色差計の筐体部品 –
180tサイズの射出成形機
メーカー・機種名 | JSW日本製鋼所/J180AD-300H |
---|---|
成形品サイズ | 230×230㎜・100×520㎜(PPコールドランナー) 270×270㎜・100×720㎜(PPホットランナー) |
製品重量 | ~163g(量産の場合)、~218g(トライアルの場合) |
材料 | 汎用PP・ABS・PC+ABS・PC(量産対応可能) PA6+G30%(トライアル・小ロットは対応可能) |
取出し機 | なし |
保有工場 | 株式会社関東製作所 岐阜工場 |
※トレーなどのプラスチック製品で例えると、A5サイズ程度まで対応可能です。
製品事例:自動車の給水口のインレット
自動車の給水口のインレットです。樹脂材質はPP。パイプ形状を両側スライドによる射出成形で構成した事例です。
より詳しい製品事例の情報は、下記リンク先「射出成形ラボ」サイトにてご覧ください。
> パイプ形状を両側スライドによる射出成形で構成 – 給水口のインレット –
以上、関東製作所グループ保有の射出成形機と事例を紹介しました。さらに国内外の協力メーカーを含めると、さらに多種多様なサイズ・材料の製品に対応できます。
【射出成形ラボの簡易金型サービスはこちらより】
> 最短納期を2週間で!180ton射出成形機用の簡易金型を、60万からご提供いたします。
まとめ
射出成形機は精度の高い製品を効率的に生産することが可能であり、現代のモノづくりにおいて非常に重要な役割を果たしています。今後も技術の進歩により素材のバリエーション増加や生産性や効率性の向上が期待されます。
関東製作所では180t~1,800tクラスの射出成形機を保有しており、多種多様なサイズ・材料の幅広い製品に対応いたします。
また金型から量産成形まで行っており、製品開発における全ての工程を社内で一貫対応いたします。特に浜松工場と福岡工場では金型製作と樹脂成形が隣接した現場で作業をしています。効率よく回せる環境が整っているため、金型輸送が必要なく大幅な納期短縮やコストダウンが可能です。
プラスチック製品で何かお困りのことがございましたら、お気軽にお問合せ下さい。