CAE解析における流動解析とは?プラスチック製品開発現場での有用性を詳しく学ぶ
射出成形
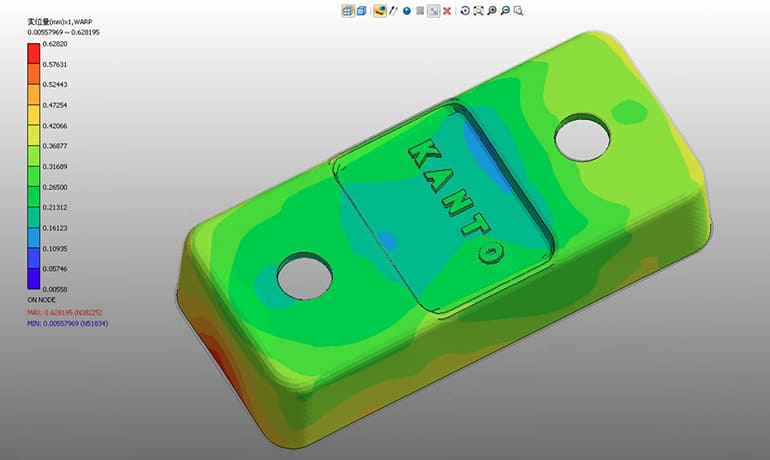
CAE解析とは、「Computer Aided Engineering」の略になります。設計におけるシミュレーション解析の総称を意味しています。
細かく分類すると流体解析や熱解析、応力解析、構造解析などがあります。設計段階において、目で見えない部分を解析する事で、知識や経験だけに頼らない設計をする事が可能です。
今回はCAE解析の中でも、射出成形の金型設計で使用する「流動解析」を解説致します。
目次
流動解析とは?そのメリットとは?
流動解析とは?
流動解析とは、金型内の樹脂の流れを見る為のCAE解析ソフトウェアの一つです。
射出成形の基本は「樹脂を溶融→金型内に溶融した樹脂を射出→冷やして固める」が大きな一連の流れです。射出成形において金型内にどのように樹脂を流すかは、非常に重要なポイントです。樹脂の流し方一つで、不良発生の原因にもなるからです。
しかし鉄の塊である金型の中を、樹脂がどのように流れるのか見る事は出来ません。ましてや設計段階では予測する事は出来ても細かく把握する事は出来ません。
そこで金型内の樹脂の流れを解析する為のソフトとして「流動解析」と言われるツールが使用されるのです。
【射出成形ラボの簡易金型サービスはこちらより】
> 最短納期を2週間で!180ton射出成形機用の簡易金型を、60万からご提供いたします。
こちらの記事は動画でもご覧いただけます
流動解析で出来る事①
流動解析という言葉通り、射出成形の金型内での樹脂の流れが把握できます。
例えば、図のような箱形状の製品で製品の両端から樹脂を流し込んだ場合、
両端から流れた樹脂同士がぶつかる箇所や、穴の部分を両側から回って樹脂がぶつかる箇所が発生します。
樹脂は金型内で冷えながら流れる為、樹脂がぶつかる境目にウェルドラインと呼ばれる不良が発生する可能性があります。
[ウェルドラインの事例紹介記事]
> 射出成形における不具合『ウェルドライン』の発生原因と対策方法【射出成形の不良対策事例 #4】
また樹脂は熱して溶かす事でガスを発生させ、金型内にある空気も押し込みながら流れる為、末端まで樹脂が到達した際に空気やガスの逃げ場がないと、ガスパックやエアトラップと呼ばれる箇所が発生します。
結果、ボイドやシルバーストリーク、ショートショットと呼ばれる不良が発生する可能性がでてきます。
しかし流動解析ソフトを使用し、樹脂の流れのシミュレーションを可視化することで、設計段階からそれら不良発生の可能性を見出すことができるのです。
[ボイドの事例紹介記事]
> 射出成形における不具合『ボイド』の発生原因と対策方法【射出成形の不良対策事例 #5】
[シルバーストリークの事例紹介記事]
> 射出成形における不具合『シルバーストリーク』の発生原因と対策方法【射出成形の不良対策事例 #3】
[ショートショットの事例紹介記事]
>射出成形における不具合『ショートショット』の発生原因と対策方法【射出成形の不良対策事例 #8】
流動解析で出来る事②
流動解析には他にも成形品の変形形状・変形量の把握をする事が出来ます。
射出成形では熱を加えて樹脂を溶かしますが、熱を加える事で樹脂は膨張し、冷却すると収縮します。よって冷却をする過程で、変形やヒケと呼ばれる凹みが発生するリスクがあります。また、ガラス繊維入りの材料などは繊維の方向によって通常の樹脂と変形が異なる場合もあります。
それらも流動解析を行う事でリスクがあるかどうかを設計段階で解析する事が可能なのです。
[ヒケの事例紹介記事]
>プラスチック成形品の意匠面に発生したヒケの対策方法【射出成形の不良対策事例 #1】
[ヒケの対策・改善を学ぶ記事]
>ヒケの発生する原因とその対策方法とは?プラスチックの成形不良を専門家が詳しく解説
流動解析のメリット
流動解析の最大のメリットは設計前に成形性の事前検討が出来る事です。
樹脂は何十種類もあり、それぞれに流動性など特徴が異なります。ゲートの位置や方式、サイズによっても樹脂の流れが異なります。
過去に製作した金型をそのまま作り直すなら別ですが、多くの場合は多少なりとも今までと異なる形状の製品を作るので、知識や経験だけではカバーしきれない部分があります。そこを流動解析する事で、成形時に起こりうる不良リスクを設計段階で洗い出し、事前に金型設計での対策や、製品形状の修正をするなどして金型製作をする事が出来ます。
つまり、金型完成後の修正を減らせることが最も大きなメリットと言えるでしょう。
流動解析の内容
充填(FLOW) /保圧(PACK)
金型に樹脂を流す(充填)際にかかる圧力と樹脂の温度を解析します。
これによりウェルドラインや末端に発生するエアトラップ・ガスパックの位置等が把握できます。
繊維方向解析(FIBER)
樹脂の中にガラス繊維や炭素繊維を含む材料があります。そのような繊維入りの樹脂の場合、充填時の繊維方向が変形不良に繋がってしまったり、部分的に強度が異なって成形される可能性があります。
例えば同じ製品、金型仕様でもABSとABSガラス入りであれば、変形の仕方が異なる事があるのです。よって、樹脂の流れとは別に繊維の配向を解析する必要があります。
図のように矢印と数値で表されます。
数値は繊維方向が整いやすい箇所ほど1に近く、整いにくい箇所ほど0に近い値となります。繊維の方向が整列している箇所ほど強度が低くなります。
変形(WARP)
上記で解析した充填(FLOW) /保圧(PACK)、繊維方向解析(FIBER)を基に製品の変形量を解析します。
この時点で変形量が数値化できるので、例えば、どうしても変形してしまう製品は、金型を逆反りで製作して、成形時の変形が起こる事で変形方向を相殺し、製品図面通りの形状にする事も可能です。
射出成形の金型では決して、製品図面通りに鉄を削るだけでは、理想通りの製品ができるものではありません。金型の中に様々な工夫、機構を入れていく必要がある為、流動解析で事前に数値化して検討出来るのは、結果的に納期短縮やコストダウンにつながるケースが多いのです。
流動解析の精度を高める為に
成形条件の設定
まずはゲート位置、形状、サイズをそれぞれ設定。
※カルフォンゲート(円弧形状)、サイドゲート(矩形)、バルブゲート(円筒形)
ランナーのサイズは解析結果の差に大きく影響はありませんが、ゲートの大きさと樹脂の流入する向きについては樹脂の流れに影響があるため、仕様に沿った条件にする必要があります。
以下は同条件下でのサイドゲートとカルフォンゲートの充填時間です。
ゲートサイズは同一であるため、樹脂の流入する向きの違いのみとなりますが 、製品部の充填時間は樹脂が下から流入するカルフォンゲートより、横から流入するサイドゲートの方が約1.5秒早いです。
たったの1.5秒と感じる人もいるかと思いますが、この製品を仮に1万個生産するのであれば、15,000秒=4時間10分の短縮につながります。
射出成形は大量生産に適した工法です。数万~数百万個生産をする製品も多いので、秒単位の短縮が出来る事は生産コストの削減にも大きく関わります。
成形機仕様に沿った成形機を設定する
成形機はどれも同じに見えるかもしれませんが、成形機ごとに仕様は異なります。
特にスクリュー径は計量位置の算出に関わってくるため、計量位置ごとに射出速度を変える設定をする場合は、使用する成形機仕様と同じスクリュー径のものを用いる必要があります。
金型設計段階では成形メーカーまで選定をした状態で、使用する成形機のスペック情報まで入手しておければ大丈夫でしょう。
指定の樹脂材料、または近い物性の樹脂材料を設定する
材料によって物性が異なります。どこのメーカーのどの品番の材料かで物性は異なるので、そこまで指定できると精度は高まります。
一般的な樹脂材料は豊富に解析ソフト内に登録されています。
ただし、タルクや長繊維ガラスなどの特殊な素材が含まれた樹脂は材料に登録されていないので、その場合は樹脂メーカーから物性表を入手して、近い物性の樹脂材料で解析を行います。
精度を高める為には、より細かく条件を設定する事で、精度の高い解析を行う事が可能です。
射出成形では、製品形状、金型仕様、樹脂材料、成形条件の大きく分けて4つの要素が密接に関係して成形品が出来上がります。どこかを少し変更するだけでも結果が異なる為、より精度の高い解析を行うためには、事前にどこまで仕様を固められるかで決まってきます。
【射出成形ラボの簡易金型サービスはこちらより】
> 最短納期を2週間で!180ton射出成形機用の簡易金型を、60万からご提供いたします。
流動解析の注意点
流動解析を行えば、不具合が0になるという事ではありません。
前述した通り射出成形では、複数の要素の絶妙なバランスによって成り立っています。最終的には「成形条件」による調整や製品によっては金型のチューニングが必要になります。
しかし、人の目では見えない樹脂の流れを解析できるので、設計段階でのリスク検知と対策を取る事が可能です。これは、金型製作後の修正を最低限に抑える事には大きく役立ちます。
流動解析をせず金型製作をしトライ後に変形不良の改善ができず、樹脂材料を変更した結果、寸法が変わってしまい金型の作り変えをした、という実際のお客様のお話も耳にします。
よって大きな不良リスクを大きく減らし、より精度の高い金型製作を行う為のツールが流動解析なのです。
【射出成形ラボサイトで、流動解析関連の不良事例コンテンツを見る】
>流動解析で『ウェルドライン』を事前に把握 – 金型でのガス抜き位置を予測 –
>流動解析にて『反り』を事前シミュレーション – 金型製作後の設変を低減 –
CAE解析まで対応する関東製作所
関東製作所の射出成形金型部門では、標準的に金型設計時に流動解析を実施しております。
特に中大型の成形品の場合、万が一の金型作り変えが発生すると、大幅に納期が延び、コストアップになってしまいます。事前の流動解析は、金型の修正にかかる納期短縮、コストダウンにつながると考えております。
また、成形を担当する側も経験と知識から成形条件の微調整を行うことも必要です。設計側と成形側の両者にこれらの知識があってこそ、思い通りのプラスチック成形品が生み出せるのです。
すなわち、プラスチック製品開発においては『設計』『金型』『成形』に対する知識や経験を豊富に持っている専門家に相談する事が大切です。
当社、関東製作所では、プラスチック製品開発のベストパートナーとして、お客様の生産技術代行を行っております。射出成形の業務に30年以上の経験を積んだスタッフが多数在籍しており、問題解決のノウハウを保有しております。
何か製品開発でお困りの事があれば、是非ご相談下さい。