【協働ロボット導入事例】工場の省人化にいち早く取り組む(株)トーカイ・アピア様 そのメリットを語る!
省人化装置
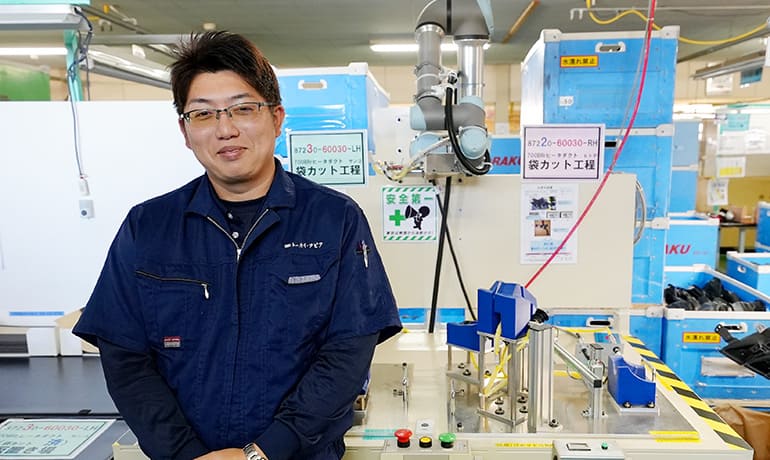
私ども関東製作所グループは、現代の製造業界における『省人化』への潮流は肌で感じています。長年、プラスチック成形品の『仕上げ・後加工機』を多数製造して参りましたが、より適応力・柔軟性の高い協働ロボットの企画・製造への取組みも近年強化して参りました。
今回は満を持して、我々が製作した『超音波カッター搭載の協働ロボット』の導入事例をご紹介いたします。実際に稼働している動画も本記事には掲載していますので、ぜひお楽しみください。
ご協力いただいたのは岐阜県大垣市にある、プラスチック成形品の加工・専用加工機作成を手掛ける株式会社トーカイ・アピア様です。取締役専務の青木様に、実際に導入いただいてのリアルなお話を頂きました。
自社工場の省人化、ロボット導入をご検討中の方にはぜひ!お読みいただきたい内容となっております。
目次
協働ロボット導入!ブロー成形品の捨て袋をラウンド切削する超音波カッター
【関東製作所】
製作のきっかけは、成形品の製造を行っているキョーラク株式会社のデザイン担当の方からのご相談でした。「今回のブロー成形品の開口部がどうしてもラウンドした形状になってしまうので、それを後加工でカッティングきる装置を造れないか?」と。
今まで数多く製作してきた『切断機』などは再現できる動きが単純なため、今回のようなラウンド開口部のカッティングには6軸を有する『協働ロボット』での対応が最適と判断しました。
また『超音波カッター』で『発砲ダクト』を切ってみた際、とても切れ具合の良さを感じたため、関東製作所 加工機事業部として『超音波カッター搭載の協働ロボット』の提案を行い、晴れて受注生産に至りました。
成形品を“切削する”という動きのティーチングの難しさ
もともと協働ロボットとは、主にピッキング作業に使用されることが多いです。ティーチングの方法もスタートポイントと終点ポイントを決め、また中間点で通したいポイントも指示すれば、比較的単純なティーチングだけで設定は可能です。
しかし今回は、プラスチック成形品のラウンド形状をした開口部の切削。切削面に対して、カッターの刃が垂直に進むような動きを再現しなければなりません。
さらに成形品の開口部はラウンドした形状のため、斜めに稼働させたり、狭い範囲で下から上にすくったような動きが必要になってきます。
総じて、とても複雑なティーチング作業を要しましたが、長年、省人化装置を作り続けて培ったプログラミングスキルで、特異な成形品の後加工作業が安定供給できる協働ロボットを納品することができました。
【導入効果①】100V電源で稼働!設置場所を選ばないという最大メリット
【関東製作所】
では、弊社製の協働ロボットをご導入いただき、実際に感じたメリットはどんな点ですか?
【株式会社トーカイ・アピア 青木専務】
100ボルトの電源で稼働できるのが最大のメリットだと感じます。
弊社は産業ロボットも1台導入していますが、やはり200Vの電源を要するので、設置場所が限られてしまいますね。そのぶん協働ロボットは100Vで動くので、設置場所に困りません。弊社も、現在2階の作業スペースで協働ロボットを稼働させていますが、備え付けの電源ですべて事足りてます。
↑赤い点線で囲った範囲が協働ロボットの設置範囲です。非常に省スペースで作業が可能です。
もし産業ロボット導入で200V必要となると、建屋の大元から工事しないと設置できないという会社も多々あると思いますし、簡易的なプレハブ型の工場であっても、協働ロボットなら難なく設置できると思いますね。
協働ロボットと産業ロボットのメリットデメリットはそれぞれあります。
正直まったく違うものとして捉えたほうが良くて、自動車で言うところの排気量600ccと排気量4Lの違いのようなものです。パワーやスピードを要求するなら、産業ロボット一択になると思います。
しかし、稼働させるラインに見合っていれば協働ロボットの方が小回りがきいたりする点は有利だと思いますし、また設定次第では限りなく安定供給できるスピードを確保できますしね。
今回の協働ロボットの設定に関しては、関東製作所さんのところでかなり詰めていただきました。
【導入効果②】ローコスト!エントリーモデルとしての敷居の低さを実感
【関東製作所】
今回の省人化装置導入に関して、設置場所や取り回しやすさも考慮すると、簡易的導入が可能な協働ロボットに非常にメリットを感じていらっしゃるということですね。
【株式会社トーカイ・アピア 青木専務】
そうですね。特に感じたのは、コスト的な問題も考えると、ロボットに対する“エントリーモデル”として協働ロボットを使ってみるのも、一つの選択肢としてありなのかなと。
やはりコスト的な問題で、「産業ロボットだと高額」という点がどうしても障壁になってしまうと思います。協働ロボットだと、ある程度は条件次第でコストを抑えられます。
例えば、「ロボットを入れてみたいけど、どんな感じなんだろう?」とか、「ラインの隙間作業をロボットで代行してみたらどうだろう?」と、導入にいま一歩踏み込めない方々にとっては、トライしやすいと思います。
我々のような中小企業ではロボット導入が当たり前になってきていますが、さらに小規模な会社様や、例えば後継者問題で人手不足に悩んでいる方々には、事業の持続にも繋がるのではないかと感じますね。
導入しやすい分、そこから協働ロボットの良いところ・悪いところを知り、「じゃあうちはもっと大きい仕事をこなすために、でかいのも入れようか」「協働ロボットでも、もう少しスペックが大きいのにしよう」など、その後の展開で、選択肢の幅は大きく広がるはずです。
【導入効果③】ティーチングが容易!都度製品が変わるラインには最適
※作業者がロボットに成形品をセットしている写真です。
特に力を要する作業ではないので、ご年配の方でも無理なく対応できます。
【株式会社トーカイ・アピア 青木専務】
例えば、ある工場内で製品ラインに頻繁に変更がある場合、その都度ティーチングを変えないといけないとなったら、断然協働ロボットの方が楽ですね。ティーチングが楽なので。手離れが良い製品で簡単な軽作業だったら、ロボットに任せておいた方が安定供給はできます。人間の場合、休憩などで現場を離れることは避けられないですからね。
【関東製作所】
確かに、産業ロボットは全部コントローラーで動かさないといけないので、「これをこっちに動かすためには、どのボタンを押せばいいのか?」など、かなり慣れてる人にしかティーチングは出来ないですからね。我々関東製作所の人間でも、対応できる人物は限られてきます。
6軸もあるので、「こうも動かさなきゃいけない、こうもあるし、こうもあるし…」。
複雑な動きに適した操作方法っていうのが直感的にパッと出てこないと出来ないんだろうなと思いますね。
その点協働ロボットは動きが分からなくなったら、ダイレクトでそのままグーって動かすだけの話なので難しいこと考えなくても出来るんですよね。
【導入効果④】怪我など事故件数0へ!安全に配慮した盤石のプログラム
【関東製作所】
今回の『超音波カッター搭載の協働ロボット』の導入後、社員の方の怪我など、事故数への変化はありましたか?
【株式会社トーカイ・アピア 青木専務】
怪我などの事故数は『0』になりました。
元々、ブロー成形品の『バリ取り』は全て人の手で行っていました。単純な後加工機では複雑な動きは再現できないので。
手加工でバリ取りを行う際、どうしてもナイフが力加減で抜けて刺さるとか、切ってしまうというのが付いて回っていたんですけど、その手作業が協働ロボットのアームに置き換わったわけですからね。そこは非常に大きな変化でしたね。
また、その安全面も相談していて、ロボット近くに人の手が介入すると完全に止まるようプログラムしてもらっています。
設定次第で安全性ということに関しては、産業ロボットでも協働ロボットでもレベルは一緒だと感じます。
【関東製作所】
ひとつひとつ人の手で行う作業だったので、導入前はきっと製品の個体間で仕上がりに差が出やすかったと思うのですが、そこをロボットに任せたことで品質もさらに向上しましたか?
【株式会社トーカイ・アピア 青木専務】
概ね一定のレベルを保ってくれています。
ただプラスチックの成形品は生き物なので、春夏秋冬とおし、ラインのスタート時だけはバラつきが出るのはしょうがないですね。そこだけは必ず品質に対して平均的な仕上がり状態をとってやるようにしています。
一度平均とって決めてしまえば、そのままずっと稼働させ続けさえすればいいので、そこも大きなメリットですよね。
関東製作所のサポート体制 迅速な対応でラインの停滞を極力抑える
【関東製作所】
あと協働ロボット自体コンパクトなので、必要な時だけ動かして、不要な時は隅に置いておけて、取り回しやすさはやっぱり大きいですよね。
【株式会社トーカイ・アピア 青木専務】
大きいです。
ただ、原点出しなどの調整をしないといけないという問題は都度でます。しかし、それも産業ロボットと比べればアンカー固定の必要が無いので動かしやすい、ライン切り替えもしやすいです。
もしも自分たちが調整方法に自信ないなって時は、関東製作所さんフットワーク軽いので、すぐ来てくれて調整してくれるサポート体制は、本当にありがたいです。
フットワーク軽く対応いただけることは、ロボットの利便性以上に重要なことだと思います。
私たちは特に自動車関連の製造に従事していますので、例えば丸一日ラインが止まってしまうことなんて、死活問題にも繋がりかねません。その点、関東製作所さんも長年自動車部品製造に従事されてきているので、ラインが停滞することの危険度に対し、同じ緊張感を共有して取り組んで頂けています。
まだまだイメージが膨らむ!協働ロボットの可能性と活用アイディア
【関東製作所】
青木専務、本日はありがとうございました。特に、この東海地方でもいち早くロボット導入に先駆けた御社の生の声を聞けて、改めて気付かされた点も多々ありました。
今後、特に協働ロボットに関しての更なる展開を考えていらっしゃったりしますか?
【株式会社トーカイ・アピア 青木専務】
協働ロボットを導入したことで、様々なメリットを享受出来ていると感じます。
しかし課題はまだあります。というのも、今まで手作業で行ってきたことをロボットに任せることで、担当者の拘束時間を大きく減らすことはできました。しかしロボットにカットさせるために、成形品をセットして、カットが終われば取り出して…などは、まだ人の手がかかっているんですよね。常にロボットのそばに人はついていなくちゃいけない。
いま構想しているのは、ロボットのハンドで成形品をセットして、そこで置き換えが終わったらそれを取り出す作業も協働ロボットに任せてしまえば、横でパッキンを貼る人だけで、あとは自動供給状態になり、ラインに人は不要になります。その考えを応用すれば、より究極の人員削減が実現できそうですね。
工場へのロボット導入は、本当に無限の可能性を秘めていると思いますよ!
さいごに
記事を最後までお読みいただきありがとうございます。
私ども関東製作所グループは創業当初より、プラスチック製品開発にかかわる事業を広範囲にわたって取り組んでまいりました。特に私が所属するメカトロニクス事業部では、成形品の後加工を自動化できる装置製作を得意としています。
機械設備としてクライアント様に納入することを主な業務としていますが、最も大きな強みは、クライアント様の環境に沿った『最適なアイディアや提案』を提供することだと自負しております。
クライアント様のニーズや環境は千差万別です。A社様で提供したシステムが、そのままB社様に適用できることはまずありません。それぞれのクライアント様の環境を把握し、お話をよくうかがい、そこで初めて今まで培ってきた経験値を取り出し、最適案を導き出しています。
プラスチック製品開発でお困りごとはありませんか?
御社の工場ラインの最適化を検討してみませんか?
経験値豊富なスタッフがご対応させていただきます。
> 協働ロボットのメリット・デメリットとは? 産業ロボットとの違いと可能性の高さを解説
> 製造業界に求められる省人化とは? 改めておさえておく『省人化』『省力化』『少人化』の違い