ミロク機械社製ガンドリルを2機配備 『大型ブロー成形金型』の製造に最適化された環境
金型
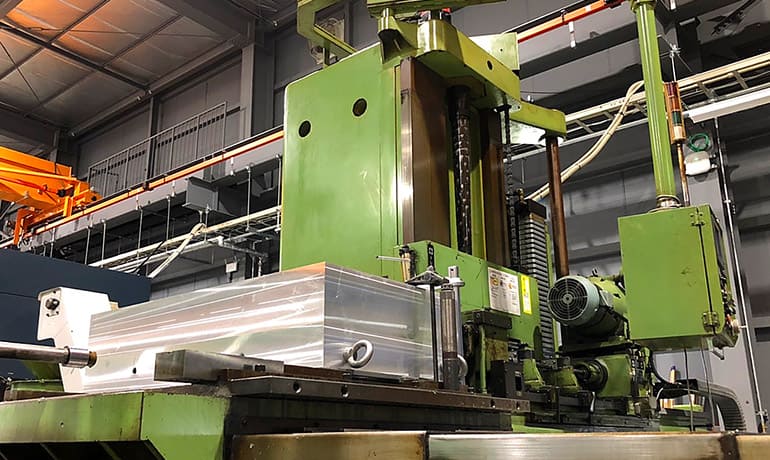
株式会社関東製作所 関工場の井上です。
前回の記事では、片持形プラノミラーを活用した『社内面削』の有効性について紹介しました。今回はミロク機械株式会社のガンドリルについて紹介します。
> 大型の『ブロー成形金型』製造の短納期・低コストを可能に! 自社工場内で『面削』できる強みを紹介
金型製造に精通した方なら十分ご承知とは思いますが、ガンドリルとは主に水冷穴、構造によってはガス抜き穴やバキューム穴を加工します。
そう、金型製造工程においては無くてはならない存在ですね。もちろん小型の金型やコマ部品などの場合はラジアルでそれらの穴をあけることが一般的ですが、特に中規模や大型の金型には必須の機械と言っても過言ではないでしょう。
目次
ミロク社製ガンドリル『MHG-1500』『MSEG-1200S』を所有
当社 関東製作所では2機種、ミロク機械株式会社製のガンドリルを所有しています。
私が所属する関工場では、「ミロク機械株式会社 ガンドリルMHG-1500」を配備しております。加工範囲は1200×900 穴深さは1000まで1回の段取りで加工が可能です。それ以上の大きさの場合には段取りを2回にすることで最大2400×1800 深さ2000が対応できます。
また東京の猿江工場では、「ミロク機械株式会社 ガンドリルMSEG-1200S」を配備しております。1000×250 深さ700が最大加工範囲です。これもMHG-1500同様、段取りを2回にすることで2000×500 深さ1400まで対応可能となっております。
↑写真は関工場の「ミロク機械株式会社 ガンドリルMHG-1500」
個人的な見解ですが、ガンドリルを所有している金型屋は少ないように思います。
私は以前、過去繁忙期にガンドリルの外注を検討した時期もありました。しかしガンドリルを所有している外注先が少ない為、コスト、納期、タイミングが合わず、その時は自社の生産計画の調整で何とか乗り切ったという経験があります。
ミロク社製のガンドリルを2つも配備している理由
関東製作所のブロー成形金型の生産拠点は、東京の3工場と岐阜の関工場です。
拠点により特色があり、主に『小~中規模金型』を東京工場で生産しています。ここでは製造サイクルが早く、工程ごとのスピードを重視して製造しています。
また『中~大型金型』は関工場で生産します。中~大型なだけに工程毎にかかる時間が長く、ここでは効率を重視して製造をしています。
以上のような理由で、小~中規模金型を量産する東京に「ミロク機械株式会社 ガンドリルMSEG-1200S」を。大型金型の生産数が多い関工場に「ミロク機械株式会社 ガンドリルMHG-1500」を配備する運びとなりました。
ガンドリル作業においても『工数削減』『品質管理』を
当社ではガンドリル加工においても、徹底して工数削減、低コストの追及を行っています。その取り組みを3つ紹介します。
【取組み①】段取り治具を用いて段取り工数削減
ご承知の通り、金型を製造する上で、水冷穴やバキューム穴の位置精度は、さほど要求されるものではないでしょう。すなわち、この『ガンドリル作業』において重要なのはスピードです。それを実現させるために、段取り治具には4つの機能を備えています。
突き当て基準を設ける
原点の座標は機械座標に入力されており、ワークと突き当て基準に隙間が無いことを確認すれば毎回加工原点を設定する必要がなくなります。
また突き当て基準はX0とX1200の位置に設けています。ガンドリルの加工範囲は1200です。という事はX0からX1200までとX1200からX0までの合計2400のワークサイズに対応できることになります。
突き当て基準を取り外し式にする
上記でもあるように1200以上のワークを加工する場合、片方の突き当て基準が干渉してしまいます。そのため突き当て基準は取り外し式にしました。この取り外し式にすることで加工範囲2400を実現可能にしており、また大型金型に対してもスピード感を落としません。
突き当てブロックにクランプ用のM16を設置
原点側を確実にクランプすることができます。
M16 50ピッチベースを設置
M16 50ピッチベースを設置。これによりどんなワークサイズも容易にクランプをすることができます。
【取組み②】NCプログラムでの加工入力と図面確認を併用したミス防止
当社ではガンドリルのNCプログラムの作成に、手入力ではなく、2DCAMを使用しています。
加えて現場のオペレーターは、出力した紙の図面で確認をしながら作業を進めております。
加工全体に言えることですが、ヒューマンエラーは徹底的に削減しないといけません。それに、金型の水冷穴加工を万が一間違えてしまった場合、そのブロック材を廃棄せざるを得ないケースも充分考えられます。
そのためプログラム作成には2DCAMを使用し、かつ図面で確認することにより、徹底的にヒューマンエラーを防いでいます。
【取組み③】ミロク機械様から伝授!切粉の『絡まり・詰まり』防止の技
金型の構造によっては穴を『段付き穴』にする必要が出てきます。この加工をするためには少し技が必要です。今回は特別にミロク機械株式会社様からご指導いただいた技を紹介いたします。
穴があいた状態でさらに径の大きい穴を加工すると、切粉がつながってしまいます。この状態で加工を進めると切粉がドリルに絡まる、また切粉排出口が詰まることとなり、加工機が止まってしまいます。これを回避するためには切粉を分断させる必要があります。
ここで必要な技が、
『1mm進んで5秒待つ』
という加工方法です。
この方法を必要な深さまで繰り返すことで、切粉を分断しながら加工をしていきます。
以上のようにガンドリル工程においても、長年蓄積してきた経験をもとに極限まで工数削減に取り組んでいます。
プラノミラーとの相乗効果! 『面削』から『穴あけ加工』までの迅速さ
関東製作所 関工場では、『ミロク社製ガンドリル』を面削用の『寿社製片持形プラノミラー』のすぐ横に配置しており、面削の終わったワークをクレーン作業たった1分でガンドリルに乗せ換えることができます。
『生産性』という観点において、ワークの移動や段取り作業に費やす時間を徹底的に無くすことは、製造業界に携わる者なら当然、常に意識していないといけません。
それを実現させるために考えた結果が、この関工場においてプラノミラーとガンドリルを両方配備するといった結論でした。そしてその両者間のワーク移動にも、徹底的に時間を費やさないことを考慮された工場内レイアウト。
ワークを業者から最短で納入してもらい、その時点から当社のタイムスケジュールで生産が始まるわけです。
このスタートダッシュの迅速さにより、工場内一貫製作による短納期対応が実現できています。これが関工場の何よりの強みです。
まとめ
以上の取り組みは当社の経営理念でもある、「顧客満足」を重視した結果の集大成です。「コストパフォーマンス」が高く、「迅速」な金型製造をお客様にお届けできるよう長年、工夫に工夫を重ねて参りました。
ガンドリルの工程は工場内一貫製作を実現させる重要なポジションです。
関工場も東京の3工場も、現在のような金型生産量を確保できているのは、ミロク社製ガンドリルを配備していることが大きく寄与しているのは間違いありません。
まだまだ、私たちの「顧客満足」への創意工夫は止まりません。
今回の機械設備だけでなく、様々な側面で「お客様の課題解決」を実現できる取組みを続けて参ります。