大型の『ブロー成形金型』製造の短納期・低コストを可能に! 自社工場内で『面削』できる強みを紹介
金型
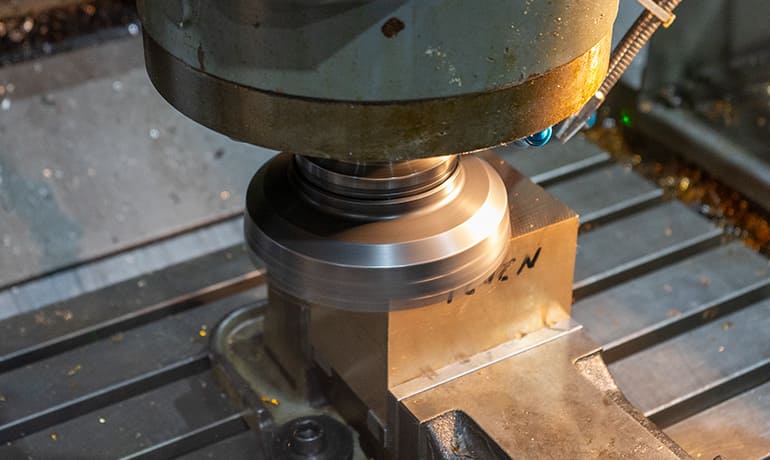
株式会社関東製作所 関工場では、ブロー成形金型を工場内で一貫製作できる環境を整えております。これにより、お客様には『短納期・低コスト』での金型製造を提供できると自負しております。その為に関工場では、必要な設備を全て揃えてきました。
今回は、関工場CAMチーム所属の井上が、特に大型のブロー成形金型製造におけるスタートの工程、片持形プラノミラーを活用した面削についてご紹介いたします。
目次
市場では、ブロー成形金型の大型化への需要が拡大
ここ3~4年間で、お客様要望による『サイズが大きいブロー成形金型物』の需要が高くなってきました。個人的な考えですが、その最も大きな理由は『製品のコストダウン化』が関係していると思います。
コストダウンをする為には生産性を高めなければなりません。生産性を高めるには工程を集約する必要があります。
さらに昨今の自動車業界に関しては、軽量化の流れもあります。
以上を踏まえると、今まで金属で作っていた大型の部品も『樹脂化してしまおう』という考えに行き着きます。(知っていますか?現在では樹脂製が当たり前の、車のハッチバックは、昔は鉄で出来ていたんですよ!)
ブロー製品(中身が中空のプラスチック製品)の成形時に、金型の構成を工夫することでコストダウンできる方法として、下記の3点が挙げられます。
- 複数個で構成されていた部品を、一つの部品としてまとめる
- 一つの金型でL側、R側など左右対称の部品をまとめ、一度に複数成形する
- 大型の成形機が登場してきたので、金型も大型化でき、一度に同じ製品を複数個成形する
このような背景から1,500を超えるブロー成形金型需要が多くなってきました。
この需要に応えていくことで、関工場は大型金型に対してのノウハウを蓄積しつつ、経験値を上げていきました。
ガソリンタンク、ラゲッジボード、仮設トイレのドアや壁面パネルの金型、浴槽パネルの金型、金型自体が浴槽のような深い金型など、今では関工場の主力技術となっています。
片持形プラノミラー導入で最大幅3,000のワーク面削を実現
そのような市場の変化に対応するため、㈱関東製作所 関工場では、寿工業株式会社の片持形プラノミラーを導入しました。片持形タイプなので加工機のベッドを超えるサイズでも面削することができます。
その特性を生かし、最大2,000×3,000のワークの面削が可能です。
水平方向にはφ315、垂直方向にはφ250のフライスが付いています。
当社では材料を社内で6Fしているため、この2方向のフライスがあることで、水平方向の面削後、段取りを変えることなく、垂直方向の面削作業を進める事ができます。
導入当時、水平方向はφ200のフライスでした。
しかし大型金型に対応する為に、既製品の最大径φ315のフライスに変更。
同時にチップも見直しました。
以前使用していたチップに対し、すくい角のある物に変更し、インサートクランプはねじ止め式になりました。そうすることで送り速度を上げられるようになり、切りくずの排出性も上がりました。
その結果、工具径で約1.6倍、切削速度は1.3倍、総合して約2.1倍の効率アップにつながりました。
自社工場内『面削』は、ガイドブロック取付時の精度確保にも!
当社が面削にこだわる理由は、ただ単に『クロカワ』を削るためだけではありません。当社では、金型のNC加工後に再度、プラノミラーによる側面の面削を行っております。
と言いますのも、金型製造の工程の中でも、特に高い精度を求められるのが『ガイドブロックの取り付け』でしょう。承知の通り、金型のCAVI側、CORE側を合わせる、たいへん重要な基準になります。
ガイドブロックは金型の長手側面に取り付けます。
当社ではこれを効率よく取り付けるために、CAVI側、CORE側をいったん被せた状態で固定をし、側面を同時に最少面削します。
こうすることで、ガイドブロックの取り付け面は必ず同一平面になります。
あとはガイドブロックをあらかじめインローさせた状態で金型と水平に取り付ければ、間違いなくグイチにはなりません。
↑①CAVI側とCORE側を被せて固定し、側面を最小面削する
↑②側面は必ず同一平面になる
↑③その状態でガイドブロックを取り付ければ、グイチには決してならない
このようにNC加工後にもう一度側面を面削することで、品質と組立作業の効率アップに大きく貢献します。ここには当社のノウハウと、先人の知恵が多く含まれており、ブロー成形金型のQCDの一端を担っています。
ただ大型金型に対応するだけでなく、効率も最大限まで上げる事で金型製作全体のスピード感を増すことになります。
金型の短納期・低コスト追及の結果、特急案件にも対応可能に!
当社では短納期、低コストの追及を常に行っています。今回はブロー成形金型のスタートの部分、『面削』の加工工程について紹介しました。
これらの加工を社内で行っているメリットとして、もう一つ大きなことがあります。
それは特急対応の場合です。
基本的には事前に予定を計画し生産管理をしているのですが、まれに特急での対応を求められることがあります。この場合、ワークさえ入荷できれば後は工場内で生産スピードを調整することができます。(もちろん現実的な日程という事になりますが・・・)
大まかですが、参考値として『面削から水冷穴あけ』までの工数を紹介します。
ワークサイズは 1,500×700 を例に挙げます。
ワークの厚み=230未満 | ワークの厚み=230以上 | |
---|---|---|
アルミ材 | 約10時間 | 約12時間 |
鉄材 | 約15時間 | 約19時間 |
例えば、朝8時にワークが入った場合、アルミ材であれば翌日の午前中、鉄材であれば翌日の夕方には完了します。
㈱関東製作所は『大型金型製造』の短納期・低コスト化が強み
前述した通り、関東製作所関工場の強みは3つあります。
①工場内一貫製作・・・ワークの面削から請け負うことができる
②短納期対応・・・クロカワでのワークが入り次第、即、製造がスタートできる
③大型金型対応・・・最大2,400×1,800 深さ2,000まで加工可能(面削・ガンドリルの場合)
冒頭でもお伝えしましたが、近年のブロー成形金型は、大型化傾向にあります。
ブロー成形金型製造にスピードが重視されるように、プラスチックの成形工程で生産性を高めるには、
・いかに短いスパンで多くの製品を成形できるか
・部品点数を減らす工夫をするなどし、可能な限りコストダウン化を図るか
を追求してきた結果だと思います。
金型が大型になると、当然金型の生産性は下がります。その中でも高い『金型の生産性の維持』を目指し、私たちは工程の見直し・改善を進めることで、コスト削減、短納期に対応をしてきました。
繰り返しになりますが、私たち㈱関東製作所関工場は、大型金型の対応、短納期・低コスト製造の提案には自信があります。
金型製造の、特にそういった点で課題をお持ちのお方、是非一度ご連絡下さい。
また、私たち関工場へのご見学なども、ぜひお気軽にご検討下さい。
きっとお客様のプロジェクトを円滑に進めるイメージが沸いてくるでしょう。
> ミロク機械社製ガンドリルを2機配備 『大型ブロー成形金型』の製造に最適化された環境