ダイレクトブロー成形・3次元多層ブロー成形の違いとは?「ブロー成形」の進化を徹底解説!
金型
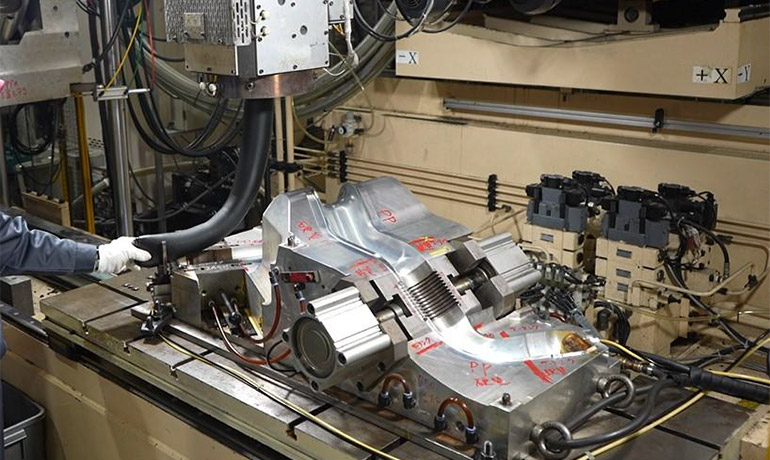
中空構造の製品成形に適した工法「ブロー成形」。一言にブロー成形と言ってもその種類は様々です。今回は、代表的なブロー成形の「ダイレクトブロー成形」と、技術の組み合わせにより進化した「3次元多層ブロー成形」に焦点を当て、それぞれの成形工程から特徴、工法選定の方法まで詳しく解説します。
目次
ダイレクトブロー成形とは?
「押出ブロー成形」や「中空成形」とも呼ばれるブロー成形の代表的な工法です。
ダイレクトブローの成形工程
①押出
プラスチック材料をホッパーに入れ、押出機内で加熱し、溶融状態にします。溶融された樹脂は、押出スクリューを介して「ダイ※」に送り込まれます。
ダイの形状に沿って樹脂が押し出され、中空チューブ状の「パリソン※」が形成されます。
- ダイとは
- 押出機から送り込まれた溶融樹脂が流れ出る出口のような役割を果たします。
ダイの径を変えることで、パリソンの太さをコントロールします。
- パリソンとは
- ブロー成形において製品を成形する前段階で作られる円筒状または中空のチューブ状の溶融樹脂を指します。
②型締め・冷却
押し出されたパリソンが金型内に入ると、左右に分かれた金型が型締めされます。金型が閉じた状態で、ブローピンから圧縮エアーがパリソン内部に吹き込まれ、パリソンを膨らませて金型の内側に押し付けます。その後、冷却装置により樹脂が急速に冷却され、製品形状が固化されます。
③型開き・製品取出
製品が十分に冷却され固化したら、金型を開き、成形品を金型から取り出します。成形品はパリソンの端部が余剰部分(バリ)として残るため、バリ取りを行います。
下記の動画では、ダイレクトブロー成形の工程を詳しくご覧いただけます。
使用される樹脂材料
主に熱可塑性樹脂のPPを使用します。TPVなどのエラストマーを使用することもありますが、硬質な樹脂での成形が主流です。
ダイレクトブローの特徴とは?
特徴① 後工程「バリ取り」
ダイレクトブロー成形の特徴は、バリを取るための後工程(あとこうてい)が必要な点です。
バリは、金型を閉じる際に、押し出されたパリソンが金型の合わせ面からはみ出すことで発生します。金型から取り出した直後のバリの温度は、150~160度程度です。このバリ取りの方法は、ナイフやニッパーを使用した手作業や、専用のトリミング機やパンチング機を使用するなど様々です。
また、バリ取り後は樹脂が鋭利な状態になっているため、怪我の発生を防ぐほか、シールの貼り付けが必要な製品ではシールが破れないよう、外周部をあぶって処理することもあります。
上記写真は、バリ取り前後の製品比較
バリは粉砕機へ投入され、バージン材(新材)と混ぜ合わせて再利用されるため、材料ロスが少ないです。
特徴② 後工程「切断」
ブロー製品は、金型から取り出された時点では袋状です。自動車のパイプやダクトなど、両端が開口している製品は、「捨て袋」と呼ばれる製品には不要な両端部分を切断し、開口部を作り出す必要があります。
特徴③ サイクルタイムが速い
後述で紹介する3次元ブ多層ブロー成形と比較して成形工程がシンプルなため、同じサイズの製品を成形する場合は、サイクルタイムが速く成形できます。
代表的な製品や製品の特徴
洗剤やシャンプーボトルなどの容器類、自動車のウォッシャータンクやダクト、アウトドア用の水筒やじょうろなど、日用品から工業製品まで幅広い製品に活用されています。
また、3次元ブロー成形や多層ブロ-成形など、その他のブロー成形工法の最小肉厚が1.5~2㎜程度であるのに対し、ダイレクトブロー成形では、最小肉厚0.8㎜程度の薄肉成形が可能です。
3次元多層ブロー成形とは?技術の融合による可能性
3次元多層ブロー成形とは、蛇腹形状を含むパイプなどの複雑な形状を成形する「3次元ブロー成形」と、複数の樹脂を重ねて成形する「多層ブロー成形」を組み合わせた工法です。
主にPP(ポリプロピレン)、TPV(熱可塑性エラストマー)が使用され、必要特性によってはナイロン樹脂の使用も可能です。
3次元ブロー成形と多層ブロー成形の詳細は下記よりご覧ください。
>『3次元ブロー成形』『多層ブロー成形』など様々なブロー成形工法を詳しく解説。
3次元多層ブローの成形工程
①押出
この工程はダイレクトブロー成形と同じで、押出機で樹脂を加熱・溶融し、ダイから中空のチューブ状のパリソンを押し出します。
②パリソンの位置決め
押し出されたパリソンを、金型に正確に配置します。作業者が人の手で行ったり、ロボットアームやエアブロー、真空吸着装置を使用することもあります。
③型締め・冷却
押し出されたパリソンが金型内に入ると、上下に分かれた金型が型締めされます。金型が閉じた状態で、ブローピンから圧縮エアーがパリソン内部に吹き込まれ、パリソンを膨らませて金型の内側に押し付けます。
その後、冷却装置により樹脂が急速に冷却され、製品形状が固化されます。
④型開き・製品取出
製品が十分に冷却され固化したら、金型を開き、成形品を金型から取り出します。
3次元多層ブロー成形は、ダイレクトブロー成形と異なり、バリが発生しないためバリ取りは不要です。後工程では、捨て袋の切断や必要に応じて切削を行います。
下記の動画では、3次元多層ブロー成形の工程を詳しくご覧いただけます。
3次元多層ブロー成形のメリットを解説
メリット① 部品点数・組付け工数の削減
3次元多層ブロー成形は、複数の樹脂を一体成形できるため、例えばゴムの組み付けが必要な製品でも、エラストマーでゴム部を成形することで、部品点数や組付け工数の削減につながります。また、樹脂や金属などのインサート部品も一体成形可能です。
下記の製品は元々、「硬質樹脂部品」「ゴム部品」「金具」の3部品構成で、3部品それぞれを製作して組み付けを行う工数が発生していました。しかし、3次元多層ブロー成形では硬質樹脂と軟質樹脂の一体成形が可能なため、取り付け用のゴム部品や金具が不要となり、部品点数と組み付け工数が削減されました。
メリット② 高い強度
下図のようにL字のパイプを成形する際に、バリが発生するダイレクトブロー成形では、PL(パーティングライン)※ 部分でパリソンを挟みこむため強度が弱く、割れる可能性があります。
一方、3次元多層ブロー成形では、PL部分でパリソンを挟みこむことがないため、ダイレクトブローと比較して強度が高いです。また、異なる樹脂を一体成形できるため、複数の機能を持たせた製品を成形することができます。
- PL(パーティングライン)とは
- 金型の合わせ目にできるラインの事です。ダイレクトブロー成形では、パリソンをPLで挟みこみながら型締めを行います。
3次元多層ブロー成形のデメリット
デメリット① サイクルタイムが長い
ダイレクトブロー成形では、垂直に垂れてくるパリソンを金型で挟むだけですが、3次元多層ブロー成形では、押し出されたパリソンを人の手やロボットで金型内に正確に配置する必要があるため、ダイレクトブロー成形と比較してサイクルタイムが長くなります。
また、複数の樹脂を使用した場合、層ごとの樹脂特性が異なるため、冷却時間が長くなりやすいです。
デメリット② コストが高い
サイクルタイムが長いため、ダイレクトブロー成形と比較して、成形コストは若干高くなります。
また、機械の複雑さから設備自体の費用も高く、3次元多層ブロー成形機の中でもパリソンの吐出量によってマシンチャージ※は異なります。
- マシンチャージとは
- 機械設備の使用料や稼働コストの事で、一般的に成形費用に含まれます。
3次元多層ブローの成形不良
樹脂材料の切り替わり不良
3次元多層ブロー成形では、異なる材料を切り替えて特定の部位に機能性を付与しますが、切り替わりの位置がずれると、特定の機能が必要な部分に、適切な材料が配置されない不良が発生します。
主な原因は、押出機の流量や温度の不安定さ、パリソンプログラムの設定ミス、または金型内での樹脂流動の偏りです。
蛇腹不良
蛇腹構造の製品では、板厚が適切でないと動きや耐久性に影響を与えます。
具体的には、板厚が厚すぎると蛇腹が硬く、動きにくくなり、逆に薄すぎると筋状の痕や破損が発生するリスクが高まります。
パリソンの肉厚制御が不十分な場合や、冷却の不均一、金型設計が不適切な場合に発生し、特に、複雑な蛇腹形状では成形条件や金型の精度が品質を左右します。
3次元多層ブロー成形で作られる製品とは?
自動車部品
振動を吸収する目的で蛇腹形状を組み込んだり、両端を軟質にすることができるため、組み付けのしやすさから自動車のエアダクトやエンジン回りの部品に活用されています。
家電製品
3次元多層ブロー成形は、洗濯機や冷蔵庫のパイプにも活用されています。
洗濯機の排水ホースには蛇腹構造を採用し、柔軟性と耐久性を持たせます。また、冷蔵庫では冷媒配管に使用され、内層にバリア性の高い樹脂を用いることで冷媒の漏れを防ぎ、外層で耐衝撃性や軽量化を実現しています。
用途に応じた、各ブロー成形の工法選定のポイント
ダイレクトブロー成形と3次元多層ブロー成形は、それぞれ特徴や性質が異なります。
「製品形状」「材料特性」「性能要件」この3つの観点から、どちらの工法が製作する製品に適しているのか確認していきましょう。
ダイレクトブロー成形 | 3次元多層ブロー成形 | |
---|---|---|
製品形状 | シンプルな形状(タンク・レゾネータ、ダクトなど) | 複雑な形状(エアークリーナーホースなど) |
材料特性 | 単層構造(100%リサイクル可能) | 多層構造(材料の比率によっては、リサイクル可能) |
性能要件 | 耐衝撃性や耐薬品性、基本的な剛性 | 強度、耐久性、軽量化 |
ダイレクトブロー成形は、比較的シンプルな形状に対応しやすい特徴を持ちます。
一方、3次元多層ブロー成形は、ダイレクトブロー成形では成形できない複雑な形状や、高い機能性を求められる製品に適しています。
まとめ
ダイレクトブロー成形と3次元多層ブロー成形は、それぞれ異なる特徴を持ち、製品の用途や設計要件に応じて使い分けることが重要です。製品の特性や目的をしっかりと見極め、適切な工法を選定することで、効率的で高品質な製品製造が実現します。
㈱関東製作所は、長年ブローの金型製作に従事しており、幅広い知識と経験を有しています。プラスチック製品の製作や工法選定にお困りの際は、ぜひお気軽にご相談ください。
また、弊社では自動機の設計・製造も社内で行っております。ブロー成形品の後工程で発生する切断やバリ取り、検圧、カメラ検査の自動化をご検討中の方は合わせてご相談ください。専門スタッフが最適な解決策をご提案いたします。
> 株式会社関東製作所コーポレートサイトへ
関東製作所は「金型の設計・製作」から「小ロット~量産の成形品の生産」、「省人化装置や専用加工機の設計・製作」「部品の加工・調達」まで、幅広い生産技術代行サービスを行います。
関東・東海・九州・インドネシアより、お客様に合わせたベストなソリューションを提案致します。