インサート成形を詳しく解説|射出成形によるインサートの流れとメリット・デメリットを紹介
射出成形
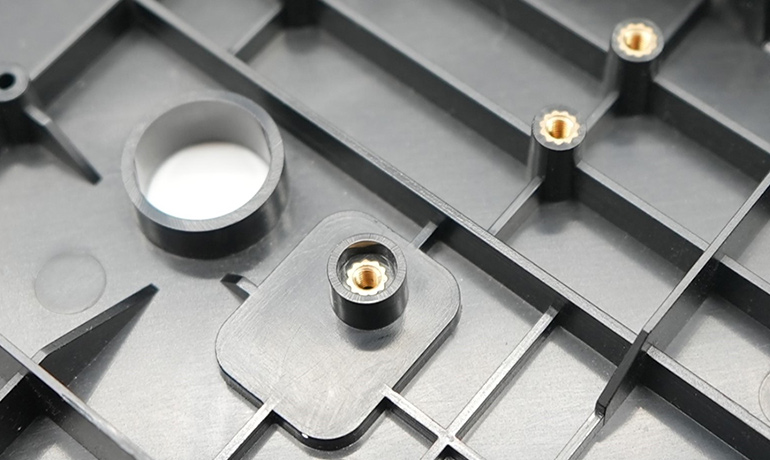
目次
インサート成形とは?
インサート成形とはプラスチック成形方法の一種で、樹脂や金属・他素材の部品を金型に事前に配置し、その上から樹脂を流し込むことで、他素材の部品と一体化したプラスチック製品を成形する技術です。
具体的にはナットなどの金属部品をインサートしたり、1次型で成形した樹脂部品を2次型に取り付けて成形することもあります。特に電子部品や自動車部品などに多く用いられており、製品精度の向上や、製造工数の削減などが可能です。
本記事では、インサート成形の基本的な流れやインサート部品に使用される素材の詳細、またメリット・デメリットについて詳しく解説します。
こちらの記事は、動画でもご覧いただけます。
インサート成形の流れ
① インサート部品の配置
通常の成形と異なるのはこの工程です。
まず最初に、インサート部品を金型内に配置します。この作業は手作業、またはロボットによる自動作業で行います。少量生産の場合は手作業で配置するケースが多く、大量生産の場合は、パーツフィーダーなどを使用して部品の取り付けを機械を用いて自動化します。
どちらにしても、成形中にインサート部品が落下したり動いたりしないように正確に固定することが重要です。
② 型締め
ここからは通常の成形と同じ流れです。インサート部品の配置後、金型が閉まります。
③ 樹脂の射出
金型が閉まると、溶融した樹脂が金型内に射出されます。樹脂はインサート品を包み込むように流れ、そのまま固化されることでインサート部品を固定します。
④ 型開き・取出し
金型を開いて、完成品を取り出します。
このあと説明するアウトサートと異なり、金型から成形品を取り出す時にはインサート部品と一体化した状態になっているため、後工程にて組付け作業などは不要となります。
【射出成形ラボの簡易金型サービスはこちらより】
> 最短納期を2週間で!180ton射出成形機用の簡易金型を、60万からご提供いたします。
アウトサートとは?
インサート成形を知る上で併せて覚えておきたいのが「アウトサート」です。アウトサートとは通常、先に成形した成形品に、後工程で金属部品を組み込む技術です。
組み込み方法としては、アウトサートする金属部品を温め、物理的に樹脂成形品に押し込むような圧入や、樹脂成形品を溶かしながら金属部品を押し込み、冷却して固定するなどの手法があります。
アウトサートのメリット・デメリット
成形後に部品の位置や方向を決定できるため、製品設計の選択肢が広がります。
しかし、後加工として金属部品の組み付けを行うため工数がかかります。
またインサート成形で部品の組み付けを行うよりも金属部品の接着強度が低いです。そのため、アウトサートが向いているものは「少量生産のもの」「修正が予想されるもの」となります。
注意点としては、組み付けを行う際に製品を固定するための治具の製作が必要となる場合があります。追加でコストや時間を要する可能性があるため、プロジェクトの計画において考慮する必要があります。
インサート部品で使用される素材
金属(鉄/ステンレス鋼(SUS)/真鍮/アルミニウムなど)
金属はインサート成形で最も一般的に使用される素材です。具体的にはナットやネジなどがあげられます。
磁性を持つインサート部品(例えば鉄やニッケル合金)の場合は、磁力を利用して金型に固定することができます。しかしステンレスや真鍮の場合は磁力を利用できないため、ネジやピンで固定するなど、固定方法を検討する必要があります。
樹脂
樹脂部品をインサート部品として、樹脂同士を組み合わせる場合もあります(インサート2色成形)。
耐熱性、耐薬品性、高い機械的強度を持つプラスチックや、強化繊維やフィラーを含む複合材料もインサートとして使用されます。
フィルム
薄いフィルムをインサート部品として一体で成形する方法もあります(フィルムインサート)。
フィルムには必要に応じて印刷、塗装、また他の装飾が施されることがあり、機能性やデザインの付与が可能になります。
車載用コントローラーパネルの表面の耐久性を向上させる用途や、印刷フィルムにより、光沢・艶消し・パターン・柄などの表面加飾としても活用されます。
その他の素材
その他にもインサート部品として用いられる素材はいくつかあります。
例えば、セラミックや木材、電子部品など、様々な素材のインサートが可能です。
インサート成形のメリット
インサート成形には下記のメリットがあります。
メリット① 工数削減
インサート成形の最大の特徴は、複数の部品が組み込まれた状態の製品を、一度の成形で生産できることでしょう。つまり、成形後の組立工程を削減することができます。そのため、大量生産の場合はトータルで考えると生産効率の向上になります。
メリット② 接着強度の向上
アウトサートでは樹脂を溶かして部品を埋め込むため、細かな凹凸まで樹脂が入らず、強度が不安定になりがちです。
それに対しインサートの場合は、部品の表面に溶融した樹脂がしっかりと流れ込み固化するため、インサート部品を強固に結合します。そのためインサート部品が外れるリスクが低いです。特に振動や衝撃が頻繁に発生する環境で使用される製品にとって、この特性は極めて重要です。
このように、アウトサートでの固定方法と比較しても、インサート成形の方が部品が外れにくく、製品に対する信頼性は非常に高いです。
メリット③ 精度の向上
インサート成形は、手作業で行うアウトサートと比較して、精度良く両部品を一体化させることが可能です。金型でしっかりインサート部品を固定することが出来れば、位置ズレのリスクが低くなります。
インサート成形のデメリット
一方で下記のデメリットもあります。
デメリット① 製品のリサイクルが難しい
インサート成形品は異なる素材のものが一体化しているため、リサイクルが難しくなるという問題があります。
例えば、プラスチック製品に金属部品のインサートが組み込まれている場合、異なる素材を分離しなくてはなりません。この作業が困難であり、また分離するための設備が必要となればその分コスト高になります。
現代において、このようなリサイクルに対する問題は大きなデメリットと言えます。
デメリット② 初期コストが高い
インサート成形ではインサート部品を配置する際、ロボットなどの専用設備が必要になることが多いです。
例えば、インサート部品を自動で供給するパーツフィーダーなどの専用設備を導入する必要がある場合、初期コストが大きく増加します。
生産数が少ない場合には、専用設備を使用しないことも可能ですが、その場合は有人(手作業)での対応になります。つまり人件費が成形費にプラスされるため、製品によってはアウトサートの方が安くなる場合もあります。そのため製品の生産数や用途などを考慮したうえで成形メーカーと相談し、適切な方法を選定することを推奨します。
しかし、初期コストのかかる専用設備の導入ですが、単に作業の自動化ができるだけではなく、ヒューマンエラーの防止や生産性・安全性を向上させるなどの複数の効果があります。
弊社関東製作所では、パーツフィーダーなどの専用設備・自動機の製作も行っております。幅広い用途の機械の提案実績があるため、お客様ごとのニーズに合わせた最適な仕様で提案いたします。
インサート成形に類似した方法『2色成形』
インサート成形とはあらかじめ金型内にインサート部品を配置し一体で成形する方法ですが、似たような方法として「2色成形」があります。
その中でも、「インサート2色成形」と「回転2色成形」が代表的です。どちらも異なる色や異なる種類の樹脂材料を組み合わせて一体成形する技術です。
インサート2色
インサート2色成形は、射出成形機と金型を2つずつ使用します。流れとしては、まず1つ目の射出成形機・1次型で、1色目を成形をします。その後、成形品を取り出し2次型にその成形品をインサートし、2つ目の射出成形機・2次型で成形します。
回転2色成形
それに対して回転2色成形とは、2つの射出ユニットを持つ特殊な射出成形機1台を使用します。
金型は、下図のようにコア側が1型、キャビ側が2型で構成されます。
成形の流れとしては、最初に1つ目の樹脂材料で製品の一部を成形します。その後、コア側の金型を回転させて、2つ目の樹脂材料で製品の残りの部分を成形します。
2色成形のメリット・デメリット
2色成形は樹脂材同士を一体化して成形ができるのが特徴です。「回転2色」と「インサート2色」は似ており目的自体は同じですが、「回転2色」では特殊な成形機を用いる事で1サイクルで行えるのが特徴です。
「インサート2色」では通常の成形機で成形可能ですが、1次型で成形し離型した部品を2次型にインサートして成形するので2サイクル必要です。
回転2色成形はサイクルタイムや工数削減に繋がりますが、専用の成形機を保有しているメーカーでないと対応が出来ません。
まとめ
以上のように『インサート成形』とは、樹脂と金属や他素材の部品とを一体化させた製品として、金型で成形する技術です。特に、精度や強度の必要な製品や大量生産の製品はインサート成形に向いていると言えます。
一方で少量生産の製品についてはアウトサートなどで初期投資を抑えるなどの方法が適切でしょう。
どの工法を選択するかは、製品の形状や部品の種類、生産数などを考慮して決定する必要があります。弊社関東製作所は、これらの技術に関する深い知識と豊富な経験があり、お客様のニーズに合わせたご提案も可能です。インサート成形品などのプラスチック製品に関することでお困りごとがあれば、ぜひ弊社までお問い合わせください。
[関連記事]
> 射出成形における「成形条件」とは?成形条件の項目や不具合発生時の対処法を学ぶ
> コスト削減に直結!射出成形におけるサイクルタイムとは?成形工程を知り、削減ポイントを見出す
> 射出成形の基礎からコスト・納期対策への専門知識まで 射出成形をトータルに学ぶ