プラスチック製品の量産を見越した“試作工法”を検討する【射出成形試作品プロジェクト#02】
プラスチック
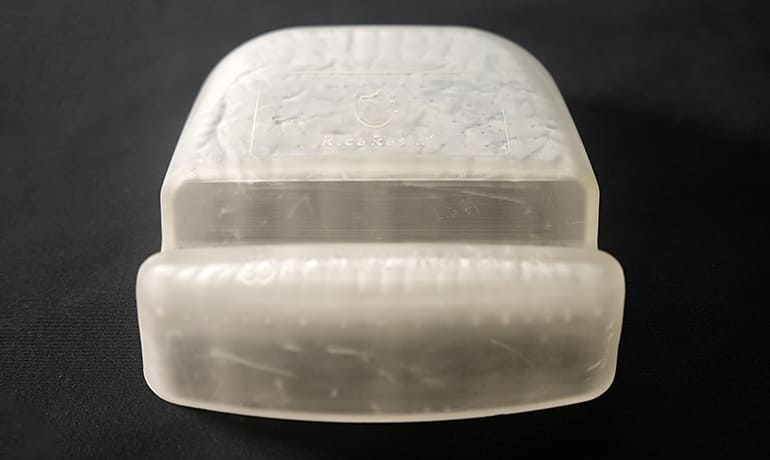
プラスチック製品の開発をご検討のメーカー様、また製造の工程で課題や難解な問題に行き詰っている開発者の方。【射出成形試作品プロジェクト】第二回目となる本記事では、プラスチック製品の『試作』についてご紹介いたします。
製品の量産プロジェクトにおいて、まずは数個の試作品で仕上りの確認をすることは重要ですね。試作品を製作する工法は様々あり、その『試作目的』次第でセレクトすべき工法も違ってきます。
本記事が、貴社の製品開発プロジェクトの手助けになれば幸いです。
【射出成形ラボの簡易金型サービスはこちらより】
> 最短納期を2週間で!180ton射出成形機用の簡易金型を、60万からご提供いたします。
目次
スマホスタンドの試作目的とは?
今回のスマホスタンドを試作した目的は、形状確認と外観確認です。
スマホスタンドとしてスマホがきちんと立つか?(製品に対する要求性能が成立するかどうか?)を確認するために試作を行いました。そのため、数量は最低1個あればよく、試作後の量産は金型を使用した量産を予定。
また、試作の工法として3Dプリンターによる光造形を選びました。
試作数量が少ない場合、試作の工法は切削か3Dプリンターが適しています。
今回のスマホスタンドは肉抜きされており、形状的に切削では削り量が多くなってコストがかさんでしまいます。また、ロゴ部分を細かく再現するには3Dプリンターの光造形方式が適している点から、この工法を選びました。
今回の試作目的だった「形状確認」と「外観確認」の結果は、概ね問題ありませんでした。
ロゴの形状も細部まで表現できており、また広めに彫り込んだスマホの差し込み口も、スマホカバーが無い状態でもしっかり立てられることが確認できました。
プラスチック製品の試作を依頼する際のポイント
試作の目的を決める必要性
試作の目的には、大きく分けると外観確認と機能確認があります。
外観確認
外観確認では、製品の出来上がりの形さえ見られればいいので、工法の自由度が高くなります。ただし、磨きや塗装が必要な場合には、注意が必要です。
例えば、切削であれば切削痕、3Dプリンターであれば積層痕など、成形・造形する際にできる跡があります。それらの跡を仕上げ加工するかについてや、色や質感が見たいのであれば、塗装や本番材料での試作が必要か等も事前に決めておかなければなりません。
機能確認
機能確認では、破壊試験、強度試験、耐摩耗試験、薬液試験など、試験の条件によって大きく異なります。量産の製品と同一材料の試作を必要とする場合が多く、工法は限られます。
複雑形状の場合は張り合わせるのではなく、一体で作る必要があるか等も関係してきます。
試作で金型を使用しない工法の場合、大型の製品や複雑形状の製品は、複数のパーツに分けて貼り合せをしないと製作できない事があります。当然、貼り合せ箇所は一体成形した場合に比べ弱くなりますので、機能確認の条件によっては一体で製作する必要がありますので、事前確認が必要です。
試作目的に従い、必要数量を決めよう
試作で必要な個数はいくつでしょうか?
外観確認には数個あれば問題ないでしょう。それに対して破壊試験などを行う機能確認では、数百~1,000個も必要とする場合があります。
試作の必要数量が多い場合、例えば数百~1,000個ぐらいなら、金型を作って製作した方がメリットを得られることが多いです。
要注意!試作と量産で工法が異なる際のポイント
量産案件の場合、大抵は最終的に金型を使用して量産成形を行います。試作と量産で工法が異なる際には、特に注意が必要です。試作品の形状がそのまま金型で成形できない場合があるからです。
試作を行う際にはあらかじめ量産工法の選定までしてから、製品形状を吟味し、試作を行う事をお勧め致します。
プラスチック製品の主な試作工法を知ろう
プラスチック製品における主な試作工法は4つあります。
【試作工法①】切削加工
切削加工は、樹脂の板やブロックを削って形を成形する工法です。材料の種類が豊富で、数量の少ない試作ではコストメリットが高くなります。
機械の刃物で削るので、大型製品や複雑形状の製品を作る際、別々のパーツで加工を進め、後で貼り合せるという場合もあります。
また、深さのある物も材料の規格サイズの関係で貼り合せになる可能性が高いです。
【試作工法②】3Dプリンター
3Dプリンターには、FDM方式や光造形、インクジェットなどの方法がありますが、どれも樹脂材を重ねて造形する工法です。近年、材料となる樹脂の種類はかなり増えてきましたが、いまだに対応できない材料もあります。
メリットとしては形状の自由度が高く、例えばラティス構造といった切削や金型では不可能な形状も造形することができます。
デメリットとしては、特に3Dプリンターの中でも最もポピュラーなFDM方式では、上から樹脂を溶かして重ねるため、形状によっては他の成形方法に比べて強度が出ない場合があります。たとえ同じ形を作ったとしても、射出成形品ほどの強度は期待できないでしょう。
そのため、FDM方式の3Dプリンターでの試作は強度試験には向きません。
前述の通り、FDM方式以外にも光造形やインクジェット、SLS方式といった3Dプリンターの中でも様々な造形方式があり、それによって使用できる材料や、強度、コストも異なるので、注意が必要です。
メーカーで3Dプリンターを保有していても、どの方式で、どんな樹脂が使えるかは必ず事前に確認しておきましょう。
3Dプリンターの規格によっては1m~2m規模の大きな製品も作ることができますが、費用が高額です。高さの低い製品の方が安い傾向にあり、小物関係を作るにはコストメリットが高くなります。
【試作工法③】真空注型
真空注型は、シリコンの型で成形する工法です。20~100個程度の数量の試作では、金型を製作するよりも安く済み、コストメリットがあります。
材料はライク材の為、量産を金型で行う場合には、量産と同じ材料で作ることはできません。また、成形費の他にシリコンの型費が必要となります。
真空注型工法の工程
まずは3Dプリンター等でマスターサンプルと呼ばれる、復元の元となる立体サンプルを作りシリコンゴムで覆います。シリコンが完全に凝固したら半分に割り、マスターサンプルを取り除きます。
再びシリコンゴムの型をきれいに復元し固定します。そして型内に樹脂を流し込み、真空引きにより形状の細部まで樹脂が流れ込んでいきます。
樹脂が固まったらシリコンゴム型を割ることで、成形品を取り出します。
【試作工法④】簡易金型
簡易金型とは、安い鋼材(アルミ等の加工しやすい材料)で金型を作る工法です。形状もなるべく簡略化して製作します。
基本的には量産時と同じ樹脂材料を使うことができ、量産品と同等品の製作が可能です。数百~1,000個ぐらいを成形する必要があれば、コストメリットが出る場合が多くなります。
デメリットとしては、簡易とはいえ金型を製作するので、そのぶん他の試作工法よりも高額となります。
【射出成形ラボの簡易金型サービスはこちらより】
> 最短納期を2週間で!180ton射出成形機用の簡易金型を、60万からご提供いたします。
まとめ
以上、射出成形における試作について弊社のロゴ入りスマホスタンドを参考に、試作の目的と工法をご紹介いたしました。
まず試作の目的を決め、そして試作数量や量産工法を決めることにより、最適な工法を選ぶことができます。業界的に試作メーカー、金型メーカー、量産メーカーと分かれている事が多いですが、関東製作所は金型の設計・製作をメイン事業としながら、試作対応、量産対応まで行えるメーカーです。
試作段階から最終的な量産まで見越した提案が可能ですので、プラスチック製品の試作でお困りのお客様は、是非ご相談ください。
ノウハウを駆使し、よりコストメリットの高い試作をお手伝いいたします。
> プラスチック製品の美しい形状と機能性を設計【射出成形試作品プロジェクト#01】
[射出成形ソリューションサイト]
> 小ロット・試作金型製作・コストダウン提案の【射出成形ラボ】サイト