ブロー成形の成形不良『薄肉』を未然に防止 金型におけるPL(パーティングライン)設定のポイントとは?
金型
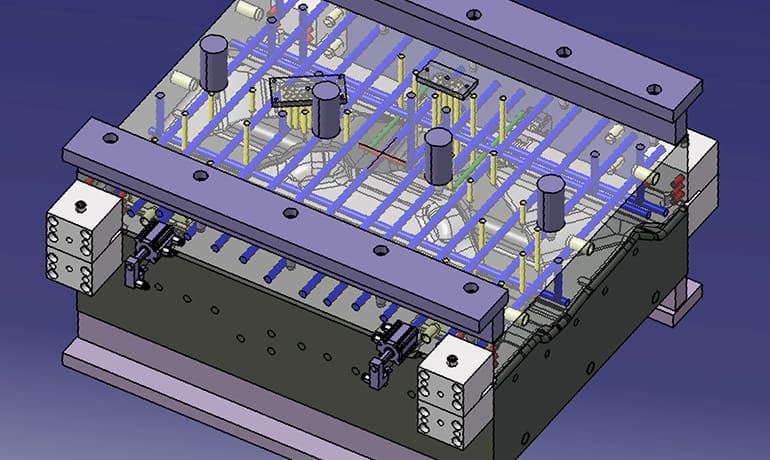
こんにちは、株式会社関東製作所の丸山です。
私たち株式会社関東製作所は、長年ブロー成形金型の製造に携わって参りました。特に、自動車の内外装、機能部品から医療機器、住設などさまざまな分野にて実績があります。
そこで今回は、ブロー成形金型を設計する上で、PL(パーティングライン)の重要性に関してお話をしたいと思います。
特に、ブロー製品(中身が中空のプラスチック製品)の開発者の方・設計者の方、ぜひ参考にご活用いただければ幸いです。
目次
製品の品質を左右する、ブロー成形金型のPLとは
ご存知の方もいらっしゃると思いますが、ブロー金型は左右2つに分かれた金型で構成されます。
ブロー型の成形機から出てきたパリソンと呼ばれる樹脂をその2つの金型で挟み、針を刺し、そこから空気を入れ、型内で膨らませることで意図した形状に成形されるという仕組みです。
> ブロー成形金型の特徴とは? ブロー成形を製作する上でのメリット・デメリットを知ろう
そのため金型には、左右2つの形状がぴったり合うための『合わせ目』があります。この合わせ目のことをPL(パーティングライン)と呼びます。
ブロー成形品の良し悪しは、その製品形状に依存することは当然なのですが、このPLを製品形状の『どこに設定するか?』で製品の品質が大きく左右されます。むしろPLの設定がブロー金型設計の醍醐味といっても過言ではありません。
それでは、そのPLを設定する上での注意点を詳しく見ていきましょう。
ブロー成形金型のPLを設定する際の注意点
【注意点1】ブロー成形品が『薄肉』になりがちなケースとその対策
PLを設定した際、製品形状において『幅:1』に対し『深さ:1』以上ある部分に関しては要注意です。
そういったケースに、成形後の樹脂の厚みが、非常に『薄肉』になる現象が、よく起きがちです。
上記のようなフランジ付きの形状は、PLが必ずフランジの外周を通るので、断面A-Aを見ていただくと『幅1に対して深さ1』になっています。
この深さがこれ以上深くなると成形条件がさらに悪くなり薄肉になる可能性が高くなります。
以下、図で説明いたします。
↑赤丸のPL間のパリソンの断面の面積は200mm²
↑PL部は相手方の金型に挟まれパリソンは固定されるので、赤丸のPL間の樹脂はのばされていく
↑最終的にパリソンの肉厚は3分の1になる
(わかりやすいよう2Dでの考え方・計算でご説明をいたします)
上記の例では、肉厚2mmのパリソンが100mm幅のPL(赤丸)で挟まれます。
PL間(赤丸ポイント間)のパリソンの断面積は 2mm × 100mm で 200mm²
それに対し、PL間の金型断面の全長は、100mm + 100mm + 100mm で 300mm
金型が閉じることでPL部分のパリソンは固定されます。その状態でブローされるので、パリソンは金型に密着するまで、のばされ続けます。
要するに、PL間のパリソン面積(約100mm×2mm=200mm²)は変わらないのに、全長が300mmある面に、無理矢理ブローされ、のばされ続けることで、成形後の肉厚は
200mm² ÷ 300mm で 0.67mm
となります。
つまり『幅:1』に対して『深さ:1』の形状は、成形すると、成形品の肉厚が3分の1程度の薄さになる可能性が高いと言えます。
そのため、PLが必ずフランジの外周を通ってしまう製品で、PLで割った後の形状が『幅:1』に対して『深さ:1』以上になってしまう場合は、製品形状の見直しを推奨いたします。
フランジ形状が無い場合に推奨したいPL設定方法
上のケースではフランジ形状がPLの位置を拘束しましたが、フランジ形状がない場合は対角にPLを設定します。
↑形状に対し対角上にPLを設定します
上記はフランジがない場合に推奨したいPL位置になります。
対角αの距離は200の二乗に100の二乗を足したものの平方根になります。
新PL間の距離は 223.6mm
新PL間の樹脂の面積は 2mm × 223.6mm = 447.2mm²
『A-B-C』の全長距離は 100 + 200 = 300mm
成形後、『A-B-C』の肉厚は 447.2mm² ÷ 300mm = 1.49mm
2mmの肉厚に対し、約75%の肉厚になります。
先ほどの、『幅1に対し深さ1』のケースでは、肉厚が3分の1にまで薄くなりましたが、対角にPLをセッティングすることによってこれほどまでの差が出ます。
いかにPLの設定位置がブロー製品の品質に影響をあたえるのかご理解いただけたかと思います。
【注意点2】鋭角なPLは、丸みをつけることで樹脂破れなどを防ぐ
上記はL字に曲がったエアコンダクトでよくある例ですが、
面①は上に向かって内側に狭くなる勾配面なのでPLは下部
面②は上に向かって外に広がる勾配面なのでPLは上部
になります。
この高低差のあるPLをどこかで繋げないとならないのですが、上記の場合、L字に曲がる箇所がそれにあたります。
3D―CADソフトが計算した結果では(※)、直角に近い形でPLが折れています。ひどいものになるとZ型になる場合もあります。
※株式会社関東製作所がメインで使用しているCATIAというソフトでは、自動でPL位置を算出してくれる機能が備わっています。
鋭角なPLは上記のように型締めの際にパリソンを破いてしまう恐れがあり、さらに成形時に製品面に皺などの成形不良を起こすリスクが高まります。
このような場合は、極力PLに『丸み』をつける必要があります。
この例では縦の直線がなくなるまでのR(カーブ)にしていますが、大きなRをつけるほどアンダー量が増えるので、Rの大きさは形状によって変える必要が出てきます。
金型を切削加工機で削る際に、①3軸加工にて『できなり』で加工処理するのか? または、②製品形状自体をアンダーが無いように形状変更するか? それとも、③アンダーを忠実に再現して金型を作るのか? は、都度、関係者間にて協議の上決める必要があるでしょう。
まとめ
いろいろ制約や推奨項目があるブロー成形ですが、スポイラーやバンパー、エアコンダクト、洗剤容器などを目にされたときは、PL(パーティングライン)がどのように設定されているか、ぜひ観察されてみてはいかがでしょうか。
なぜPLがそのそうな位置に設定されているのかには、必ず理由が存在します。
今回取り上げたPLに関する2点の注意事項は、ブロー成形金型を設計する上で、基本的かつとても重要なポイントです。
もしこの2点を知らず、金型設計、金型製造、成形トライを進めた場合、無駄に設変や製品形状の再検討が必要になる可能性が出てきてしまいます。
ブロー成形品というプラスチック製品の特長、そしてそれを生産する金型の構造を熟知した上で製品設計することが、後の製造工程を円滑に進める大きなポイントとなるでしょう。
株式会社関東製作所は、ブロー成形金型の製造には、半世紀以上携わっております。
そのため、ブロー金型設計のベテランは多く所属しており、上記以外の視点からも多角的に支援、アドバイスが可能です。
ブロー成形品の開発者様、設計者様、ご検討の製品がございましたら、是非お気軽に関東製作所までご連絡ください。