プロダクト製品の開発・設計初心者向け 製品開発の定石手順、全8ステップ
プラスチック
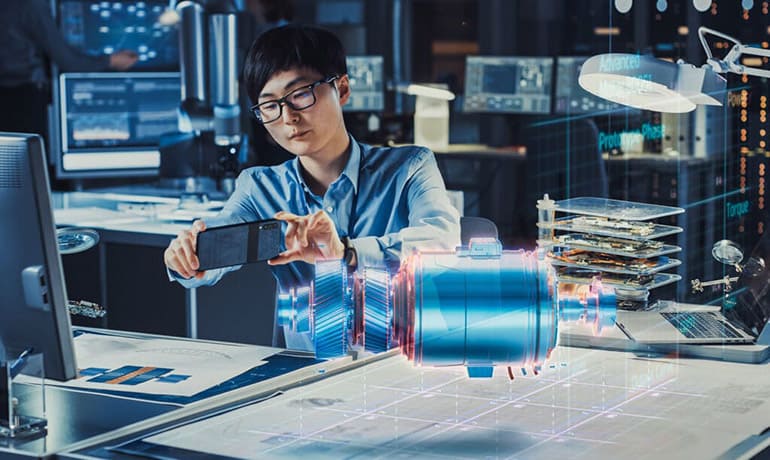
製品開発者は新たな製品を開発するあたり、様々な要素を検討しないといけません。
製品機能、形状構成、メカ構成など、理想の性能と形状を実現する為に試行錯誤を繰り返し、様々な苦難を乗り越え、ようやく理想の製品として日の目を見ます。
何もないところからプロダクト製品を開発するとなると、どこから手を付ければいいのか…。
特に設計経験の少ない方には、荷が重い作業ですね。
しかし、どんな製品を開発するにも相応の手順があり、それらを一つ一つクリアすることで、世の中から評価される製品が生まれます。
急いで必要な工程を軽視し製品開発を進めても、後々大きな修正が必要になり、無駄な工数やコストが発生してしまいます。
今回は、開発・設計が初心者の方でも理解いただけるよう、プロダクト製品開発の進め方をご説明いたします。
目次
製品開発の手順
Step① 製品の機能を考える
製品開発を行ううえで根幹となるのは、「どんなユーザーが、どのような用途で使用する製品か」を検討することです。「当たり前の事だろ!」と感じたと思いますが、この用途イメージがすべての工程で、一貫して明確である必要があります。
例えば試作段階にて、計画していた形状では上手く具現化できず、それを理由に形状変更をした為、本来の機能が損なわれた製品になってしまうことも…。
製品化実現に向けて、取捨選択を余儀なくされた場合、その製品の機能が明確であれば、何を優先すべきかの判断ができます。
Step② 製品の構造を考える
次に製品機能を実現できるメカ構成を考えます。
製品機能で考えた製品(部品)が単体で機能するものか?それとも、他の部品(機構)との連携で機能するものか?で、形状のX,Y,Zの構造が変わってきます。
単体で製品を検討する際は、機能を付加しすぎると形状が複雑になり、製品として実現させるには無理が生じる可能性も出てくるので、出来るだけ単純に考えまた方が良いです。
しかし、どうしても複雑になってしまう場合は、製品をいくつかの部品に分割して構成する方が、トータルで有利な場合もありますので考慮に入れるべきです。
Step③ 製品の形状を考える
最終的に「形状の構成」を考えます。ただし、デザインが優先される製品もあります。
製品機能を主軸に考えつつ、「構造」と「形状構成」のバランスを考えて、形状を作っていきます。
ここで重要なのが、金属製or樹脂製に限らず、形状次第でその後の工法が大きく変わってきます。例えば金属加工では、構造の一体化に限度有るので、何部品かの組合せや溶接等の後加工が必要となります。
射出金型による樹脂成形は、溶けた樹脂がゲートと言われる注入口から、金型内の形状化された隙間に高圧で入っていくので、肉厚の厚薄・大きさまで、比較的自由に再現できるでしょう。
真空成形は金型が安価なのがメリットではありますが、逆に成形上、複雑な形状を再現できません。
ブロー成形は主に、製品が中空な形状に適した製法です。
以上のように、形状を再現するのに適切な工法は数多くあります。
先ずは希望する形状を成形業者と相談し、金属では困難な場合は、どの成形に最適な形状かを検証していく事が大切です。
ここまでで、製品の大枠のイメージができます。
簡単な形状・機能であれば、この段階でイメージしたものがそのまま製品化できるかもしれませんが、製品を完成させるには、まだまだ決定事項があります。
素材の選定
Step④ 素材を考える
「製品機能」「メカ構成」「形状構成」が決まれば、次に製品の「素材」を考えていきます。
代表的な素材の分類では、「金属」「樹脂」「陶器」の3つがあります。
金属
[メリット]
・強度が高い
他の2素材と比較すると強度が高い為、強度が必要な製品に適している。また、熱処理を行うとさらに強度や靭性を持たせる事ができる。
・耐熱性、耐摩耗性が高い
鉄で約1,200度、ステンレスで1,400度と融点が高い
・導電性、熱伝導性が高い
・単純な形状の場合、金型費用を軽減できる(曲げ型、穴ポンチ型程度のため)
[デメリット]
・重い
強度があるので薄くできるが、鉄は樹脂の約6倍の重量。
・腐食しやすい
ステンレスなども条件次第で腐食する
・デザイン性に欠ける
製品形状が直線的なものに限定され、厚肉は基本的に均一となる
・追加費用がかかりやすい
外観部品だと表面処理(防錆等)、色塗装の後処理、複雑形状の場合、部品間の溶接など、後処理が出てくる
樹脂(プラスチック)
[メリット]
・軽い
・加工性に優れている
複雑な形状でも量産が可能
・絶縁性、遮断性が高い
電気や熱、水、ガスなどの物質を通さない
・表面処理が不要
・色も樹脂色で成形可能
・樹脂種類も豊富で選択幅も広い
[デメリット]
・耐熱性が低い
・紫外線に弱い
屋外では劣化する
・金型が必要
複雑な形状だと金型機構も複雑になり費用は高価になる
また内面導電性、超絶縁性等、付加が必要な場合は塗装処理が必須
陶器
[メリット]
・キズが付きにくい
・保温性がある
・絶縁性、防炎性が高い
[デメリット]
・強い衝撃に弱い
・重い
金属よりは軽いが、強度が低い分、厚みが必要
・形状的な制約は単純形状に限定
大まかな分類での特性を記載したが、各素材の中でも細かく種類があり特性が違うので、注意が必要です。
生産の手順
Step⑤量産数と販売価格の設定
ここまで決まってくると、いよいよ製品を作る工程に入ります。だた、その前に量産にあたり、どのぐらいの数を生産し、どのぐらいの価格で販売するのか、考えましょう。
素材や形状、生産数量などが決まっていれば、「製造方法」の選定ができます。そこまで情報が揃えばおおよそのコストの算出が可能です。
ただし、販売価格に見合うコストで生産ができないのであれば、この企画は見直しが必要になるでしょう。
それぞれの製品マテリアルによる製品形状、スペックがある程度固まった後に、予算算出での製法判断に移行します。
それぞれの専門業者に見積もり依頼を行い、価格精査に入ります。(この時点では、各業者には専用マテリアル図面でなくても、製品意図を明確に伝達すればOKです。また業者からもアドバイスを受けて算出依頼します)。
製法の選択は、各社に依ってそれぞれの考え方があると思いますが、単純にデザイン重視か機能重視かで違ってきます。
また、生涯製品企画数を型費(初期費用)で割り、型費用製品単価の優位性で判断するのもありです。
必ずしも価格のみの優劣判断とは限らず、開発企画者の想い、製品価格全体での開発費用(準備設備費)をどれだけ充てるかにもよります。
Step⑥図面の作成
実際に、製品を具現化するにあたり、まずは製品図面の作成が必要です。2D図面で製品寸法などを入れて、どんな製品を作りたいのか、具体化します。
可能であれば3D図面も作成すると、よりスムーズに製作に入る事ができます。
図面化は、どの製法かの前に、設計者の希望形状があるものです。
製法がほぼ決まった時に、各製法にて適正形状、金型の抜き方向、スライドコマの要否等を各専門業者と協議行い、ある程度決めこんで作成していきます。
3Dデータを提示できれば、委託業者も検証が簡易に出来るのでスムーズに進むでしょう。
Step⑦試作品を作る
素材によって様々な製法が存在する為、ここでは素材に「樹脂(プラスチック)」を選択した場合の手順を紹介します。
図面や素材、生産数量が決まれば、いよいよ試作を行います。
プラスチック製品の場合、量産を行う為には金型を作るのが通常ですが、いきなり試作段階で金型を作ると、もし成形品に問題があった場合、修正費などコストが高く、場合によっては作り直しといった事が起こりえます。
金型の製作費用は、数十万円から、機構・サイズによっては数千万円かかります。
そのため、「この形状で問題ない」といえるところまでは、金型以外の製作方法を採るのがベターです。
試作にも目的を持って行いましょう。形状の確認、強度の確認、耐薬性の確認など、どんな事を試すための試作かを決めます。
下記に主な試作方法を記載しますが、試作にも様々な方法があり、工法によっては、試作の目的をクリアできない場合がありますので、注意が必要です。
試作の方法[1] 切削加工
樹脂板や樹脂ブロックを切削で加工して形状を作る
[メリット]
・安価でできる
・すぐにできる
[デメリット]
・素材が限られる
・あまりにも細かい形状や小さいものは加工できない
試作の方法[2] 真空注型
シリコンで型を作って樹脂を流し込み成形する
[メリット]
・安価でできる
・20個程度はその型で作れる
[デメリット]
・シリコンは柔らかいので寸法精度が悪い
・耐水性がない素材
試作の方法[3] 簡易金型
アルミなどの柔らかい金属で金型を作る
[メリット]
・金型と同等の寸法精度
・1,000個程度は量産できる
[デメリット]
・金型ほどではないがコストが高い
3Dプリンター
FDM、インクジェット、光造形などのプリンターを使用する
[メリット]
・精度がよい
・安価
・形状対するに制約がほぼない
[デメリット]
・大きいものは造形できない(もしくはコストが高い)が、発泡体切削法で形状確認は可能
・素材に制限がある(近年、素材は増えているが、造形方法によっては制限がある)
それぞれにメリット・デメリットがあるので、前述のとおり、どんな目的で試作をするのかを考えて、パートナーとなる製造メーカーに相談する事が大切です。
また、あくまで試作は量産を視野に入れて進めなくてはなりません。
特に3Dプリンターは、複雑な形状でも生成可能です。
しかし量産時の金型作成において、試作時と同じ形状が実現できるかは別問題です。
3Dプリンターでの生成方法とは大きく違い、金型で製品を生成するにあたり、気をつけなければいけない要素は多々あるのです。
そのため、金型での量産を視野に入れた製造メーカーとのパートナーシップが非常に重要になってきます。
製品の条件次第ですが、量産数が少ないものは、上記で紹介した試作の工法で本番製品を作るのもいい方法です。
大量に製品を作るのであれば、金型を作って量産するほうが、製品単価が下がります。
そのため、世の中のプロダクト製品は、基本的に金型を作って量産を行うケースが多いのです。
Step⑧製品の量産
試作が終われば、試作品の評価・検証を行い、問題がなければ量産に向かって準備を進めます。
量産に適した金型による成形方法にも多種類あるので、下記に紹介します。
射出成形
世の中の大半は、射出成形という方法で成形されています。金型内(雄型、雌型)に形状を彫り込み、その隙間に樹脂を高圧で注入する方法。
[メリット]
・複雑な形状でも金型構造の工夫で構成対応可能
・樹脂の種類も豊富
[デメリット]
・金型費用が比較的高価
ブロー成形
容器ボトル、タンク、ダクト類を成形するのに適した方法。
金型内(雄型、雌型)に形状を彫り込み、円筒状の樹脂を金型で挟み、金型の外から空気針を差し込み、圧縮空気を注入して、中空の成形品を作る方法です。
[メリット]
・中空構造、大型成形品に適している
・金型費用が比較的安価
[デメリット]
・形状的な制約がある
・使用樹脂に制約がある
真空成形
金型(雄型もしくは雌型)に形状を彫り込み、板状の樹脂と金型の間を真空状態にして樹脂を型に押し当てて成形する方法です。
[メリット]
・金型費用が比較的安価
[デメリット]
・量産性がない
・形状的な制約がある
・使用樹脂に制約がある
量産と言っても一品物は別として数十個、数百個、数千個、数万個と各社、各業者、その製品特性で変わってきますが、樹脂成形品は量が多いほど安価にできます。
例として製品形状による製法選択、金型の取り数増による1ショット成形での成形費割り、製品設計の肉盗みでの軽量化での樹脂量軽減等・・トータル予算での判断になります。
成形後、追加で加工を余儀なくされる場合もございます。
ブロー成形では特に、成形時にできるバリを取ったり、製品同士のジョイント部分に穴を開けるため、成形された製品の一部を切断したりなど。
今までは、成形後に人の手でそういった後加工を行うのが主流でした。
しかしそこには、人が行うことによるヒューマンエラーの発生や、刃物を使うことの危険性などがあります。また現在の日本国内では、少子化による労働者の減少が現実のものとなってきています。
そのため、安全で安定した品質かつ省人化の為に、近年では加工機や協働ロボットの導入も増えております。切断、バリ取り、穴あけ、溶着などの加工はもちろん、高性能カメラを使用した検査なども担わせることが可能です。
必要に応じて、そういった加工機・協働ロボットの導入も、あらかじめ計画しておきましょう。
まとめ
今回はプロダクト製品開発の概略を流れに沿ってご説明しましたが、新しい製品を開発するのは相当な苦労がかかります。一つの問題を解決すればまた別の問題が出ての繰り返しで、形になるまでに何年もかかる場合が多いです。
特に樹脂は70種類近い素材があり、成形方法による特徴も多いので、経験者であっても開発に苦労される事だと思います。
当社、関東製作所は長年の成形経験則、各方面でのモノづくり経験豊富な技術スタッフを有しており「プラスチック製品開発のベストパートナー」を自負しております。
皆様の製品開発の最初の一歩からのパートナーとしてお役に立てるよう体制を整えておりますので、製品の企画段階から是非、ご相談頂ければと思います。
射出成形ソリューションサイト
> 小ロット・試作金型製作・コストダウン提案の【射出成形ラボ】サイト