部品加工の品質維持とコストダウンへの設計変更|国内製造転換の成功事例をご紹介
金属・部品加工
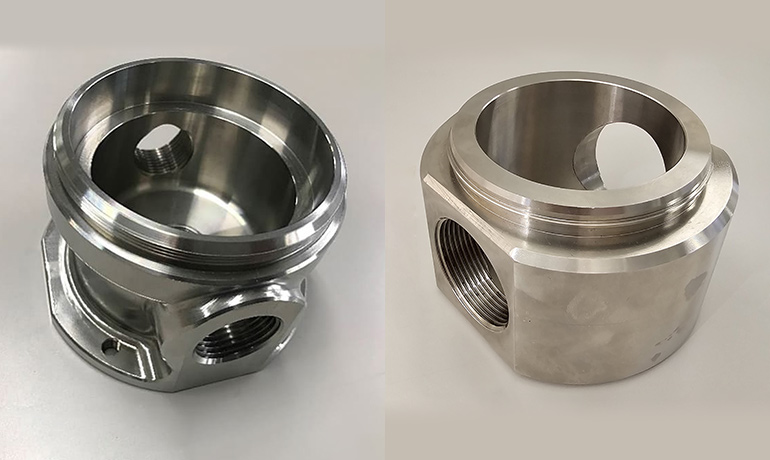
今回ご紹介する事例は、下記リンク先の「サプライチェーンの国内回帰のメリット」にて取り上げた、部品加工案件です。
部品加工発注において、中国製作から日本製作へ変更されることにより、距離的なアドバンテージを得たお話は先の記事にてお話し済みです。今回はコストの面で目標価格に近づける、いわゆるVA提案によるコストカット事例として詳しくご紹介いたします。
> サプライチェーンの国内回帰のメリットを考える|部品加工現場でのQCDを再検証
目次
品質を保ちながらの形状変更によるコストカット
金属の部品加工に対するコストカット。これには一概に「形状の変更」に切り込む必要が出てきます。もちろん、既存の製品の品質は維持しなければなりませんので、製品の機能や特性等を理解した上での提案が必要となります。
手順としてはこうです。
- お客様側で、最初にお考えの内容をそのまま設計・作図して頂く
- その後、その必要・十分条件を反映して、部品としての機能、コストの整合性をとる
- VAとは
- Value Analysisは価値分析と呼ばれ、既存の製品の品質を維持したままコストダウンを行う提案
部品加工のコストカットに成功した製品事例
お客様から頂いた、最初の設計が下図①となります。
検討段階ではありましたが、最低限守らなければならない「製品の内径寸法」や相手部品との位置関係を設計されたものでした。
これをこの加工部品の用途、お客様側の設計の意図を遵守しつつ、加工における製造要件と形状の簡素化を図り再検討した結果、下図②を経て、下図③のような形状に着地しました。
最初の設計段階(図①)での最大の高コスト要因は、肉抜き形状でした。
「肉を抜く」箇所は、切削工程が発生すると同時に、その個所が外観部分となっている為、精度よく仕上げる必要があります。つまり、品質を担保する為に多くの工数が必要となり、当然コスト増へと影響します。
さすがに我々側が提案するどんな形状・要望も承諾していただけるとは思っていません。設計要件を担保しつつ、有効な提案を行っていく。それには、お客様との会話を重ねる事が非常に大切だと改めて痛感した次第です。もちろんお客様にも、多大なご協力を頂いて得られた結果と考えています。
コストカット前後での加工工程の比較
具体的な加工工程を以下に示します。
対象部品に対する「設計変更前」と「設計変更後」を比較していただければ、加工工数の削減がなされている様子を実感頂けると思います。
なお、こちらは下記リンク先の記事ページでも「5軸加工機への変更メリット」として紹介しております。
> 5軸加工機による加工費コストダウンの実情とは? 実際の加工部品で『加工工程』と『コスト』を検証
コストカット前の加工工程と形状のポイント
コストカット前の加工工程
工程① | 旋盤加工(外径+内径) | 旋盤を使用して最外径と内径の加工を進めていきます |
---|---|---|
工程② | 3軸加工(側面)前+後 | 従来まで申し上げている肉抜き部の加工をマシニングでおこなっていきます。 この場合、製品の全周にわたって肉抜き形状がありますので前と後(表と裏)の2工程で切削していきます。 |
工程③ | 3軸加工(横穴) | マシニングで穴とその座面を切削していきますこちらも前と後(表と裏)の2工程となります。 |
工程④ | 3軸加工(下面穴) | マシニングで下部の穴を加工していきます。 |
コストカット前の形状のポイント
まず問題なのが、軽量化をはかるための側面の肉抜きの形状です。
最初の旋盤加工後に、NCマシニングでの切削加工での形状出しが必要となり、ここに一定の工数が必要となってきます。
加えて、相手物とのRの合わせが難しく、また外観に出てくる個所でもあるので、仕上げの丁寧さが必要になります。つまり、細い刃物で時間をかけて切削するとういう工程です。当然それらには、コストは加算されます。
コストカット後の加工工程と形状のポイント
コストカット後の加工工程
工程① | 旋盤加工(外径+内径) | 旋盤を使用して最外径と内径の加工を進めていきます。 |
---|---|---|
工程② | 3軸加工(下面穴) | マシニングで下部の穴を加工していきます。 |
工程③ | 3軸加工(横穴) | 座面を設ける事によって締結面確保。 |
コストカット後の形状のポイント
設計変更前(図①)の肉抜き問題を回避するために、外径を大きくし旋盤加工のみで済む形状としました。ただ、図に示したように相手物との締結面が確保できなくなってしまう点、また、部品自体が重くなってしまう点が問題です。
そうして上記の2つの点を解決するための対策として、側面に座面を設ける事によって締結面を確保し、またR形状を削ることで肉抜きの役目を果たし、軽量化を実現しました。
締結面は旋盤とは別にNCマシニングでの切削加工が必要となりますが、図①と比較して各段に作業工数が削減されコストダウンにつながっています。
最終的には大幅な形状変更を施しましたが、部品の用途やお客様側の設計上の要求も確保することで、コストパフォーマンスの高い改修提案が実現しました。
もちろん量産する事は決まっていましたので、量産時にトラブルにならないよう試作品にて部品同士を合わせて検討した事は言うまでもありません。そして、全く問題も起こらず、量産へと送り出すことが出来ました。
まとめ
上記内容は主な変更のご紹介ですが、他にもすり合わせして形状変更の結果コストダウンにつながり量産対応させて頂いている案件も多くあります。
どのような製品にも、内容の大小にかかわらず、設計検討の余地はあると思います。我々(株)関東製作所は金型、金属加工に60年以上の経験と実績でその余地を見出し、大小を見極め効果的なVAに導いてきました。
昨今の海外生産の中、多かれ少なかれ様々な問題がある事はもちろん承知しています。海外生産がもちろん悪いとはいいませんが、現状のサプライチェーンに変更の余地があれば是非当社にて検討させて下さい。当社にて多角的な上効果的なVAの提案をお話させて頂く事が出来ると考えております。
[関連記事]
> サプライチェーンの国内回帰のメリットを考える|部品加工現場でのQCDを再検証