アルミ部品を射出成形で『プラスチック+メッキ』に工法転換! 東北新幹線ヘッドライトカバー開発秘話
射出成形
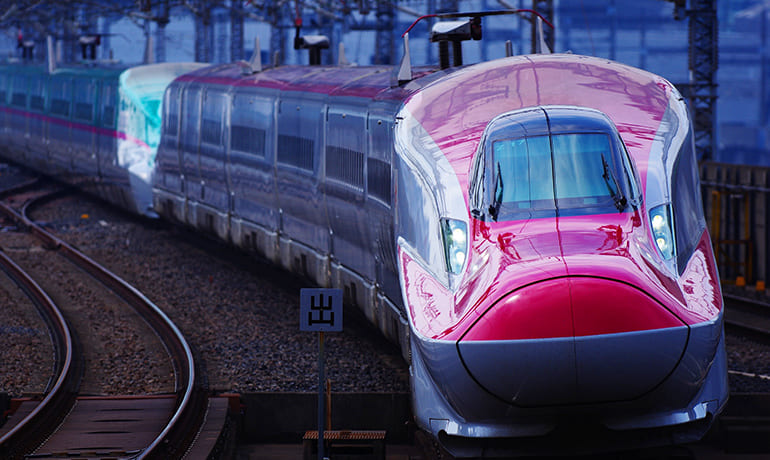
目次
みんな大好き! あの乗り物! 東北新幹線E6系こまち・E7系かがやき
今回ご紹介するのは、弊社が開発をお手伝いし量産部品も納入させて頂いた、「東北新幹線 E6系こまち、E7系かがやき」のヘッドライトカバーの開発エピソードをご紹介いたします。
実際に走っている新幹線車両の部品の開発秘話です。
タカラトミーさんのシンカリオン玩具ではありません。(笑)
射出成形ラボサイトでの事例紹介ページ
> アルミ部品を射出成形で樹脂部品に工法転換 – 東北新幹線ヘッドライトカバー –
アルミ部品を射出成形でプラスチック+メッキに! 240Kgを1kgへ!
2011年にデビューした東北新幹線「E5系はやぶさ」は、営業最高速度320km/hで走る日本最速の新幹線です。
その独特の形状が特徴の先頭車両、グリーン/ホワイト/ピンクの帯という斬新な塗色、従来のグリーン車よりも上位となる「グランクラス」と今までの新幹線とは異なる斬新なアイディアで満ち溢れた新幹線です。
大人気アニメ「シンカリオン」でも主人公が操る車輌はE5系はやぶさ!まさにE5系は東北新幹線の“主人公”ですね。
改良したい部品はヘッドライトカバーで、部品の問題点はずばり“重量”。
何と(×2)!日本が誇る最速新幹線のヘッドライトカバーはアルミニウムの削りだしで製作されていました。
そう、今回のご相談はE6系こまちでは、「アルミ部品を射出成形でプラスチック+メッキに工法転換をし、軽量化したい」というものでした。
JIS規格の壁、金型構造の変更不可、少量生産…問題山積
自動車に代表されるように、ヘッドライトカバーのような部品は当時でも既にプラスチック化が進んでおり、最初にこのお話しを伺った際には、「なぜE5系はアルミの削りだしにしたんだろう?」と逆に疑問に思いました。
しかし、お客様と徐々にお話しを進めるにつれ、大きな3つの問題点が浮かび上がってきました。
【問題1】樹脂素材とメッキ
JIS規格で鉄道車両に使用してよいプラスチックが限定されており、それらプラスチックとメッキ加飾の実績がない。
【問題2】金型構造
意匠デザインや部品取付方法などは先行されており変更はできない。
金型構造を考慮せず部品はデザインされているが、ほぼ現状のまま金型構造を成立させなければいけない。
↑ヘッドライトカバーの意匠面
↑ヘッドライトカバーの裏面
【問題3】少量生産
企画台数が500個打ち切りと少量生産品の中で、【問題1】【問題2】を含めて対応してくれるメーカーがない。
金型のスペシャリスト魂と幅広いネットワークで問題解決
【問題1への解決】JIS規格の壁。樹脂選定からサンプル作成とメッキ実験を繰り返す
プロジェクト時に初めて知ったのですが、新幹線をはじめとする鉄道車両は、対応するJIS(日本産業規格)の内容が自動車のそれとは大きく異なるという事でした。その中でプラスチックに関しては、燃えにくいこと=“難燃性”がとても重要視されておりました。
当時、我々は鉄道JISに対応でき、かつメッキ加飾が可能といわれる難燃性PC/ABSは1種類しか見つけることが出来ず、使用したことがない樹脂材でした。お客様をはじめ、樹脂材料メーカー側にも、特にメッキ加飾に関するノウハウ等がないため、ひたすら樹脂サンプルプレートをメッキ加飾する実験からスタートしました。
いくつかのプレート試験の結果、加飾品として遜色ない色、光沢を得ることが出来き、お客様に難燃性などの試験をお願いいたしました。結果はOK。
これで開発のスタートラインに立つことができました。
【問題2への解決】美しい意匠面を変えることなく、斬新な金型構造で量産化を実施
本プロジェクトは、弊社を含めた2社による“技術コンペ”の競争でした。
技術コンペ=プラスチック化が出来るか?という事です。
ですが、弊社が本プロジェクトのお話しを頂いた時点で、E5系の実績からヘッドライトカバーは従来のアルミニウム材を前提として、すでに車両設計は大きく進んでいました。
その結果、意匠面や締結方法などを変更することはできないというのが対応条件でした。
意匠や締結を遵守した形で、500個の量産製品を作る金型構造を考えなくてはいけない。しかしながら、アルミニウム材を単純に中空化して進めた部品は、射出成形の金型構造では極めて致命的ポイントがありました。
致命的なポイント:全周にアンダーカット
アンダーカットが全く成立していないのです。
まずフランジがアンダーカットとして全周に設計されており、そのフランジに締結位置がありました。これでは傾斜コアといわれる内部のアンダーカット処理方法では対応することができません。
競合他社の提案した『部品分割』
競合先が提示した案は部品分割。意匠側の部品とフランジを2部品に分け、それらを難燃性に対応した接着剤で止めるというものでした。
競合先は「難燃性に対応した接着剤」を見つけたことで、自信満々でした(笑)
手動で製品を45°回転させることで問題回避
私達はプラスチック並びに金型のスペシャリストとして、なんとか1部品構成でこの要求を満たす方法はないかと考えました。Q・Cはもちろんのこと軽量化や接着強度の工程保証などを考えれば、お客様にとって1部品構成である方が良いに決まっています。
悩みに悩んだ結果、私達は少量生産だから出来る、それに対応するから可能とする、簡単だけど斬新なアイディアを思いつきます。
私達と言いましたが、思いついたのは「私」です!
前述の通り、このようなフランジ形状のアンダーカットを金型で処理する場合、通常は傾斜コアという機構を使用します。
フランジが幅広かったり、全周にあった場合などその処理が不可能な場合は、製品や取付部位の強度を確保した上で、一部フランジをカットしてもらうことで、金型構造を成立させます。
今回のヘッドライトカバーも、お客様からフランジカットはしても良いという了解は頂いておりました。
↑フランジカットした裏面形状
しかし通常の傾斜コア構造では、本デザイン意匠形状が邪魔をし、下図のように作動方向に傾斜コアが動きません。
意匠形状を変更することはできないので、どうするのか・・・・・
“回転”させました。
製品を。
幸いな事に、ヘッドライトカバーのデザインは真円でした。
そこでまず傾斜コア構造を、リフトコア構造に変更しました。
そして製品を型から押し出した後、製品を45°クルっと手で持って回転させることで、アンダーカットを処理しました。
リフトコアがセットされた状態
手動で製品を45度回転させた状態
製品を押し出した状態
【射出成形ラボの簡易金型サービスはこちらより】
> 最短納期を2週間で!180ton射出成形機用の簡易金型を、60万からご提供いたします。
【問題3への解決】幅広い協力パートナーを活用し、少量生産への対応実現
金型、射出成形という産業は、「大量生産」の象徴です。
試作や少量生産の象徴である3Dプリンターはここ10年で大きく進化しましたが、製品によってはまだまだ金型+射出成形の工法で「少量生産」や「小ロット生産」が求められます。
金型はお客様である開発メーカーにとっては大きな投資であり、製品の売れ行きを考えれば、一種の博打です。要求品質を確保した上で、最適な投資を望まれるのはもちろんのことです。
自動車や弱電のように大量生産が見込めるものは良いのですが、残念ながら、小ロットや少量生産の分野では、その最適投資な工法に巡り合うことが少なく、お客様にはいつも大きなリスクがつきまといます。
私達は、中小企業であることによるフットワークの軽さと、培ったノウハウ、多種多様の協力パートナーを活用し、そこに「あっと驚くようなアイディア」で、少しでも皆様の最適投資に貢献できるよう努力してまいりました。
本プロジェクトにおいても、
・サンプル作成と少量生産のメッキ加飾に惜しみなく協力していただいたパートナー
・手回し回転によるアンダーカット処理というアイディア
などなど数多くの我々だからできることを詰め込んで対応させて頂きました。
軽量化プロジェクト成功とE7系かがやきの開発案件も受注
これらの提案、取り組み結果が評価され、E6系こまちは無事に当社が金型、少量生産、メッキ加飾まで受注することができました!(パチパチパチ)
では、実際に軽量化の結果はどうだったのでしょう?
アルミニウムの削りだしヘッドライトカバーの場合、その重量は30kg/個。運行車輌では前後合計8個で構成されていますので、総重量240kgでした。
それに対し、メッキ加飾をしたプラスチックの製品重量は0.25kg/個。
総重量で1kg!
99.5%の軽量化です!数字が大きすぎてよくわからないです(笑)
それだけではありません。
アルミニウム材は、その製品重量から、本体とヘッドライトカバーとの締結ボルト数が1個あたり10本。すなわち車両全体で80本が必要でした。
それが製品が軽量化されたことで、1個あたり5本のみでOK。車両全体で40本とこちらは数量及び重量を半減することができました。
プラスチック製品の重量のみで考えれば、ボルト数はもっと少なくても良かったのですが、運行時の振動揺れに耐えれる様、締め付け位置をバランスよく配置する必要があるため、5本が最小本数でした。
締結ボルトの削減はその重量だけでなく、ボルト自体の費用及び作業員の締め付け工賃も削減されます。
大きな副効果です。
このような結果から、今回のプラスチック化は大成功で、お客様にも非常に喜んでいただけました。
その証拠に、続くE7系かがやきの開発プロジェクトにおいても、“コンペティター無し・当社ご指名で”再度受注をすることができました。
自動車業界の枠を超えて。目指すは宇宙開発にも!
愛知、岐阜に大きな製造拠点を構える私達グループは、自然と自動車関係の仕事を多く頂きます。
そんな中、今回の鉄道車両開発に携わったときは、異なる産業の方と一緒に仕事ができることがとても新鮮で刺激的でした。そして、自動車産業で培ったノウハウやアイディアが他の分野でお役に立てたことが喜びでした。
当時、私の幼稚園児だった長男は鉄道が大好きで、「今度パパはE6系こまちの部品開発の仕事をしたんだよ!」と自慢したもんです。「すげぇーパパ!じゃぁ今度こまちを見に行きたい!」と言われ、東京駅まで足を運びました。
そんな長男も、現在は宇宙関係が大好きで、ISSが通るたびに空を眺め、学習机の周りはH型ロケットの写真や模型などで埋め尽くされています。
「下町ロケット」ではないですが、関東グループが宇宙開発に携わる、そんな日も遠くはないと思っております。私個人としても、グループとしても、そんな来るべき日に向けて、着々と準備を進めていきたいと思っております。
射出成形ソリューションサイト
> 小ロット・試作金型製作・コストダウン提案の【射出成形ラボ】サイト