協働ロボットのメリット・デメリットとは? 産業ロボットとの違いと可能性の高さを解説
省人化装置
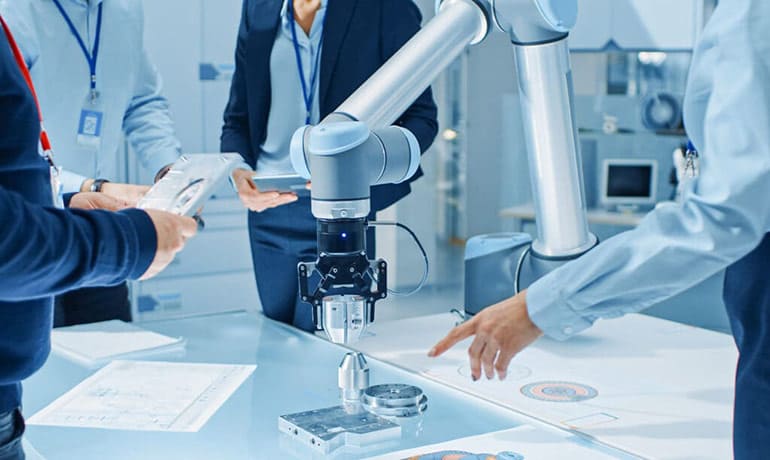
協働ロボットを使用するにあたり、従来の産業用ロボットとの違いから、メリット・デメリットが生まれます。ここでは協働ロボットのデメリットを理解した上で、それでも協働ロボットをお勧めする理由を説明したいと思います。
尚、下記動画は弊社、株式会社関東製作所で製作した「超音波カッターを搭載した協働ロボット」の動きです。
本記事、「3.ユニバーサルロボット社製『UR-5e』を使用した協働ロボット」でもご紹介しておりますので、ぜひ参考にしていただければと思います。
目次
協働ロボットのデメリット
協働ロボットのデメリットと言われる部分は大きく分けて3つあります。
【1】 動きが遅い
【2】 可搬重量が小さい(力が弱い)
【3】 価格が高い
デメリット【1】 :動きが遅い
協働ロボットは安全に停止できる事を前提に設計されているため、産業用ロボットに比べ、最高動作速度が遅く設定されています。(800~1500mm/sec程度)
しかし中には“協働モード”と“産業用ロボットモード”との切り替え付きの機種もあります。
例えば測域センサー(※1)(レーザースキャナー等)と連動し、人が近くにいない場合は産業用ロボットモードで素早く動き、人が近づいたら協働モードに切り替えて安全を確保する などの使い分けが出来、効率良く作業ができます。
- (※1) 測域センサー
- レーザー距離センサーを高速で放射状に走査して対象物を2次元的に検出する事が出来るセンサー。
また、ABB(株)製の協働ロボットには、4kg可搬で最速5000mm/secの速さで動作する事が出来る機種があります。
デメリット【2】 :可搬重量が小さい(力が弱い)
協働ロボットの可搬重量は4~16kgのものが多く、産業用ロボットほどラインナップが多くはありません。
しかし、ピッキングや部品組付け、検査など、従来作業者により行われていた作業は、協働ロボットのラインナップで充分足りるでしょう。
またファナック(株)製のものには、可搬重量35kgの機種があります。
可搬35kgといえば、人であればなかなかの怪力です。
『人の代わりに作業する』協働ロボットというより『人に出来ない作業をする』協働ロボットと言えるでしょう。
デメリット【3】 :価格が高い
価格に関しては、各軸に荷重センサーを内蔵しているものが多いので、なかなか安くはならないと思います。
しかし普及率があがれば生産台数が増え、製造ラインの効率化などで価格が下がってくる可能性もあると思います。
また、価格が高いのはあくまで産業用ロボットと比べての話ですので、産業用ロボットにできない、協働ロボットならではの付加価値を見出す事で、価格差を埋める事が可能になるのではないでしょうか。
協働ロボットのメリット
一方、メリットとしましては
【1】 安全柵が不要
【2】 専門教育が不要
が挙げられます。
産業用ロボットと比較してのメリットという点ではこの2点が目立つところですが、この2点には無限の可能性が生まれます。
メリット【1】 :安全柵が不要
まず安全柵が不要であれば、狭いスペースに設置出来たり、自由に移動させたりすることが可能になります。
生産ラインにおいて協働ロボットを、『ある特定の製品を生産するときのみ使用する(または使用しない)』というような使い分けも可能です。
また、『協働ロボットに重いワークを持たせた状態で作業者が組付けをする』事や、治具なしでも空間に位置決めが可能になる事で作業者とのコラボレーション作業により、設備費のイニシャルコストの削減が可能になる場合もあります。
小ロット・多品種を生産する現場などでは非常に有効な活用法となるでしょう。
メリット【2】 :専門教育が不要
次に専門教育が不要という点では、専門の技術者でなくてもティーチング(※2)が行えることを意味します。
すなわち、いくつかのハンドユニット(※3)さえあれば、設備メーカーを呼ばなくても、現場サイドで新製品の生産ライン向けに、ロボットの動作を変更したりすることが出来ます。
よって、ここでもイニシャルコストを削減する事が出来るでしょう。
また、『特定の人物だけが触れる装置』ではなく『誰でも触れる道具』であれば現場の中で様々な活用法のアイデアが生まれる可能性があります。
- (※2) ティーチング
- ロボットに動作を教え込む(プログラムする)事、教示ともいう。
- (※3) ハンドユニット
- ロボットの先端に取り付けるユニットの事で例えばピッキング用のユニットであれば、クランプシリンダでワークを掴めるようなものであったり、バキュームパッドで吸い付けるものであったりします。
ユニバーサルロボット社製『UR-5e』を使用した協働ロボット
実際に弊社関東製作所で製作した協働ロボットのご紹介をいたします。
協働ロボットはユニバーサルロボット社製の『UR-5e』を使用しました。可搬重量は5kgながら可動半径1000mmをカバーしていまして、人で言いますと腰から上を使って手が届く作業エリアに近いと思います。
このロボットに超音波カッターを持たせ、ワークとなる樹脂製のブロー成形品を仕上げ加工します。
ロボットは2つの治具をセットできるテーブルに固定されており、例えば、右側のワークを加工している際中に左側のワークの入れ替えが可能なため、ロボットを止める事なく生産を続けられる仕様となっています。
そうすることで、協働ロボットのデメリットである『動きの遅さ』をカバーしています。
もちろんワークを入れ替える際には、ロボットの動作スピードを安全速度にまで落とし、作業者に危険が及ばない様に配慮しています。
『超音波カッター搭載の協働ロボット』の導入事例
> 【お客様の声】工場の省人化にいち早く取り組む(株)トーカイ・アピア様 そのメリットを語る!
また、弊社が使用している超音波カッターは、先端のカッター保持部を『工具ホーン』と呼ばれる溶着用の部品に交換する事により『超音波かしめ溶着機』に早変わりします。
小ロット多品種の工程であっても、治具を用意するだけで簡単にティーチングができ、作業者による手作業を減らし、安定した品質を得られる事でしょう。
>【プラスチック製品開発のベストパートナー】株式会社関東製作所コーポレートサイトへ
関東製作所は「金型の設計・製作」から「小ロット~量産の成形品の生産」、「省人化装置や専用加工機の設計・製作」「部品の調達」まで、幅広い生産技術代行サービスを行います。
関東・東海・九州・インドネシアより、お客様に合わせたベストなソリューションを提案致します。
プラスチック製品製造のあらゆる工程に関わる関東製作所
このように、製造業界においての省人化が進められる昨今において、キーになるのは協働ロボットの存在と言えるかと思います。何と言っても人件費削減や人手不足の解消に貢献し、従業員の安全環境を提供してくれる可能性を大いに秘めていますから。
弊社関東製作所は長年にわたり、金型製作をはじめとし、プラスチック製品が工場から出荷されるまでのあらゆる工程に関わる事業に携わって参りました。
特に、協働ロボットや樹脂製品の後加工機械等の製作には長い経験を誇ります。
金型の設計・製造から、樹脂成形、そして後加工機械提案・制作まで一貫して提供できるのが弊社関東グループの強みです。
工場の省人化・効率化でお困りの際は、きっとお力になれるかと思います。
是非とも、ご用命くださいませ。