リークテストでプラスチック製品の品質を確保する|リークテストの種類と検査工程を解説
省人化装置
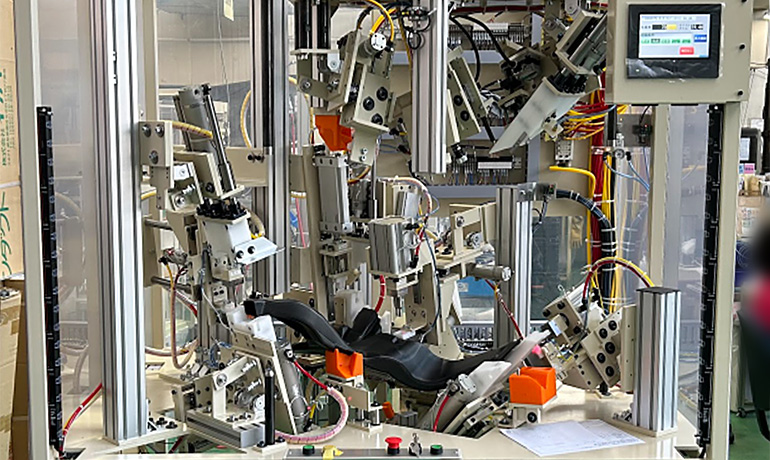
リークテストとは、プラスチック製品の中でも主に容器やタンク、ダクトのような気体や液体などを入れたり流したりする製品において、その品質を確認するための検査となります。
本記事ではこの「リークテスト」について、その工程やタイミング、さらには具体的な検査方法まで詳しく解説しています。
目次
リークテストとは
まず、リーク「Leak」は日本語で「漏れ」と訳します。テスト(Test)は日本語で「検査・試験」ですね。直訳すると「漏れの検査」となります。
プラスチック製の容器やタンク、ダクトなどでは、気体や液体を溜めたり流したりする用途で使用されるので、このリークテストを実施して漏れの検査を行う必要があります。
またリークテストには様々な手法があり、主に空気(ガス)や液体を用いて検査します。目的や対象製品によって、それぞれ適切なリークテストの方法を選択します。
こちらの記事は、動画でもご覧いただけます。
なぜリークテストを行うのか?
例えば、浮き輪を膨らまして栓をし、穴が開いていなければ使う事ができます。逆に穴が開いていたら、浮き輪は萎んでしまいますから使えないですよね。
当然の話ですがそれと同様に、空気が流れるダクト、液体を入れるボトルやタンクなどは、製品に穴が開いていたら空気や液体が漏れてしまい、製品としての役割を果たせません。
例えば、不具合のあるプラスチック製品が車に組付けられては、当然リコールの対象となってしまいます。それを事前に防ぐために、このリークテストとは非常に重要な検査なのです。
どのタイミングでリークテストするのか?
プラスチックの容器やタンク、ダクトを生産する際にリークテストを実施することが多いですが、プラスチックの製造方法によって、実施するタイミングは異なります。
ブロー成形におけるリークテスト
プラスチック製の容器やタンク、ダクトの多くはブロー成形で生産されます。
ブロー成形の場合、成形機から成形品が出て来た直後に、加工機で加工する工程(インライン工程)があり、主にそのタイミングでリークテストが行われます。
ブロー成形では、成形後の後加工が必要なため、NG品の加工を行う前にリークテストで漏れが判明したら、その製品は即粉砕機行き(不良品として廃棄)となります。
[関連記事]
> ブロー成形品に対応した『検圧・穴あけ・切断加工機』の機能を知る 省人化装置導入のすすめ
射出成形の場合におけるリークテスト【動画あり】
射出成形でダクトやタンクなどの製品を作る場合は、2部品を溶着で合体させることでダクトやタンクの形状を作るケースが多く、その溶着加工後にリークテストを行います。
特に弊社(株)関東製作所のエアリークテストでは、最小で直径1mmの穴の漏れまで検出できます。
リークテストの方法を解説
一般にリークテストの方式は数種類ありますが、大きく分けると2種類です。
※仮にボトル(容器)を想定して解説します。
① 空気(ガス)を用いたリークテスト
加圧放置法(エアリークテスト)
加圧放置法とは、ボトル内部を窒素ガスなどで加圧して、一定時間での内部圧の変化を確認する方法です。
真空放置法
ボトル内部を真空状態にし、一定時間で真空状態の変化を確認する方法です。
② 液体を用いたリークテスト
水圧法
ボトル内部に水圧をかけることで水漏れを確認する方法です。
空気と水を使用したリークテストそれぞれのメリット・デメリット
メリット | デメリット | |
---|---|---|
空気を用いたリークテスト | 漏れ量をセンサで数値化できるので、結果の信憑性が高い | どこに穴が開いているかを探すのが困難 |
液体を用いたリークテスト | 穴が開いた場所から気泡が出るので場所の特定が容易 | 検査対象の製品が水濡れNGの場合は使用不可 |
他にも、石鹸や染色液を用いるような方法や、空気と水の両方を組み合わせて検査するような方法もございます。
差圧式圧力降下方式
弊社ではエアリークテストの「差圧式圧力降下方式」を用いることが多いです。
差圧式圧力降下方式とは端的に言うと、検査対象となる製品とすでに検査合格したOK品とを検査比較する方法です。エアを製品に注入後、OK品と内圧の変化を計測して漏れを判定します。差圧センサにより、漏れによるワーク内の圧力変化を、OK品との圧力変化の差として検出します。
弊社では前述の通り、リークテストの方式は数種類ございますので、お客様のご指定や要望に沿ったリークテストの方式を採用します。
エアリークテスト「差圧式圧力降下方式」の検圧方法
エアリークテストの「差圧式圧力降下方式」での検圧方法ですが、
【昇圧】→【充填】→【平衡】→【検圧】→【針詰まり確認】
の全てをクリアしたら検圧終了となります。
弊社が「差圧式圧力降下方式」を優先的に用いるのは、精度の高い検査にこだわっているからです。トータル5工程を、1工程ずつスモールステップで検査クリアしていくこの検査方法は、最も信頼のおける検査方法と言えます。
差圧式圧力降下方式のテストフロー
【昇圧】~【針詰まり】確認の時間については、製品毎に変更します。当然、大きい製品の方が検圧終了までの時間が長くなります。
昇圧 | 昇圧とは、「製品にエアを注入して圧力を上げること」です。昇圧では、設定した下限値に到達していなければ、その時点でNGとします。 |
---|---|
充填 | 充填とは、「欠けているところや空いている空間にものを詰めて塞ぐこと」です。エアリークテストでは、製品という空間にエアを詰めることを指します。 |
平衡 | 平衡とは、「つりあいがとれて物事が安定した状態にあること」です。リークテストでは充填を止めて、製品の膨張を落ち着かせて安定させることを指します。平衡時間は、充填完了時の圧力との差を比較して設定します。 |
検圧 | いよいよ検圧です。ここで詳細なリークテストを行います。ところで充填中は昇圧しますが、充填後は降圧(圧力降下)します。この降圧こそが内圧の変化を見ている状態であり、差圧式圧力降下方式の最も重要なところです。 |
針詰り | 針詰まり確認は、検圧終了後に検圧針が後退してから開始します。設定した時間の経過後に、検圧針に詰まりが無いか判定します。 針詰まり確認をする理由は、エアが注入できたとしても、針詰まりがあると針穴全体からエアが流れないため正常なエアが確保できず、良品判定ができないからです。 |
リークテストのエラー内容
昇圧エラー | 昇圧の時点でエアーによる加圧が出来ず、空気が抜けている状態です。 |
---|---|
検圧エラー① | 平衡の状態までは維持できたが、検圧時に良品と比較して降圧のスピードが早い状態です。 |
検圧エラー② | 昇圧完了後に、検圧時間の終了までに圧力の設定値から外れた状態です。 |
針詰りエラー | 検圧の状態までは良品と同じ数値ですが、針詰りが原因で降圧で圧が抜けきらない状態です。 |
まとめ
弊社メカトロニクス事業部は、様々なプラスチック製品の後加工専用機を製造しており、設計はもちろんのこと、部品製作、組付け、電気配線、制御プログラム、納品調整まで自社で一貫して対応しております。
特に今回ご紹介したようなリークテスト機の製造案件に関しては、まずはお客様から対象となるプラスチック製品をお借りし、最適な条件を徹底的に洗い出します。そのため、量産を見越した加工サイクルのスピードアップやコストパフォーマンスを加味した機械仕様の提案に注力しております。
弊社は特に、自動車用のタンクやダクトを成形する金型などとセットで、リークテスト検査機の販売実績が豊富にございます。リークテストだけでなく、様々な検査機でお困りの事案があれば、是非弊社までご相談下さい。
[関連記事]
> プラスチックの接合方法『溶着』を学ぶ。自動化・省人化を見据えたそのメリットと種類