ブロー成形品に対応した『検圧・穴あけ・切断加工機』の機能を知る 省人化装置導入のすすめ
省人化装置
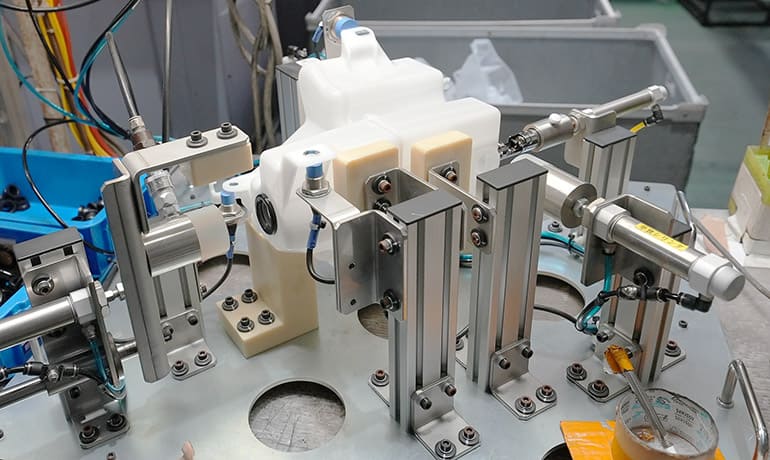
当社、株式会社関東製作所で製作している省人化装置のうち、最も生産台数が多いものがブロー成形品の『検圧・穴あけ・切断加工機』です。
とは言え数年前までは5割近くを占めていたのですが、近年、溶着機などの組付け機や検査機が増え、昨年実績ではおよそ3割程度でした。
組付け機や検査機が増えた理由としては、コストダウンを目指しての省人化や自動機での作業による品質の安定化、センサーやカメラなど『機械の目』による検査で不具合品の流出を許さない品質強化の流れが強くなったからと考えています。
本記事では、省人化装置の動きを動画でもご紹介しております。工場内の省人化を検討されている方々にはぜひご覧いただきたい記事となります。
目次
主に車載用エアコンダクトに使用される『検圧・穴あけ・切断加工機』とは
他の記事でも書いたのですが、ブロー成形で製品を製造する場合、後加工が必須となります。
ボトルのような一部例外もありますが、ダクトやホース、タンクなどブロー成形で製造される主だった製品には、切断や穴あけ、切削やリークテストなど様々な後加工(後工程)が必要となります。
その中で『検圧・穴あけ・切断加工機』は主に、車載用エアコンダクトの生産に使われます。
元々は『穴あけ』と、捨て袋と呼ばれる不要な部位の『切断』だけを行う機能が主流でした。
しかし、自動車の低燃費化が進むにつれ部品の軽量化が必須となり、ブロー成形品も薄肉の製品が多くなるとともに、製品に穴が開く不具合が発生するようになってきました。
その穴あき不具合を作業者の目視ではなく、設備で検出するために『検圧』が追加されるようになりました。
現在では殆ど全てのダクト加工機に検圧機構が付いています。
ブロー成形品の『吹き込み穴』を利用した『検圧』方法
それでは『検圧』の仕組みについて説明していきます。
ブロー成形品は内部にエアーを吹き込み成形するため、必ず『吹き込み穴』が存在します。当然、製品に不要な穴はNGですので、吹き込み穴は基本的には捨て袋に設定されます。
[ブロー成形の基本情報が掲載された記事]
> ブロー成形金型の特徴とは? ブロー成形を製作する上でのメリット・デメリットを知ろう
その『吹き込み穴』を利用し検圧を行います。
まず、製品をクランプし、吹き込み穴に『検圧針(検圧ピンともいう)』を刺します。その際、吹き込み穴と検圧針の間に隙間が出来ない様にパッキン等で補助的にシールする場合もあります。
検圧針からエアーを注入し製品が破裂や変形しない程度の圧力で充填します。設定した圧力に到達したらエアーの供給を止めます。
そのまましばらく待って圧力が下がらなければ『穴が開いていない』と判断され検圧は合格となります。
※こちらの参考動画はブロー成型品ではなく、射出成形品を溶着して作られたプラスチックのタンク製品です。
ただし、圧力がかかった状態では製品はわずかながらですが徐々に延びていくため、内容積が拡大し、圧力が下がります。
その下がり方が『穴あき』か『内容積の拡大』かを判断するところにノウハウが必要となります。
開口後の寸法精度にも注力した『穴あけ』機構
検圧に合格すると加工に進みますが、多くの場合『穴あけ』を先に加工します。
なぜかというと、加工機のサイクル途中で何らかの原因で停止してしまった場合、作業者は加工機から取り出したその製品が『加工途中の状態』なのか?『加工完了後状態』なのか?を判断する必要が発生します。
その判断の目安として『穴が全て開いているか?』を確認するより『捨て袋が全て切断されているか?』の方が確認し易いからです。
箱詰めの際にも穴が開いていなくても箱詰めできてしまいますが、捨て袋が付いていると箱詰め時に干渉するなど、作業者が気付く可能性が高くなるからです。
2通りの『穴あけ』プロセスを紹介
続いては『穴あけ』プロセスについて説明していきます。
『穴あけ』には主に2通りの方法があります。
プレス加工
パンチ(オス)とダイ(メス)で製品を挟んでパンチを貫通させて穴あけします。紙などに穴をあけるあのパンチと同じしくみです。
穴径の精度が高いので構造的に成り立つ場合はこちらを選択します。
ドリル加工
モーターでドリルを回転させて穴あけをします。
この方法では、プラスチック製品に対しては、芯ブレにより穴径が大きくなってしまったり、加工した穴の周りにバリが残る場合があるため、プレス加工が成り立たない場合にのみ採用します。
※当社ではドリルの形状を工夫し、穴径精度が高くバリの少ない加工が可能です。
穴あけする場所がフランジ形状の様にコンプレッション(※1)された部分であればプレス加工、胴体部分のように裏側にプレスダイを配置出来ない場合はドリル加工というように形状に合わせて設定していきます。
- コンプレッション
- ブロー成形で中に空気のスペースを作らずパリソンだけを金型で挟んで形成する方法。
ブロー成形品特有の、捨て袋をカットする『切断』工程
『穴あけ』が終わると『切断』工程になります。
ブロー成形品の、特にダクトの捨て袋カットに絞った話ではありますが、『切断』の方法は『ギロチン切断』と言われる切断方法が主流です。
『ギロチン切断』とは何かと言うと、平板の切断刃で製品と捨て袋の境界線を狙って刃物を差し込んで押し切りする、まさにギロチンのような切断方法です。
この際、肉厚や製品形状の影響で切断刃が製品に食い込んだり、捨て袋側に食い込んで切断公差以上に切れ残りが発生したりすることがあります。
ある程度は設計段階で対策を練りながらも、実際どのように切れるかは『一度切ってみないと分からない』状態のため、調整に苦労する事もあります。
しかし弊社では長年培った経験を基に、様々な方法を駆使して公差内で切断できるように調整しています。
まとめ
以上の『検圧』『穴あけ』『切断』の工程を、製品をセットしてスタートボタンを押すだけで自動で行えるのが『検圧・穴あけ・切断加工機』です。
エアシリンダやモーターを駆使して作られたこの省人化装置は、成形作業者の負担を軽くするだけでなく、『工場内の省人化』『ヒューマンエラーの削減』『製品の精度向上』を叶える様々な知恵が織り込まれています。
今回ご紹介したブロー成形品の『検圧・穴あけ・切断加工機』以外にも、当社では様々なプラスチック製品の後加工専用機を製造しており、設計から部品製作、組付け、電気配線、制御プログラム、納品調整まで自社で一貫して対応しております。
ブロー成形の後加工機でお困りの方、工場内に省人化装置の導入をご検討の方、ぜひ一度、関東製作所にご相談ください。