金属加工現場の工数削減事例その1 4割削減を果たした関東製作所 関工場の取組みとは?
金属・部品加工
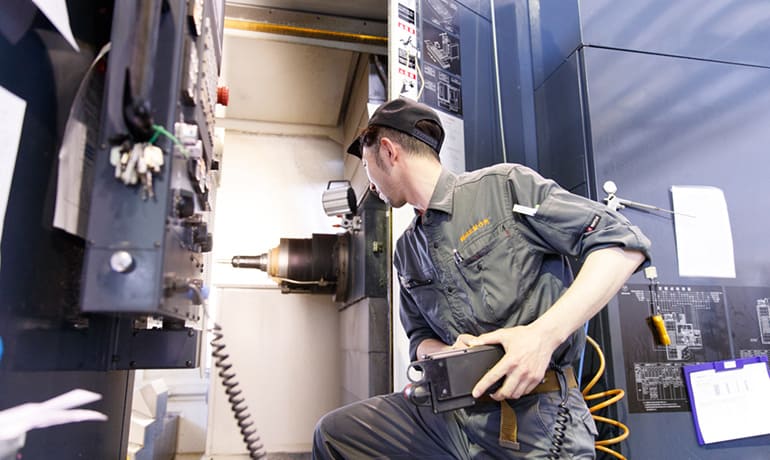
どんな業種においても仕事をする上で、「工数削減」は永遠のテーマであり、またそれぞれの会社様ごとに知恵と工夫を凝らし、取り組まれていると思います。
関東製作所でも、金型製作・金属加工を通して、今まで培ってきたノウハウを活かし、日々工数削減に取り組んでいます。
今回、金属加工のワーク固定法の改善により、段取り工数を3割削減。さらに、工具の見直しにより切削工数を4割削減を実現できた事例を紹介させていただきます。
目次
【工数削減Point1】 ワークの固定を「ピッチ定盤」から「治具板」へ
金属加工においてワークの固定方法には会社様ごとのノウハウが多く含まれています。
当社の場合、以前はピッチ定盤や市販されている既製品の道具を用いてワークを固定していました。
BEFORE:大型サイズのピッチ定盤を使用した効率の悪い加工段取り
以前は1500mm×1000mm 厚み50mm重量580kg の鉄板に50mmピッチで穴があいているピッチ定盤を使用していました。
ワークにはNC加工用のタップ加工を施し、この穴を使ってピッチ定盤とワークを固定します。
このピッチ定盤を使用する場合、以下5段階の工程を必要としていました。
【工程1】 設計担当によるNC加工用M16タップの設定
【工程2】 CAMのNC加工用M16タップの加工データ作成
【工程3】 クレーンを使用し、ピッチ定盤を運搬する人的作業
【工程4】 ピッチ定盤(350kg)+ワークの状態での反転作業
【工程5】 加工機テーブルのキー溝を使用しない平行出し作業
↑イケールのキー溝を使用しないため、機械で平行出し作業が必須となる
ここでの問題は、小物から大型までどんなワークサイズでもこのピッチ定盤が必要になる事です。
ワークサイズが小物であっても、580kgのピッチ定盤を付けた状態でクレーン作業、平行出し作業を行う必要があります。
またピッチ定盤とワークは平行に固定されているわけではないため、加工機テーブルのキー溝も利用することができません。
AFTER:治具板を活用することで段取り工数3割削減を実現
このような問題を解決するために「治具板」というものを製作しました。
この治具板とは、220mm×185mm 厚み36mm 重量11kgの鉄板に、M16キャップボルトを通せるザグリ穴とクランプ用の溝を施した構造をしています。
これを4枚1セットで使用します。
金型の製品側ではない側、つまり裏側には「水冷穴」「バキューム穴や溝」「シリンダーの取り付け穴」「スペーサーの取り付け穴」など、成形に必要となる機能的な加工をします。
裏側の長手にはスペーサーを取り付けるためのM12タップが設定されています。
このM12タップをM16タップに変更し、ピッチ定盤から治具板に変更することで、段取り工数を3割削減となりました。
その具体的な効果はというと、
【工程1】 設計担当によるNC加工用M16タップの設定
→ 不要
【工程2】 CAMのNC加工用M16タップの加工データ作成
→ 不要
【工程3】 クレーンを使用し、ピッチ定盤を運搬する人的作業
→ 不要(手で運搬可能)
【工程4】 ピッチ定盤(350kg)+ワークの状態での反転作業
→ 治具板(44kg)+ワーク重量で反転 (工数1割削減)
【工程5】 加工機テーブルのキー溝を使用しない平行出し作業
→ 加工機テーブルのキー溝を使用した平行出し (工数2割削減)
↑平行な加工機テーブルのキー溝に対しワークは完全に平行を保てるので、機械による平行出し作業は不要になる
↑加工機テーブルのキー溝に精度板を挟み込んだ様子
このように、その削減ポイントが多方面に表れてきました。
ワークサイズが大きいものになる程その効果も大きく、さらに1割程度の工数削減になることもあります。
【工数削減Point2】 スチール加工・アルミ加工 それぞれの加工条件を確立
今までは
・ワークを1枚のピッチ定盤でM16タップを4か所で固定し、
・そのピッチ定盤を4つのクランプで固定していた
ものから、
・1枚の治具板でM16タップを1か所で固定し、
・その治具板を1つのクランプ(これを4か所)で固定
することになります。
そのため、導入当時は本当に材料が固定できるか、かなり不安な気持ちでいっぱいでした。
↑治具板を取り付けた状態の写真
当社における、材料固定の厳重さが特に問われる切削負荷の高い加工というのは、下記2つの加工が挙げられます。
・被削材スチールの荒加工
・被削材アルミの荒加工
スチール加工の加工工数削減
既存の工具使用時ではロードメーター70%前後、加工振動は比較的大きい印象でした。
段取りの工数削減を優先したい為、少々切削能力を落とす事を検討したのですが、せっかくのメリットを最大限に活かしたいという事で、各メーカーの協力を得て工具の見直しをする事にしました。
今回協力を依頼したメーカー様はDIJET社様とOSG社様の2社。工具の評価を提出することを条件にレンタルをさせて頂きました。
今までと同条件で加工を行った結果、ロードメーター50%前後、また加工振動がかなり小さかったDIJET社様の工具を採用することになりました。
この効果として、送り速度は既存工具の約1.6倍速く、工具寿命は当社の基準に対し約2倍以上長くなりました。
このことから荒加工で使用する工具の本数は半分になり、加工工数は4割削減になりました。
下記は、スチール加工における当社仕様の加工条件です。
被削材:S50C相当の場合
メーカー | DIJET |
---|---|
名称 | SKG-5050R-10-22 φ50 |
チップ | JC8118 SPMT100415ZPTR-PM |
回転 | 1020 min-1 |
送り速度 | 7320 mm/min |
径方向 | 30mmピッチ |
軸方向 | 1.2mmピッチ |
アルミ加工の加工工数削減
スチール加工の結果から、ワークは問題なく固定されていると判断できたので既存の条件をそのまま採用。ロードメーター60%前後で問題なく加工ができました。
被削材:アルミ50系相当の場合
メーカー | MOLDINO |
---|---|
名称 | ABR4080R-6 φ80 |
チップ | JS4060 RDMT1204MOTN |
回転 | 2500 min-1 |
送り速度 | 7500mm/min |
径方向 | 68mmピッチ |
軸方向 | 2mmピッチ |
以上のことからピッチ定盤を治具板に変えることをきっかけに実現できた、トータルの工数削減は、
・段取り工数 3割削減
・被削材スチール 荒加工工数 4割削減
となりました。
この治具板は特に特殊な加工を施しているわけではないため、容易に製作することができます。
当社では同様の機能を持った3つのサイズの治具板を製作し、最大2600mm×1200mm 厚み400mmのワークサイズに対応させています。
見る人から見ればただの鉄板なのですが、この鉄板が生み出す価値は大きく、工数削減により最終的には私たちが手掛けるブロー金型のコスト削減につながります。
まさに、「道具を制する者は時間を制す!」ですね!(笑)
関東製作所グループ 工数削減への取組み
このように私たち関東製作所では、日々工数削減へのアイディアを出し合い、トライ&エラーを繰り返すことで、確実に業務効率化のフローを取り入れております。
そして削減できた工数は、お客様へのコスト削減に還元できるものと考えております。
関東製作所グループは70年以上の歴史を持ち、特に金型製作に関しては、設計から製造までの一貫生産体制をしいております。
さらに、東京・静岡・愛知・岐阜・福岡の国内複数拠点に加えて、国外ではインドネシアからも対応が可能です。
私たちはグループ一丸となり、金型の設計から成形品の生産まで、安定した製品づくりのご提案をお約束いたします。
> 金属加工現場の工数削減事例その2 製作治具で干渉リスク回避&作業効率2倍の効果とは?