プラスチック製品の小ロット成形に適した工法『真空注型』とは? そのメリットとデメリットを学ぶ
プラスチック
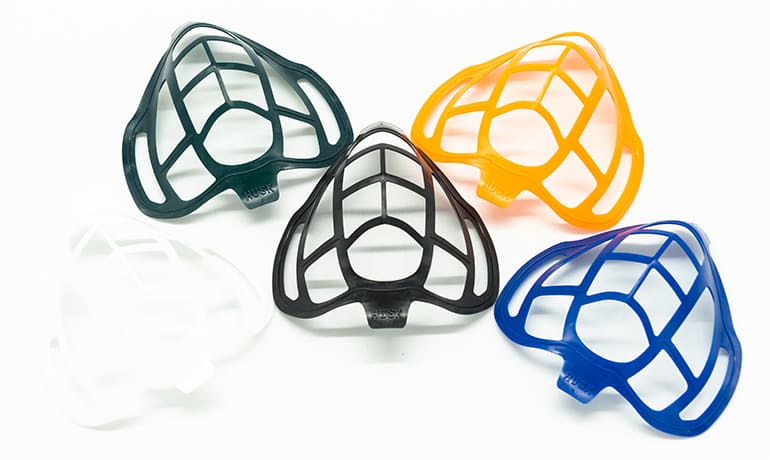
プラスチック成形の工法には種類があり、製作時には製品に合わせて最も適した工法を選ぶことが重要です。
今回はその代表工法『真空注型』について、その特徴や活躍どころをご紹介いたします。
真空注型とは?
真空注型とは、金型を作らずシリコンの型を使い、真空下で液状の樹脂剤を流し込んで成形する工法をいいます。基本的な構造としては、射出の金型と同じ考え方での成形が可能です。
真空注型では、製品データを基に3Dプリンターなどで複製の元となるマスターモデルを製作。
マスターモデルの周りにシリコンを流し込み、固めたところで型を割ってマスターモデルを取り出せば、シリコン型が完成します。
シリコン製の型なので耐久度は金型と比較すると弱いのですが、型費が安く、小ロット製品に適した成形方法といえます。
こちらの記事は動画でもご覧いただけます。
小ロットって、どのぐらいの数量が真空注型の適正数量なの?
真空注型は、10~100個程度の製品の製作に適しています。
金型と比べてシリコン型の耐久度は低いため、1型あたり約20ショット程で型は消耗してしまいます。
しかし、シリコン型は容易に増産が可能で、1つのマスターから5型くらいまでは作ることができます。また簡易な形状のマスターなら1型に5個など複数個並べ、一度に5個分作れるシリコン型の成形も可能です。
真空注型のメリット・デメリット
真空注型のメリット
真空注型のメリットは、
①小ロット向きであり、納期が短い点にあります。
②指紋まで転写するレベルで転写性に優れ、細かい意匠の再現が可能です。
③3Dプリンターと比較すると強度が強いことも特筆すべきメリットです。
真空注型のデメリット
デメリットとしては、一般的に金型ほど寸法精度が出せないケースも出てくる点でしょう。
製品の製作に使用する樹脂は熱硬化性樹脂のため、熱を加えながら成形品を作ります。
一方で、シリコン型には熱を加えると膨張してしまう性質があり、注型メーカーごとのノウハウ次第で、寸法精度が異なってしまう場合があります。
その点、弊社協力メーカー様は独自で研究開発を重ねたノウハウで、JIS中級の公差までの精度出しを可能としており、さらに1mを超える製品にも十分対応可能です。
真空注型が活躍する場面
真空注型は、小ロットの製品や射出成形品の試作として多く使われます。例えば、100個程度で打ち切りの製品に関しては注型品が多くなります。
特に大きな製品は、『切削加工』にて貼り合せで作ったり、『3Dプリンター』で作る場合があるでしょう。しかしこれらの工法は強度に不安があるため、一体で作れる注型が実用品として採用されるケースが多いです。
また射出成形品の補給品の場合は、金型が良い状態で保管されていればいいのですが、何十年も使わない金型はひどく錆びている可能性があります。金型に対して大がかりなメンテナンスが必要な際は、注型で生産した方がコストメリットが高くなる場合があります。
- 補給品
- 廃番になった製品が、リピート発注されたもの。多いケースでは、壊れてしまった部品を数点追加でほしいなど。
射出成形と比較して
真空注型は、生産性の基礎であるQCD(Quality「品質」/Cost「コスト」/Delivery「納期」)に優れているといえます。射出成形と比較して同等の「品質」で、小ロットにメリットのある「低コスト」「短納期」を実現することができます。
また真空注型の大きな強みに、無理抜きが可能な点が挙げられます。
アンダーカット形状等は、金型では通常「スライド」と呼ばれる構造を入れ、製品を取り出せるようにします。射出成形においてアンダーカット処理のためのスライド機構を追加することは、金型費の増加を意味します。
しかし、注型の場合はシリコン型側が変形することでつっかえることなく、多少のアンダーカットは引き抜くこと(無理抜き)が可能なのです。
真空注型で射出成形品の試作をする際の注意点
上記の通り真空注型という工法は、金型では取り出せない多少のアンダーカットがあっても成形することができます。
しかしここで注意しないといけないのは、注型で試作ができたからといって、全く同じ形状が射出成形金型で成立するかは別問題です。
同じ型とはいえ、金属でできた金型とシリコン型は全く別物です。
場合によっては量産のタイミングで形状変更をしないと、金型が成立しない可能性があるため、量産を控えた試作においては、射出の金型・成形に知見のあるメーカーとのタイアップも必要となるでしょう。
写真は弊社協力メーカー様『株式会社東和デザインモデル様』自社製品『HUSK』。
試作品を真空注型で製作し、その後射出成形で量産した製品になります。
真空注型の製作の流れ
【その①】マスターモデルの製作
【その②】マスターの周りにシリコンを流して固める
【その③】PL(パーティングライン)を取り、キャビ/コアに分ける
【その④】マスターを取出してシリコン型の完成
【その⑤】真空装置に入れ、ウレタン樹脂を流し込む
【その⑥】乾燥炉に入れウレタン樹脂を硬化後、成形品を取り出す
何故、真空装置に入れるの?
真空にせずに樹脂を入れると、型内の空気が邪魔をしてしまい、末端までうまく樹脂が入らないためです。
真空下で型内の空気を抜き、リークし(空気を入れ)ながら樹脂を入れることで今度は材料が引き上げられ、型内に綺麗に樹脂が回ります。
真空注型で実現できる製作期間は?
真空注型の製作期間は短く、シリコン型は約1日で製作が可能です。
ごく一般的な大きさであれば、発注日の翌日にはウレタン樹脂を入れて成形が可能です。(車のバンパーなど200~300㎏クラスの大きなものだと、表面は固まっても内側が固まらないため、二日間くらいオーブンの中に入れる場合もあります。)
- 熱硬化性樹脂と熱可塑性樹脂
- 樹脂は、熱硬化性樹脂と熱可塑性樹脂に分けられます。
熱硬化性は加熱する事で固まります。シリコンやウレタンは熱硬化性樹脂なので、熱をかけることで形状を固めます。
逆に、熱を加えると溶ける熱可塑性は冷やして固めます。射出成形など、特に金型で使用する樹脂は熱可塑性樹脂となります。
真空注型で使える樹脂材とは
真空注型で使える樹脂剤には、ウレタン樹脂があります。
熱可塑性樹脂は使うことができないのですが、ABSライクやPPライクなど、金型成形で一般的に使われるABSやPPに、非常に物性の近い樹脂の使用が可能です。(※物性が近いとは、硬さが近い材料のこと)
ご相談いただければ材料の調合も可能なので、強化用のガラス入り等の材料も使うことができます。後処理次第で難燃性(V0)相当の成形品も製作できますし、耐候性も持たせる事も可能です。
目的に合わせ、どのような物性が必要かを相談しながら対応が可能かを確認するのが大切です。
まとめ
以上のように『真空注型』とは、金属ではなくシリコンで型を作り、そこに材料を流し込んで成形する工法です。同じ型でも金属を使わず削る必要もないため、金型よりも圧倒的にイニシャルコストは安いです。
弊社では特に、必要個数が30個以下の場合、工法検討に入れております。
射出成形に近い成形方法で、小ロットの生産に適した真空注型という工法。強度は3Dプリンターよりも強いので、十分機能部品・外観製品として検討できます。
特に量産を控えた試作品をお考えの方、ぜひ一度当社にご相談いただければ、トータルでのイニシャルコストを抑えた提案をご期待いただけるでしょう。
> プラスチック製品の試作・小ロット生産が可能な工法を紹介 それぞれのメリット・デメリットを知る
> 射出成形で小ロット生産が可能な㈱関東製作所グループの環境とは? 成形条件と費用の関係を知る
【射出成形ソリューションサイト】
> 小ロット・試作金型製作・コストダウン提案の[射出成形ラボ]
射出成型ラボは、小ロット・特殊品・試作品の設計から後加工まで一貫して対応可能です。ソリューションやコストダウンの提案も行っています。
【コーポレートサイト】
> 株式会社関東製作所ホームページ
関東製作所は金型の設計製作から試作・小ロット~量産の成形品の生産、専用加工機の設計製作、部品の調達まで、生産技術代行サービスを致します。
関東・東海・九州・インドネシアからお客様に合わせたベストなソリューションを提案致します。