『バイオエポキシ樹脂』で作る、半透明のデザインチェア!READYMADE製『EASY CHAIR』第二弾!
プラスチック
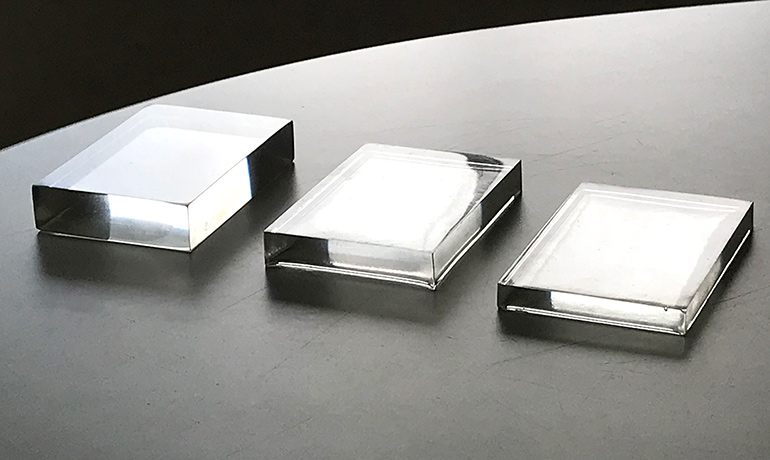
関東製作所 カーボンニュートラル推進課の丸山です。
今回は、アパレルブランドREADYMADE様とのバイオプラスチックを活用したモノづくり第二弾『バイオエポキシ樹脂でできた半透明のモダン&シンプルデザインチェア』の制作ストーリーをお届けします。
目次
『EASY CHAIR』第二弾!PET樹脂を原料とした透明な椅子
話の発端は、『第一弾 ペットボトルキャップを原料としたEASY CHAIR』に続く第二弾として、『ペットボトル本体のPET樹脂を原料とした透明なEASY CHAIR』を作りたいとREADYMADEデザイナー 細川雄太様より、ご要望がありました。
進めるにあたり、設計チーム内で形状把握・認識が必要なので、まずは参考用としてデザイナーがイメージしているビンテージ品の椅子を送っていただき、椅子の骨組みを寸法測定しました。
ビンテージ品だけあり使用感がたっぷりで、かなり年季のはいったものでした。
[関連記事]
> 「サスティナブル×ものづくり」への参画 レディメイド製デザインチェアのテストピース作成ストーリー
[動画でご覧になりたい方はこちら]
モデルとなる現物チェアを測定しCAD上でイメージ再現
座・肘・脚・背などの基本構造は前・横・後ろからメジャーで測定してCADで再現。プロッターで原寸プリントしたものを椅子にあてがい誤差を修正します。
CADを使っているとはいえ、なかなかのアナログ作業ですね。ただこういった地道な作業を積み重ねることで、製品のイメージも頭の中で徐々に出来上がってくるので、非常に重要な作業です。
送付された椅子の籐編みの部分は、網目の1グリッドの籐の1本の幅と厚み、編み幅を測定して1網目の構成を設定してCADソフトで再現します。
基本構造は一般的に「クォーターアイソグリッド(QUARTER ISOGRID)」と呼ばれる六角形と三角形の配列です。こういった幾何学的構造は世界中に見受けられますが共通のようですね。
CAD上で再現した籐編みの部分
Formlabs社製3Dプリンタ『FORM2』で籐編みを模型で再現
ブラウザ上で、完成イメージをクライアントと共有
またAUTODESK社のFUSION360のデータ共有機能を使用し、CADをお持ちでない家具メーカー様と打合せが円滑に進むよう工夫しました。
これは、WEBブラウザーでデータが確認できるようデータ変換して共有リンクを作成するものです。画面中のスライドバーを動かすことで、形状を分解して表示する機能がある、大変優れモノのCAD/CAMソフトです。
CAD上で再現した第二弾『EASY CHAIR』の完成イメージ
オンライン上で、製品の完成イメージを確認しながらの打合せは、プロジェクト自体の精度がとても上がりますね。
バイオエポキシ樹脂の提案
チーム内での当初の製品イメージは、再生PET板材を使うことで、肘・脚・背などの基本部材は中空形状の製品を想定していました。
中空になることで軽量化を図れますが、家具として検討した場合、「中空で軽い椅子」よりも「中身の詰まった重量感の感じられる椅子」の方がREADYMADEが求めるデザインチェアとしては相応しいのではと思うようになりました。
大豆油をベースにした植物由来の素材
環境に配慮した透明な材料で、木材のように加工可能な材料を探索し、たどり着いた材料が『バイオエポキシ樹脂』になります。
このバイオエポキシ樹脂は、大豆油をベースにした植物由来の素材で構成されているので、今までの石油由来のエポキシ樹脂とは違い、環境負荷を極力低く抑えることができます。
また、水のように非常に透明性があり、今回のデザインチェアのイメージにより近いのではと考えました。
そこで弊社ではバイオエポキシ樹脂のテストピースを何点か作成してお客様に確認してもらい、承認をいただきました。
バイオエポキシ樹脂で板材を試作
次の段階は、EASY CHAIRの製造過程で必要となる板材の試作です。大きさも椅子のサイズをカバーできるものしました。
24mm厚のポリランバーコアに、離形テープを貼って型枠を製作。表面に離形剤をスプレーして、仕上がりの厚みが30mmになるよう多めにバイオエポキシ樹脂を注ぎ、硬化を待ちます。
バイオエポキシ樹脂には温度管理がMUST!
表面にある気泡は、注型の際にヒートガンで表面をあぶることで消すことができます。
また重要ポイントとして、室温は20℃から25℃以内になるように室温コントロールの必要があります。
硬化剤を混ぜると化学反応で樹脂自体が熱を持ち始めるので、温度が上がらないような対策が必要です。扇風機などを使用し、エアコンで温度設定した室内空気を部屋全体に循環させる必要があるのですが、思った以上に樹脂温度が上昇してしまいました!
下記写真にあるように、当初は樹脂の変形と収縮が発生して壁との間に隙間ができたりもしました。大きいところでは5mm以上の隙間ができてしまうので、バイオエポキシ樹脂を使用する際の温度管理は確実にMUSTですね!
完全硬化には時間を要するも、できた板材は完全な無色透明!
それからは成形不良が起きないようエアコンで温度管理をし、扇風機を部屋に持ち込み、空気を対流させて絶えず硬化具合を確認しました。
樹脂の注型の12時間後には、爪楊枝の先で表面を触ると少し糸を引くような粘着性を持ちます。それを経て徐々に硬度が増しつつ、完全に硬化するのを待ちます。
樹脂を型枠に注いだ後は温度管理が重要な反面、硬化に時間がかかるため気泡が抜け、水のように無色透明な板になります。
そして、完成したバイオ樹脂板を家具メーカー様に持ち込み、実際のデザインチェアの製作に入ってもらいます。
半透明なすりガラス調で第二弾『EASY CHAIR』完成!
しかしここで問題が起きました。
家具メーカー様からのお話として、加工の過程で透明だった箇所が白濁し、クリアな透明性を維持するのが非常に困難でした。
しかし、READYMADEデザイナー 細川雄太様に見ていただいたところ、「この半透明なすりガラス調の質感が、落ち着いたモダンな印象を放ち、逆に洗練されたデザインになってていい!」ということになりました。
結果、最終的にはこのすりガラス調の半透明を仕上げとして、しっとりとくる手触りの質感で製品化され、デザイナーにも満足していただける仕上がりとなりました。
家具メーカー様での製作過程の様子
すりガラス調の半透明のデザインチェアとして完成!
Designer : Yuta Hosokawa
Instagram : @readymade_official
Official HP:http://www.readymade-official.com/
ブランドネームであるREADYMADE には既製品に対しての
アンチテーゼが込められている。
本来、不要なものとして廃棄されていくようなものを循環させ、
新たな姿に生まれ変わらせるブランドでもある。
READYMADEの頭文字でもある“RE”から派生した
数々の“RE”にまつわるプロダクトを提案。
RESPECT, RECONSIDER, RECUNSTRUCT,……etc.
新しい挑戦にこそモノづくりの楽しみがある
こういったトラブルを受け入れ、そして乗り越えることで、モノづくりの大変さや喜びをお客様と共有したいと関東製作所は考えています。
今回の製作事例のように、当初のイメージは透明だったのですが、結果半透明だからこそ表現できた偶然のこの産物。世界でも稀有なデザインチェアとして世に中に発表でき、一部ながらでも協力できたことに喜びを禁じえません。
※色付きのバイオエポキシ樹脂のテストピースも製作してみました。このような取り組みが次につながります。
モノづくりの可能性は無限大です。
特に昨今は、我々プラスチックを扱う事業者にとっても、環境に配慮した樹脂材への取り組みをより一層深めていかなければならない時代です。
まだまだ未知の領域であるがゆえに、そこには『挑戦』が必要です。
そして、まるで子どものような純粋な心でモノづくりを楽しむことも大切でしょう。
モノづくりの現場も、新しいステージへと移行します。
私ども関東製作所は、製造業という枠を超えた新たな挑戦のモノづくりで、創造性の豊富な市場を切り開いて参ります。
> 「サスティナブル×ものづくり」への参画 レディメイド製デザインチェアのテストピース作成ストーリー
> バイオプラスチックを知る 製造現場から考える環境問題を意識した次世代プラスチック素材とは